Operational Improvement: Strategies, Implementation, and Best Practices
According to McKinsey research, companies that excel in operational improvement achieve 25% higher productivity and 20% lower operating costs than their competitors.
These numbers highlight why businesses across industries are focusing on refining their operations.
Today’s competitive market demands more than just maintaining the status quo. Organizations must constantly evolve their processes, optimize resources, and boost efficiency to stay ahead.
Operational improvement offers a structured approach to achieve these goals while driving sustainable growth.
Key Highlights
- Process optimization and efficiency gains
- Strategic planning and implementation steps
- Performance measurement techniques
- Team engagement and change management
- Technology integration for better results
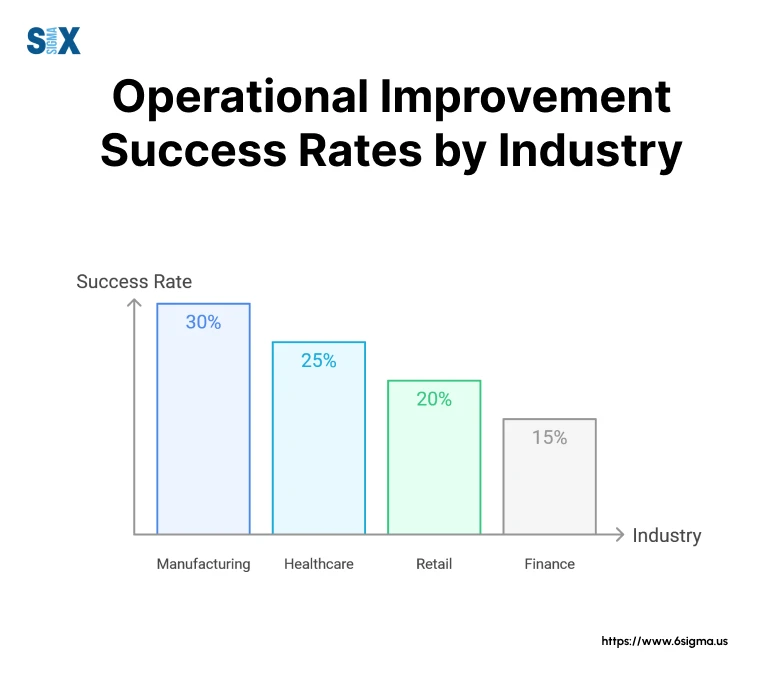
What Is Operational Improvement?
Operational improvement transforms how organizations work by optimizing processes, reducing waste, and boosting productivity.
This systematic approach helps businesses deliver better products and services while maximizing resource utilization.
Moving Beyond Basic Efficiency
While operational efficiency focuses on doing things right, operational improvement strategies target both effectiveness and efficiency.
Think of efficiency as running a machine at its fastest speed, while improvement involves upgrading the machine itself.
For example, a manufacturing plant might run its assembly line efficiently, but operational improvement would redesign the line to eliminate bottlenecks and reduce defects.
Essential Building Blocks of Operational Improvement
Successful operational improvement rests on four key pillars:
- Process Optimization: Streamlining workflows and eliminating redundant steps
- Resource Management: Making the best use of time, money, and human capital
- Quality Control: Building systems that prevent errors and maintain standards
- Innovation Integration: Adopting new technologies and methods to enhance operations
Master the fundamentals of process improvement with our Yellow Belt Certification program
earn essential tools like Process Mapping, C&E Matrix, and FMEA to drive meaningful change in your organization.
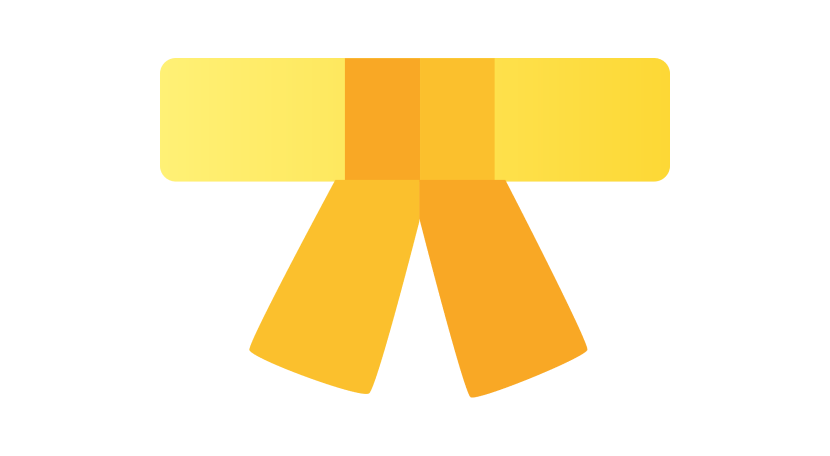
The Business Impact
Organizations that implement strong operational improvement strategies see measurable gains across multiple areas.
