Ultimate Guide to Process Standardization: Strategies for Operational Excellence
As businesses survive to run like well-oiled machines, having standard methods, like process standardization, for how work gets done has become even more important than ever.
Companies are always looking for ways to boost productivity, cut waste, and provide top-notch products and services consistently.
This is where setting guidelines for procedures comes into play by helping streamline systems and constantly improve operations.
It involves laying out uniform steps and rules for handling specific tasks and responsibilities within an organization.
Mapping out and writing down these processes means everyone follows the same set of best practices no matter where they are located or what job they do.
This consistency is key to performing at a high level because it minimizes differences in outcomes, errors, and helps ensure high-quality control overall.
Key Highlights
- A clear definition of process standardization and its importance in achieving operational excellence
- The numerous benefits of process standardization
- An overview of the different types of process standardization
- A step-by-step methodology for implementing process standardization
- The role of process mapping in standardization, including a visual representation of process steps
- Guidelines for implementing Standard Operating Procedures (SOPs), including step-by-step instructions, best practices, and compliance with regulations
- An exploration of process standardization tools and software, and the benefits of process automation
- Strategies for overcoming challenges in process standardization, and best practices for successful implementation
In this article, I will draw upon my expertise in Six Sigma, Design for Six Sigma (DFSS), and statistical thinking to provide a detailed exploration of process standardization.
Introduction to Process Standardization
In the relentless pursuit of operational excellence, organizations must continuously strive to streamline their processes, eliminate waste, and deliver consistent, high-quality outputs.
This pursuit has given rise to the critical practice of process standardization, a structured approach that has become indispensable in today’s dynamic business landscape.
Definition of Process Standardization
It involves establishing uniform procedures and guidelines for performing specific organizational tasks and activities.
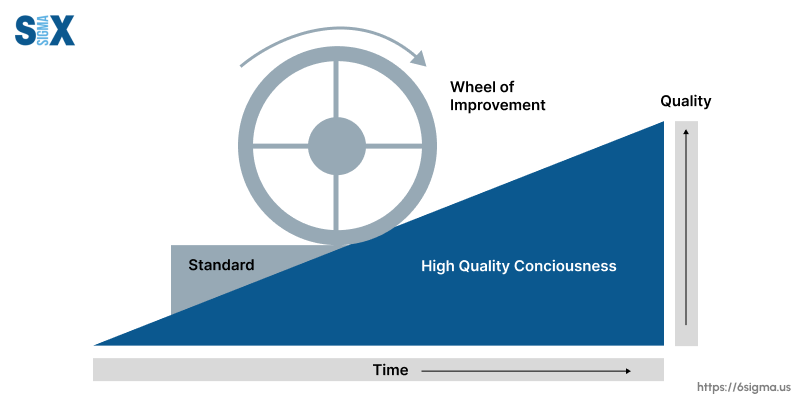
By clearly defining and documenting these processes, companies ensure that every employee, regardless of their location or role, follows the same set of best practices.
This consistency is paramount in achieving operational excellence, as it minimizes variations in performance, reduces errors, and enhances overall quality control.
Importance of Standardized Processes
The importance of standardized processes cannot be overstated in today’s fast-paced and ever-evolving business environment.
Standardized procedures lead to consistency, efficiency, cost savings, and a competitive edge.
Achieving Operational Excellence
This is the ultimate goal of process standardization, and it is a journey that requires unwavering commitment and continuous improvement.
Benefits of Process Standardization
The implementation of process standardization is a strategic decision that yields far-reaching benefits for organizations of all sizes and across various industries.
Consistency and Quality Control
One of the most significant advantages of process standardization is the consistency and quality control it brings to an organization’s operations.
This level of consistency not only enhances customer satisfaction but also reinforces brand reputation and trust.
Improved Efficiency and Productivity
Standardized processes are inherently optimized for efficiency, eliminating unnecessary steps, redundancies, and bottlenecks that can hinder productivity.
When employees follow well-defined and streamlined procedures, they can focus their efforts on value-adding activities, ultimately increasing their output and contributing to the organization’s overall productivity.
