Focus PDCA: Drive Continuous Improvement & Business Excellence
Constantly refining workflows is now key for businesses everywhere to stay ahead. Whether boosting product quality, streamlining operations, or better satisfying customers – having a solid process to fuel fact-based enhancements is huge. This is where the focus PDCA cycle steps up as a helpful tool.
It lets companies methodically pinpoint chances for upgrades, enact data-guided fixes, and sustainably refine how work gets done.
We’ll look into focus PDCA – find out where it came from, break down its major parts, and learn smart ways to put it into practice. Our goal is to help you extract its full potential as a transformation machine for workflow perfection.
Let’s jump in and explore how this powerful method of power builds business excellence and lights the path forward through change. Stick with me as I guide you step-by-step towards operational brilliance.
Key Highlights
- Understanding the genesis of focus PDCA and its roots in the healthcare industry, as well as its evolution from the seminal work of quality pioneers like Deming and Shewhart. Much like the Six Sigma certification framework—which builds on Deming’s principles—Focus PDCA emphasizes iterative learning and data-driven decision-making.
- Mastering the nuances of the focus steps, including identifying critical processes, assembling cross-functional teams, and mapping current states.
- Executing the PDCA cycle with precision, encompassing meticulous planning, controlled experimentation, rigorous data analysis, and sustainable implementation of improvements.
- Recognizing the multifaceted benefits of focus PDCA, such as its comprehensive end-to-end approach, simplicity and accessibility, and structured framework for consistent improvement.
- Exploring case studies and industry examples that illustrate the transformative power of focus PDCA.
- Learning essential best practices that ensure the successful adoption and long-term sustainability of focus PDCA initiatives.
Mastering the Focus PDCA Cycle: A Proven Path to Continuous Improvement
In the unrelenting quest for operational excellence and sustained competitive advantage, organizations must embrace a mindset of continuous improvement – a philosophy that permeates every facet of their processes, products, and services.
To advance structured problem-solving proficiency, pairing Focus PDCA methodology with Six Sigma certification enhances the ability to spearhead data-led improvements.
Traditional quality assurance methods, while valuable, often fall short of addressing the dynamic complexities of modern business ecosystems.
This is where the focus PDCA cycle emerges as a game-changing methodology, offering a comprehensive, data-driven framework for driving transformative change across diverse industries and organizational functions.
What is Focus PDCA?
Focus PDCA is an iterative problem-solving and process improvement methodology that harmoniously integrates two complementary cycles:
Focus (Find, Organize, Clarify, Understand, Select) and PDCA (Plan, Do, Check, Act). Originating in the healthcare industry, this approach has since gained widespread adoption across various sectors due to its versatility and effectiveness in tackling complex challenges.
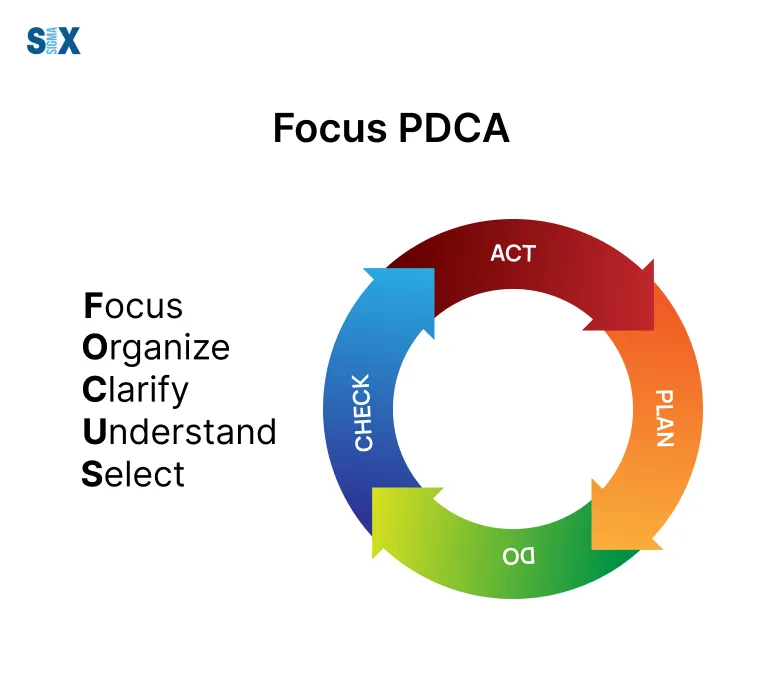
Focus PDCA builds upon the seminal work of quality pioneers like Walter Shewhart and W. Edwards Deming, who championed the PDCA cycle as a means of continually refining processes through systematic experimentation, analysis, and adaptation.
The focus component, introduced by the Hospital Corporation of America (HCA), serves as a precursor, ensuring that organizations have a solid foundation for identifying improvement opportunities, assembling cross-functional teams, and thoroughly understanding the current state of processes before embarking on the PDCA journey.
Understanding the focus Steps
The focus phase lays the groundwork for successful process improvement by guiding organizations through a series of critical steps.
Find a process to improve
Whether driven by customer complaints, performance metrics, or a proactive pursuit of optimization, this initial step involves identifying a specific process or problem area that warrants improvement.
Tools like value stream mapping, pareto analysis, and control charts can aid in pinpointing opportunities.
Organize a team
Assembling an interdisciplinary team that possesses a deep understanding of the targeted process is crucial.