Manufacturing firms report up to 30% reduction in production costs, while service-based businesses note 40% faster delivery times. These improvements directly affect the bottom line through:
- Lower operating costs
- Increased customer satisfaction
- Better employee engagement
- Higher market competitiveness
- Stronger brand reputation
The banking sector offers a clear example of operational improvement in action.
By redesigning their loan approval process, banks have cut processing times from weeks to days while reducing errors by 50%.
This improvement not only saves money but also creates happier customers and more engaged employees.
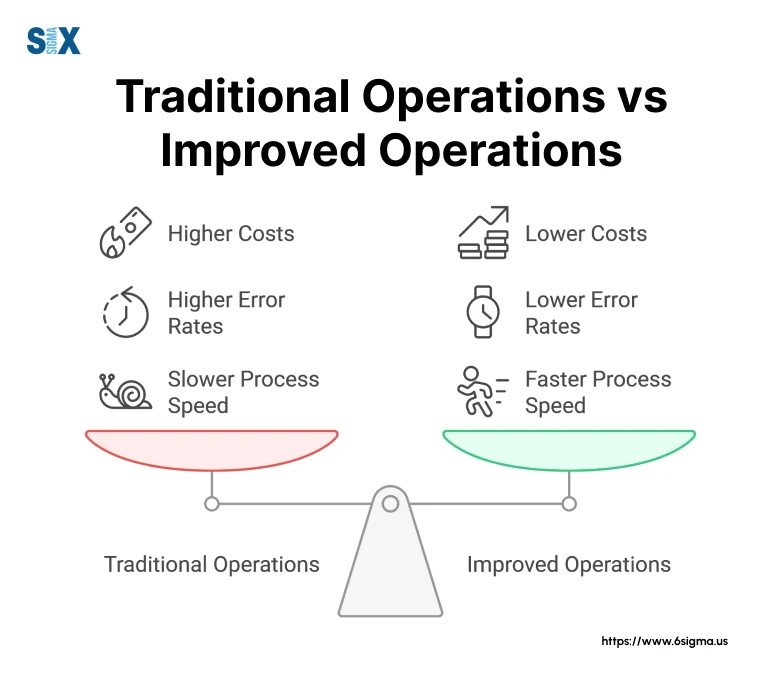
When implemented correctly, operational improvement becomes a driving force for business growth.
It creates a culture of continuous advancement where teams constantly look for ways to work smarter, not just harder.
The Five Phases of Operational Improvement
Successful operational improvement follows a structured cycle that drives lasting change. Each phase builds upon the previous one, creating a framework for sustained progress and measurable results.
Phase 1: Assessing Current Performance
The cycle begins with a thorough review of existing operations. This means analyzing current processes, identifying bottlenecks, and gathering data on key performance metrics.
For example, a retail chain might track customer wait times, inventory turnover rates, and staff productivity levels to pinpoint areas needing improvement.
Phase 2: Setting Clear Goals with Operational Improvement
Based on the assessment findings, organizations must establish specific, measurable targets.
These goals should align with broader business objectives while remaining realistic and achievable.
A manufacturing plant might aim to reduce production waste by 20% within six months or decrease machine downtime by 15% over a quarter.
Phase 3: Executing Changes
The operational improvement execution phase transforms plans into action.
This involves:
- Rolling out new processes
- Training staff on updated procedures
- Implementing supporting technologies
- Managing the transition period
Success during this phase depends heavily on clear communication and strong leadership support. Teams need to understand not just what’s changing, but why these changes matter.
Phase 4: Measuring Results of Operational Improvement
Regular monitoring helps track progress and identify necessary adjustments.
Organizations should:
- Track key performance indicators
- Compare results against baseline metrics
- Document unexpected outcomes
- Gather feedback from staff and stakeholders
Phase 5: Refining and Continuing
Continuous operational improvement means never settling for “good enough“. Using insights from the monitoring phase, organizations can fine-tune their approaches and start the cycle again with new targets.
This ongoing process ensures operations keep evolving with market demands and technological advances.