Streamlined Training and Onboarding with Process Standardization
The presence of standardized processes greatly simplifies the training and onboarding process for new employees.
With clearly documented procedures and guidelines, organizations can quickly familiarize new hires with the established methods and expectations, reducing the learning curve and allowing them to become productive members of the team in a shorter timeframe.
This not only enhances the overall efficiency of the organization but also contributes to employee satisfaction and retention.
Facilitated Process Analysis and Improvement
Standardized processes provide a solid foundation for continuous process analysis and improvement.
By establishing a consistent baseline, organizations can more effectively identify areas for optimization, measure performance against defined metrics, and implement targeted improvements.
Compliance with Industry Regulations
In many industries, adherence to regulatory guidelines and standards is a critical aspect of operations.
Process standardization plays a vital role in ensuring compliance by embedding these requirements into the organization’s procedures and workflows.
Cost Savings and Waste Reduction
By optimizing processes and eliminating inefficiencies, process standardization directly contributes to cost savings and waste reduction within an organization.
Streamlined procedures minimize the consumption of unnecessary resources, reduce the likelihood of errors and rework, and promote the efficient utilization of available assets.
These cost savings can be reinvested into other areas of the business, fueling growth and innovation.
Competitive Advantage
Process standardization can be a powerful differentiator, providing organizations with a significant competitive edge.
By delivering consistent quality, enhancing operational efficiency, and reducing costs, standardized processes enable companies to offer superior products and services at competitive prices.
This, in turn, attracts and retains customers, driving long-term success and market dominance.
Types of Process Standardization
Process standardization is a comprehensive endeavor that encompasses various aspects of an organization’s operations.
By understanding these different types, organizations can develop a holistic approach to process standardization, ensuring consistency and efficiency across all facets of their operations.
Document Standardization
This is a critical aspect of process standardization, as it establishes uniformity and consistency in the creation, formatting, organization, and management of documents within an organization.
This type of standardization ensures that all digital or physical documents adhere to predefined guidelines, fostering a consistent and professional appearance.
Workflow Standardization
Workflow standardization involves defining the sequence in which tasks are performed, ensuring that all employees follow the same steps for a given process.
This type of standardization reduces variability and enhances predictability, as individuals clearly understand their roles and contributions to the organization’s overall processes.
Communication Standardization
Effective communication is vital for any organization, and communication standardization addresses the flow of information within an organization.
This type of standardization defines reporting structures, escalation paths, and protocols for disseminating information to relevant stakeholders.
Resources Standardization
Resources standardization addresses matters related to the allocation, utilization, and management of resources within an organization. This includes tangible assets, human resources, and technology.
By standardizing resource management, organizations can ensure efficient and effective use of their assets while reducing the risk of losses and promoting a safe working environment.
Policy Standardization
Policy standardization establishes guidelines and rules that govern various aspects of organizational behavior, decision-making, and operations. It sets the codes of conduct within the entire organization and ensures adherence to legal and regulatory requirements.
Performance Metric Standardization
Performance metric standardization puts forward uniform criteria for measuring and evaluating the performance of individuals, teams, processes, or the overall organization.
It specifies the key performance indicators (KPIs) relevant to each role or process, ensuring everyone understands what is being measured.
Customer Service Standardization
Delivering exceptional customer experiences is paramount. Customer service standardization ensures that customers receive a consistent and positive experience across various interactions with an organization.
This type of standardization involves establishing clear standards for service quality, communication protocols, issue resolution processes, and response times, and ensuring that service representatives are well-informed and equipped to accurately address customer queries.
Process Standardization Methodologies
Implementing process standardization is a structured endeavor that requires a systematic approach.
I have developed and refined a methodology that encompasses a series of critical steps, each building upon the previous one to ensure a successful and sustainable implementation.
This proven methodology serves as a blueprint for organizations embarking on their process standardization journey, guiding them from the initial identification and mapping of processes to the continuous monitoring and improvement of standardized procedures.
Identifying and Mapping Processes
The first step in the process standardization methodology is to identify and map the organization’s core processes.
This involves pinpointing specific processes that may be causing bottlenecks, inconsistencies, or impacting customer satisfaction, as well as tasks that are being executed in multiple ways across different departments or locations.
By thoroughly documenting these processes, organizations can capture every step, decision point, and handoff involved, providing a comprehensive understanding of the current state.
Process Analysis and Benchmarking
Once the current processes have been mapped, the next step is to analyze them for efficiency and effectiveness.
This analysis involves identifying areas for improvement, streamlining workflows, and eliminating redundancies or unnecessary steps.
Designing Standard Operating Procedures (SOPs)
With a clear understanding of the current processes and areas for improvement, organizations can then design and document standardized procedures, known as Standard Operating Procedures (SOPs).
These SOPs provide a structured set of instructions that guide employees through the execution of specific tasks and processes, outlining the sequence of activities, responsible parties, checkpoints, and decision points.
Testing and Validating Standardized Processes
Before implementing the standardized processes across the organization, it is crucial to test and validate them on a smaller scale.
This pilot phase allows organizations to closely monitor performance, assess the effectiveness of the changes, and make any necessary adjustments based on real-world feedback and data.
Employee Training and Change Management
Successful process standardization requires buy-in and adoption from employees at all levels.
Organizations must prioritize comprehensive training programs to ensure that employees understand the new standardized processes, their roles and responsibilities, and the rationale behind the changes.
Effective change management strategies, such as clear communication, stakeholder engagement, and ongoing support, are essential for facilitating a smooth transition and minimizing resistance.
Continuous Monitoring and Improvement
Process standardization is not a one-time effort but rather an ongoing journey of continuous improvement.
Organizations must continuously monitor the performance of standardized processes, collect feedback from employees and customers, and analyze data to identify opportunities for further optimization.
Regular audits, process reviews, and a culture of continuous learning and adaptation are vital to ensuring that standardized procedures remain effective, efficient, and aligned with the organization’s evolving needs.
Utilizing Process Mapping
Process mapping is a critical tool in the process standardization methodology, providing a visual representation of the steps involved in a process.
Visual Representation of Process Steps
Process maps use flowcharts, diagrams, or other visual aids to illustrate the sequence of activities, decision points, and handoffs involved in a process.
This visual representation enhances comprehension and ensures that all stakeholders have a shared understanding of the process, reducing ambiguity and miscommunication.
Identifying Inefficiencies and Bottlenecks
By mapping out processes, organizations can identify areas where inefficiencies or bottlenecks may exist.
This could include unnecessary steps, redundant activities, or points of excessive waiting or rework.
Process mapping provides a clear overview of the entire process, enabling organizations to pinpoint and address these inefficiencies, streamline workflows, and optimize resource utilization.
Facilitating Communication and Training
Process maps serve as valuable communication and training tools, allowing organizations to effectively convey process information to employees, stakeholders, and new hires.
By visualizing the process flow, organizations can ensure consistent understanding and execution, facilitating knowledge transfer and enabling more effective training programs.
Implementing Standard Operating Procedures (SOPs) for Process Standardization
Standard Operating Procedures (SOPs) are the cornerstone of process standardization, providing a structured set of instructions that guide employees through the execution of specific tasks and processes.
Implementing SOPs is a critical step in ensuring consistency, quality, and efficiency across an organization’s operations.
Step-by-step Instructions
SOPs should include clear, step-by-step instructions that outline the sequence of activities to be performed, as well as any relevant decision points, checkpoints, or contingencies.
These detailed instructions eliminate ambiguity and ensure that every employee follows the same proven and optimized approach, regardless of their role or location within the organization.
Best Practices and Guidelines
In addition to procedural instructions, SOPs should incorporate best practices and guidelines that have been established through industry experience, regulatory requirements, or internal process optimization efforts.
These best practices serve as a framework for ensuring that processes are executed in a manner that promotes efficiency, quality, and compliance.