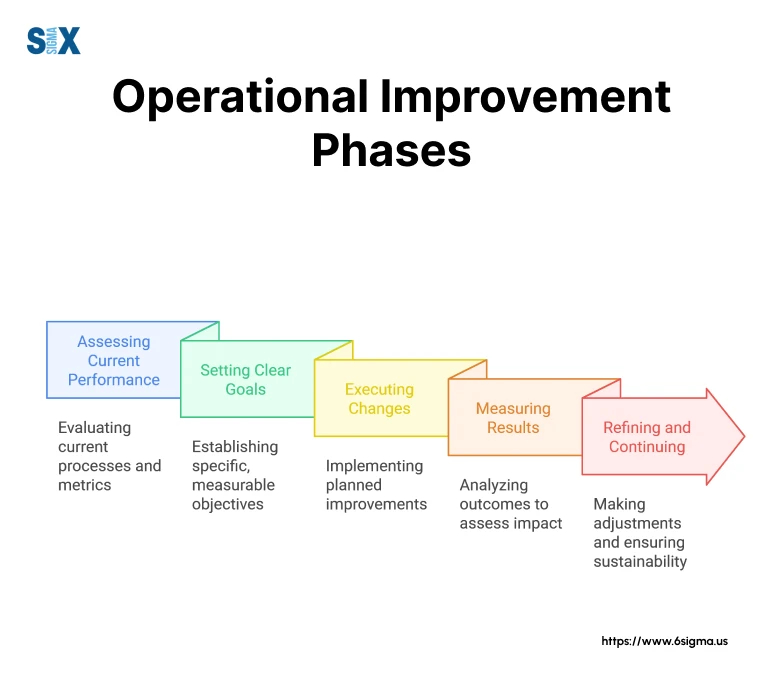
This cyclical approach to operational improvement delivers consistent results while building a culture of excellence.
Organizations that commit to this process often see sustained gains in efficiency, quality, and employee engagement.
Creating Your Operational Improvement Plan
A well-structured operational improvement plan serves as your roadmap to enhanced business performance.
Organizations that invest time in proper planning typically achieve their improvement goals 60% faster than those who rush into implementation.
Building The Foundation
Start by identifying specific areas that need improvement.
A manufacturing company might focus on reducing production delays, while a service business could target customer response times.
Document current performance metrics to establish clear baseline measurements.
Next, outline specific goals with measurable targets. Rather than stating “improve customer service”, set concrete objectives like “reduce customer wait times from 10 minutes to 5 minutes within three months.”
This specificity makes progress tracking easier and helps maintain team focus.
Essential Plan Components of Operational Improvement
Your operational improvement plan should include:
- Timeline: Break down implementation into phases with specific deadlines
- Resource allocation: Detail required budget, staff, and tools
- Risk assessment: Identify potential obstacles and mitigation strategies
- Success metrics: Define KPIs to measure progress
- Training requirements: Outline necessary skill development programs, including those covered in our Six Sigma Certification programs
Connecting With Business Goals
Every improvement initiative must support broader organizational objectives.
For example, if your business aims to increase market share by 15%, your operational improvement plan might focus on scaling production capacity or enhancing service delivery speed.
Engaging Key Stakeholders in Operational Improvement
Successful implementation requires buy-in from all levels of the organization.
Department heads need to understand how changes affect their teams, while front-line workers must see the benefits of new processes.
Regular meetings and feedback sessions help ensure everyone stays aligned with improvement goals.
Sample Plan Framework
Consider this example from a retail chain’s operational improvement plan:
Goal: Reduce inventory management costs by 25%
Timeline: 6 months
Actions:
- Install automated inventory tracking system (Month 1-2)
- Train staff on new system (Month 2-3)
- Implement new ordering protocols (Month 3-4)
- Monitor and adjust processes (Month 4-6)
Success Metrics:
- Storage costs
- Order accuracy rates
- Stock turnover speed
- Employee productivity
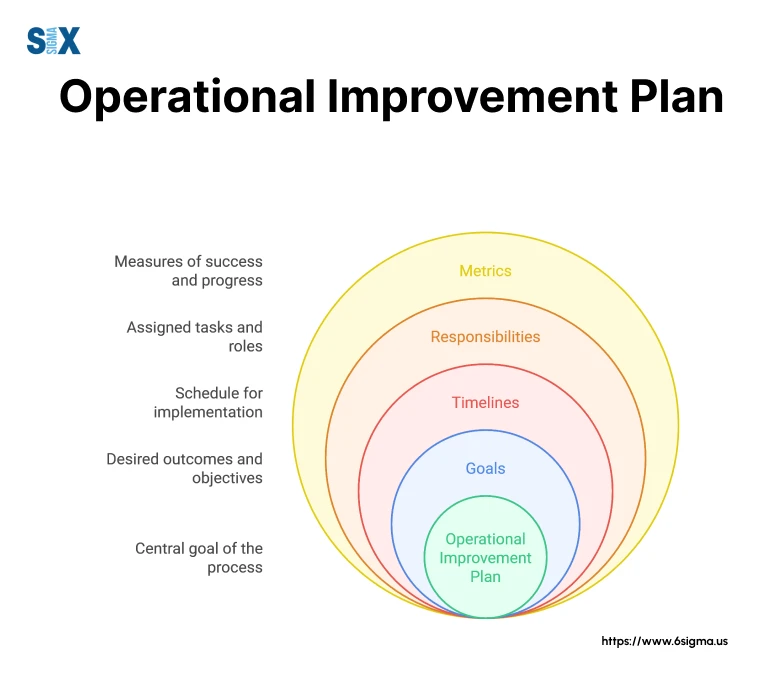
Remember, flexibility remains crucial.