Compliance with regulations
For industries subject to regulatory oversight or specific compliance requirements, SOPs play a crucial role in ensuring adherence to these standards.
By embedding regulatory guidelines and requirements directly into the documented procedures, organizations can mitigate the risk of non-compliance and associated penalties, demonstrating a commitment to upholding industry best practices and fostering customer trust and confidence.
Process Standardization Tools and Software
The successful implementation and management of standardized processes often rely on the effective utilization of specialized tools and software.
These technological solutions not only streamline the process standardization journey but also provide organizations with the necessary insights, automation capabilities, and monitoring mechanisms to ensure sustained success.
Business Process Management Systems (BPMS)
Business Process Management Systems (BPMS) are powerful software platforms designed to facilitate the design, execution, and optimization of business processes.
These systems leverage advanced modeling and automation capabilities, enabling organizations to visually represent their processes, identify opportunities for improvement, and implement streamlined workflows.
Process documentation and mapping tools
Process documentation and mapping tools are essential components of any process standardization initiative.
These tools enable organizations to capture, visualize, and document their processes in a structured and easily understandable format.
By creating detailed process maps, flowcharts, and diagrams, organizations can enhance transparency, facilitate communication, and ensure a shared understanding of processes among stakeholders.
Workflow automation and process tracking
Workflow automation and process tracking tools play a crucial role in streamlining and monitoring standardized processes.
These solutions automate repetitive tasks, enforce predefined process rules, and route work items to the appropriate individuals or systems.
Quality control and monitoring solutions
Ensuring the consistent execution of standardized processes is paramount to achieving the desired outcomes.
Quality control and monitoring solutions assist organizations in maintaining process integrity by continuously monitoring adherence to established standards and identifying deviations.
Benefits of Process Automation
While process standardization lays the foundation for operational excellence, the integration of automation technologies amplifies its impact, unlocking a myriad of benefits that can transform an organization’s performance and competitiveness.
Reducing manual effort and errors
One of the primary advantages of process automation is the reduction of manual effort and the associated potential for human errors.
Streamlining workflows
Process automation streamlines workflows by eliminating unnecessary steps, optimizing resource utilization, and ensuring seamless integration between different systems and departments.
Real-time monitoring and reporting
Automated processes generate a wealth of data that can be leveraged for real-time monitoring and reporting.
Organizations can gain visibility into process performance metrics, identify bottlenecks, and track key performance indicators (KPIs) in real time.
Overcoming Challenges in Process Standardization
While the benefits of process standardization are undeniable, its implementation is not without challenges.
Overcoming these challenges requires a strategic approach, effective change management, and a steadfast commitment to continuous improvement.
Managing resistance to change
One of the most significant challenges in process standardization is managing resistance to change.
Employees may be hesitant to adopt new processes, particularly if they are deeply entrenched in established working methods. This resistance can stem from various factors, such as fear of the unknown, perceived loss of autonomy, or concerns about increased workload.
Balancing standardization and flexibility
While standardization promotes consistency and efficiency, it is important to strike a balance between rigid processes and the flexibility required to adapt to unique situations or changing business needs.
Organizations must be cautious not to stifle creativity and innovation in their pursuit of standardization.
Ensuring ongoing compliance
Certain industries are subject to stringent regulations and compliance requirements, which can pose challenges to process standardization.
Companies must ensure that their standardized processes align with these external mandates and are regularly updated to reflect any changes in regulatory landscapes.
Fostering a culture of continuous improvement
Process standardization is not a one-time endeavor; it is a continuous journey of refinement and optimization. Fostering a culture of continuous improvement is crucial to sustaining the benefits of standardization over the long term.
Best Practices for Successful Implementation
Several best practices can significantly enhance the likelihood of success and maximize the benefits of this transformative endeavor.
Engaging stakeholders and subject matter experts
Engaging stakeholders and subject matter experts from the outset is crucial for ensuring the success of process standardization initiatives.
By involving individuals with diverse perspectives and in-depth knowledge of the processes being standardized, organizations can gain valuable insights, identify potential challenges, and develop solutions that are tailored to their specific needs.
Starting small and scaling gradually
While the temptation to standardize all processes simultaneously may be strong, it is often more effective to adopt a phased approach.
By starting with a smaller subset of processes and demonstrating early wins, organizations can build momentum, refine their methodologies, and address any potential issues before scaling standardization efforts across the entire organization.
Providing comprehensive training and support
Effective training and ongoing support are essential for ensuring the successful adoption and sustained implementation of standardized processes.
Companies should invest in developing comprehensive training programs that not only cover the technical aspects of the new processes but also emphasize the rationale behind the changes and the expected benefits.
Promoting a culture of process improvement
While standardization is a critical step toward operational excellence, it should not be viewed as a static endpoint.
Organizations must cultivate a culture of continuous process improvement, encouraging employees to identify opportunities for further optimization and actively participate in refining standardized processes.
Case Studies of Process Standardization
The transformative power of process standardization is evident across numerous industries, where organizations have leveraged this methodology to drive operational excellence, enhance customer experiences, and gain a competitive edge.
Process standardization in manufacturing
In the manufacturing sector, process standardization has played a pivotal role in ensuring consistent quality, reducing production costs, and optimizing supply chain operations.
One notable example is Toyota’s New Global Architecture (TNGA), a platform strategy developed to standardize and streamline the development of its vehicles.
Process standardization in retail
Delivering exceptional customer experiences is paramount.
Retailers such as Zappos, the renowned online shoe retailer, have leveraged process standardization to empower their customer service representatives with the authority to resolve customer complaints efficiently and consistently.
By standardizing issue resolution processes and providing representatives with clear guidelines and decision-making autonomy, Zappos has achieved faster resolution times and higher customer satisfaction levels, setting a benchmark for the industry.
Process standardization in healthcare services
The healthcare sector has also embraced process standardization to improve patient outcomes, enhance operational efficiency, and ensure compliance with regulatory requirements.
The Mayo Clinic, a prestigious medical institution, standardized its clinical pathways for common procedures, including preoperative testing, medication administration, and post-operative care.
Success Stories and Lessons Learned
These case studies illustrate the profound impact of process standardization across diverse industries. However, the path to success is not without its challenges.
Organizations that have successfully navigated this journey often cite the importance of strong leadership, effective change management strategies, and an unwavering commitment to continuous improvement.
The Future of Process Standardization
As we look toward the future, the landscape of process standardization is poised to evolve rapidly, driven by emerging technologies and innovative approaches.
Emerging Trends and Technologies
One of the most significant trends shaping the future of process standardization is the integration of advanced technologies such as artificial intelligence (AI), machine learning, and advanced analytics.
The Role of Artificial Intelligence and Automation
Artificial intelligence and automation will play a pivotal role in the future of process standardization. AI-powered systems will be able to analyze process data, identify patterns and anomalies, and suggest optimizations in real time.
Continuous Process Optimization strategies
As organizations embrace the power of data and advanced technologies, continuous process optimization will become a core competency.
Organizations will need to adopt agile methodologies and implement feedback loops that enable them to rapidly iterate and refine their standardized processes in response to changing market conditions, customer demands, and technological advancements.
Conclusion
Setting standard processes has shown its worth for all sorts of businesses and industries.
It’s difficult to emphasize enough just how important having standard methods is.
It truly forms the basis for performing at top-notch levels, letting companies reliably provide excellent products and service while also adapting to shifts in the market demands down the road.
When new challenges appear, those with established procedures find it much easier to adjust without missing a beat. Overall, streamlining tasks through standardization sets the stage for the success of any organization in both the short and long haul.
While not a magic solution alone, it equip teams with a tremendous advantage over those without clear ground rules. In the end, process standardization time and again proves a transformational practice worth pursuing for any serious about excellence.
SixSigma.us offers both Live Virtual classes as well as Online Self-Paced training. Most option includes access to the same great Master Black Belt instructors that teach our World Class in-person sessions. Sign-up today!
Virtual Classroom Training Programs Self-Paced Online Training Programs