The best operational improvement plans allow for adjustments based on real-world implementation feedback and changing business conditions.
Proven Strategies For Operational Improvement
Modern businesses need robust operational improvement strategies to stay competitive.
The right mix of methodologies, tools, and techniques can boost productivity by up to 35% while reducing operational costs by 25%.
Process Mapping For Better Results
Process mapping reveals inefficiencies and bottlenecks in current operations. By creating visual representations of workflows, organizations spot redundant steps and improvement opportunities.
A healthcare facility using process mapping identified that patient discharge paperwork went through seven unnecessary steps, leading to delays.
After streamlining the process, discharge times decreased by 45%.
Get certified in Process Variables Mapping and learn how to identify critical improvement opportunities.
Implementing Lean Management
Lean principles focus on eliminating waste while maximizing value.
Implementing Lean Management requires understanding core fundamentals of Lean, which focus on eliminating waste while maximizing value.
This strategy works across industries – from manufacturing to service sectors. Key lean concepts include:
- Value stream mapping
- Just-in-time delivery
- 5S workplace organization
- Pull systems
- Standard work procedures
A food processing plant applying lean principles reduced inventory costs by 30% and improved production speed by 25% within six months.
Six Sigma Excellence
Six Sigma methodology targets defect reduction and process consistency.
This data-driven approach uses statistical analysis and analyzing the root causes to identify and fix problems.
Organizations implementing Six Sigma typically see:
- Reduced error rates
- Lower operational costs
- Improved customer satisfaction
- Better quality control
- Enhanced process stability
Elevate your operational improvement expertise with our comprehensive Green Belt certification
Technology And Automation Integration
Modern operational improvement ideas leverage technology to enhance efficiency. Smart factories using IoT sensors report 20% higher productivity than traditional setups.
Automation tools handle routine tasks, allowing staff to focus on strategic activities.
Examples of effective technology integration:
- Automated inventory management systems
- Predictive maintenance software
- Digital workflow platforms
- Real-time monitoring tools
- AI-powered quality control
Employee Development Programs for Operational Improvement
Staff training drives operational efficiency strategy success. Organizations must invest in:
- Skills development workshops
- Cross-training opportunities
- Leadership development
- Technical certification programs
- Continuous learning initiatives
Companies with strong training programs see 24% higher profit margins than those without structured development plans.
Measuring Success Through KPIs
Effective performance metrics track improvement progress. Key indicators might include:
- Production efficiency rates
- Quality metrics
- Customer satisfaction scores
- Employee productivity levels
- Cost per unit
- Time to market
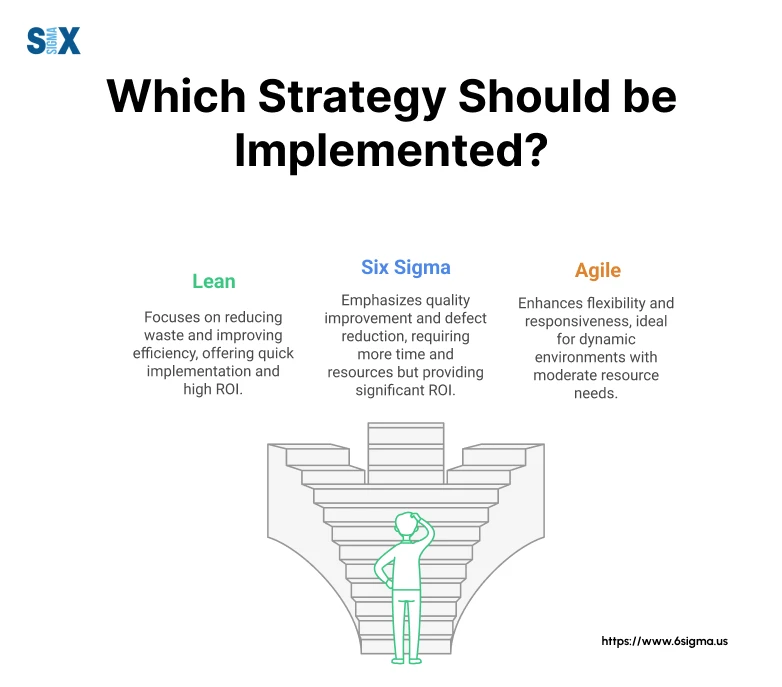
The most successful operational improvement programs combine multiple strategies based on specific business needs.
Regular assessment helps determine which approaches deliver the best results for your organization.
Turning Operational Improvement Plans Into Reality
Managing operational improvement requires more than just good ideas – it demands careful execution and strong leadership.
Managing Change Effectively
Successful change management starts with clear leadership vision and support. Organizations must create a structured approach that addresses both technical and human aspects of change.
This means establishing clear roles, responsibilities, and expectations while providing necessary resources and support systems.
Department heads should serve as change champions, actively demonstrating commitment to new processes and procedures.
When leaders actively participate in realizing operational improvement, employee buy-in increases by 45%.
Breaking Through Resistance with Operational Improvement
Employee resistance often stems from fear of the unknown or concern about job security. Address these concerns head-on through:
- Regular updates about progress and impact
- Clear explanations of how changes benefit employees
- Open forums for questions and feedback
- Recognition of employee contributions
- Quick wins that demonstrate positive results
Testing And Scaling Solutions with Operational Improvement
Start with pilot programs in controlled environments. A manufacturing plant might test new procedures on one production line before rolling out changes facility-wide. This approach allows for:
- Risk minimization
- Process refinement
- Real-world validation
- Employee familiarization
- Evidence-based scaling decisions
Building Strong Communication Channels
Effective communication drives successful implementation. Create a multi-channel approach using:
- Team meetings and briefings
- Digital updates and newsletters
- Visual management boards
- Progress tracking dashboards
- Feedback collection systems
Organizations with strong communication strategies report 23% higher success rates in operational improvement initiatives.
Supporting Your Team
Provide robust training and support throughout the implementation process. This includes:
- Initial skills training
- Ongoing coaching sessions
- Resource materials and guides
- Help desk support
- Regular check-ins and progress reviews
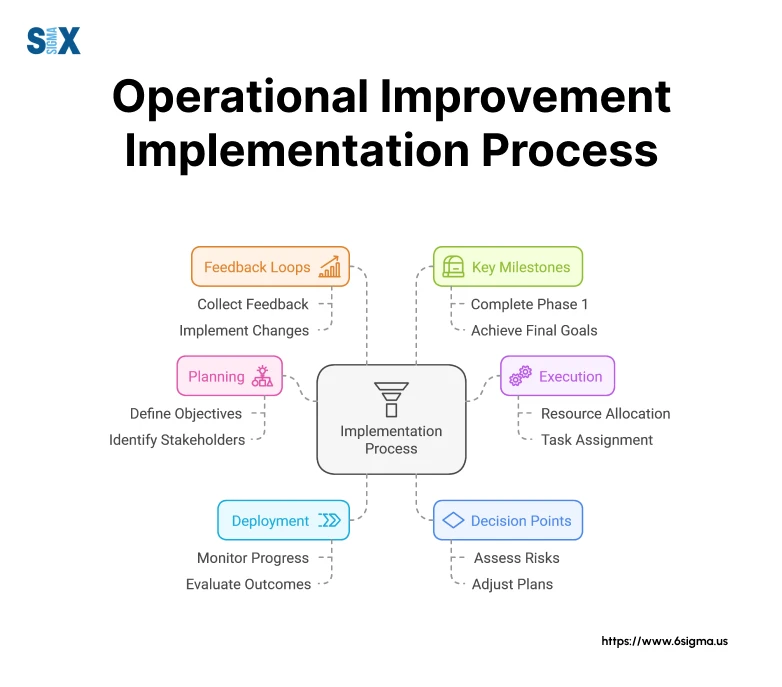
Remember that implementing operational improvements takes time.
Organizations that rush the process often face setbacks that could have been avoided through proper planning and support.
Tracking Your Operational Improvements
Success in operational performance improvement depends on robust measurement systems.
Organizations that regularly track their progress are twice as likely to achieve their improvement goals compared to those that don’t measure systematically.
Essential Performance Indicators
Different industries require specific KPIs to measure operational efficiency.
Manufacturing companies might focus on production cycle times and defect rates, while service organizations track customer satisfaction scores and response times.
- Key metrics often include:
- Productivity rates
- Resource utilization
- Quality standards
- Cost per unit
- Customer satisfaction levels
- Employee engagement scores
Measurement Tools And Methods of Operational Improvement
Modern technology offers various tools to track operational improvements. Digital platforms can automatically collect and analyze data, providing real-time insights into performance.
For example, automated tracking systems can monitor machine downtime, while customer relationship management tools measure service delivery speeds.
Statistical process control charts help identify variations in performance, while trend analysis reveals patterns over time. These tools enable managers to spot issues before they become major problems.
Building Effective Dashboards for Operational Improvement
Dashboards should present data in clear, actionable formats. The most effective dashboards include:
- Real-time performance metrics
- Historical trend comparisons
- Target vs. actual results
- Alert systems for deviations
- Drill-down capabilities for detailed analysis
Ongoing Monitoring Strategies
Regular monitoring helps maintain momentum in operational improvement initiatives. Establish weekly review meetings to discuss performance data and address emerging issues.
Monthly deep-dive sessions can examine longer-term trends and adjust strategies accordingly.
- Create standardized reporting templates that highlight:
- Performance against targets
- Areas needing attention
- Success stories and best practices
- Resource allocation effectiveness
- Recommended adjustments
Organizations should adjust their monitoring approaches based on results and changing business needs. This flexibility ensures the measurement system remains relevant and valuable over time.
Overcoming Obstacles In Operational Improvement
Even well-planned operational process improvement initiatives face challenges.
Common Implementation Roadblocks
Budget constraints often top the list of challenges when trying to improve operational processes. Organizations frequently underestimate the resources needed for training, technology upgrades, and temporary productivity dips during transition periods.
Employee resistance presents another major hurdle. Staff members may feel threatened by new processes or struggle to adapt to changing workflows.
This resistance can slow implementation and reduce the effectiveness of improvement efforts.
Technical difficulties also emerge during system upgrades or process changes. Legacy systems might not integrate well with new solutions, while data migration can cause unexpected disruptions to daily operations.
Strategic Solutions For Success
Successful organizations tackle these challenges through careful planning and flexible approaches.
Breaking large improvements into smaller, manageable phases helps manage budget constraints while maintaining momentum.
This approach allows teams to demonstrate quick wins and build support for larger changes.
To address employee concerns, create detailed transition plans that include:
- Regular training sessions
- Clear communication channels
- Recognition programs
- Support systems
- Progress tracking
Sustaining Long-Term Progress
Maintaining momentum requires ongoing attention and effort. Regular review meetings help identify emerging issues before they become major problems.
Celebrating small victories and sharing success stories keeps teams engaged and motivated.
Organizations that successfully maintain their operational improvement initiatives typically establish:
- Monthly progress reviews
- Quarterly strategy adjustments
- Annual goal setting sessions
- Regular feedback loops
- Continuous training programs
Remember that challenges often signal opportunities for additional improvements. By viewing obstacles as chances to refine processes further, organizations can build stronger, more resilient operations.
Taking Action On Operational Improvement
Operational improvement remains crucial for business success in today’s competitive market.
From initial assessment through implementation and monitoring, each step builds toward stronger, more efficient operations.
Organizations that commit to continuous improvement consistently outperform their competitors by 20-30% across key metrics.
The journey requires careful planning, strong leadership, and dedicated teams.
Success comes from choosing the right strategies, engaging stakeholders effectively, and maintaining momentum through challenges.
Regular measurement and adjustment ensure these improvements stick and deliver lasting value.
Now is the time to start your operational improvement initiative. Begin by assessing current processes, setting clear goals, and building a strong implementation plan.
Remember that even small improvements can lead to significant results when approached systematically and sustained over time.
SixSigma.us offers both Live Virtual classes as well as Online Self-Paced training. Most option includes access to the same great Master Black Belt instructors that teach our World Class in-person sessions. Sign-up today!
Virtual Classroom Training Programs Self-Paced Online Training Programs