Teams often benefit from including members with Six Sigma Green Belt Certifications or Six Sigma Black Belt Certification, as their training in statistical analysis and project leadership accelerates problem-solving.
This team should comprise individuals directly involved in the process, as well as customers, suppliers, and subject matter experts who can contribute diverse perspectives.
Clarify current knowledge
Before attempting to improve a process, the team must first develop a comprehensive understanding of its current state.
This involves mapping out the process flow, identifying customers and suppliers, establishing performance indicators, and setting up data collection mechanisms.
Understand the causes of variation
Every process exhibits some degree of variation, and identifying the root causes of undesirable variation is paramount.
The team employs analytical tools like cause-and-effect diagrams and the “5 Whys” technique to uncover the underlying drivers of process inconsistencies. Pairing these methods with root cause analysis training ensures teams systematically address core issues rather than symptoms.
Select an improvement strategy
Armed with a thorough understanding of the process and its pain points, the team can now brainstorm and evaluate potential solutions.
Using consensus decision-making techniques, they select the most feasible and impactful improvement strategy aligned with the organization’s broader goals.
Clarifying Current Process Knowledge with Focus PDCA
Before embarking on any improvement initiative, it is imperative to develop a comprehensive understanding of the current process state.
This critical step involves mapping out the process flow, identifying key stakeholders (customers and suppliers), establishing performance indicators, and setting up mechanisms for data collection.
Process mapping is a powerful tool that enables teams to visualize the sequence of activities, decision points, and information flows within a process.
By creating a clear, visual representation, teams can identify bottlenecks, redundancies, and areas for optimization.
Additionally, identifying customers (those who receive the outputs of the process) and suppliers (those who provide inputs) is crucial for ensuring that improvements address their needs and expectations.
Establishing relevant performance indicators is another essential aspect of clarifying current process knowledge.
These metrics serve as benchmarks against which the effectiveness of improvement efforts can be measured.
They may encompass variables such as cycle time, defect rates, customer satisfaction scores, or any other relevant Key Performance Indicators (KPIs).
Finally, setting up a robust data collection plan is paramount. This involves identifying the specific data points to be gathered, determining appropriate sampling methods, and establishing protocols for accurate and consistent data recording.
Without a solid foundation of data, the subsequent steps of the focus PDCA cycle would be compromised.
Uncovering Root Causes of Variation
Every process exhibits some degree of inherent variation, which can manifest as inconsistencies in output, inefficiencies, or deviations from desired performance levels.
Identifying and addressing the root causes of this variation is a crucial step in the focus PDCA cycle, as it allows for targeted and effective improvement efforts.
Once the team has gathered sufficient data on the current process state, they can leverage a variety of analytical tools to uncover the sources of variation.
One powerful technique is the “5 Whys” approach, which involves repeatedly asking “why” a particular problem or deviation occurs until the underlying root cause is revealed. This systematic questioning often exposes deep-seated issues that may not be immediately apparent.
Another valuable tool is the cause-and-effect diagram, also known as the fishbone or Ishikawa diagram.
This visual representation allows teams to organize potential causes of a problem into categories such as people, machines, materials, methods, and environment.
By mapping out all possible contributing factors, teams can identify patterns and prioritize the most significant root causes for further investigation.
Statistical analysis methods, such as control charts and capability studies, can also shed light on sources of variation by distinguishing between common cause variation (inherent to the process) and special cause variation (attributable to specific, identifiable events or factors).
This insight guides the team in determining whether process adjustments or fundamental redesigns are necessary.
Selecting the Optimal Improvement Strategy
Once the team has gained a comprehensive understanding of the process and its root causes of variation, the next crucial step is to select an appropriate improvement strategy.
This decision-making process often involves a combination of creative thinking techniques and objective evaluation criteria.
Brainstorming sessions can be a powerful tool for generating a diverse pool of potential solutions. By encouraging team members to share their ideas freely, without judgment or criticism, organizations can tap into the collective wisdom and unique perspectives of their workforce.
Techniques like mind mapping, SCAMPER (Substitute, Combine, Adapt, Modify, Put to another use, Eliminate, Reverse), and lateral thinking exercises can further stimulate creative problem-solving.
Cost-benefit analyses, risk assessments, and prioritization matrices can aid in objectively comparing and ranking the various options.
The selection of the optimal improvement strategy should be a collaborative effort, leveraging consensus decision-making techniques to ensure buy-in and commitment from all team members.
This collective ownership fosters a sense of shared responsibility and increases the likelihood of successful implementation.
Executing the PDCA Cycle
With a solid foundation established through the focus phase, the team can now transition into the PDCA cycle – a powerful framework for systematic experimentation, implementation, and continuous refinement of the selected improvement strategy.
The PDCA cycle, rooted in the teachings of quality pioneers like Deming and Shewhart, provides a structured approach to iterative learning and adaptation, ensuring that organizations can continuously optimize their processes and achieve sustainable gains.
Planning the Improvement Implementation
The first step in the PDCA cycle is meticulous planning, which involves translating the selected improvement strategy into a concrete action plan.
This phase necessitates a deep understanding of the current system or process, as well as a clear articulation of the desired future state.
During the planning stage, teams must gather data to establish a comprehensive baseline of the process’s current performance. This data will serve as a reference point against which the effectiveness of the improvement efforts can be measured.
Obtaining buy-in from key stakeholders is also crucial at this juncture. Effective communication and change management strategies can help mitigate resistance and foster a culture of continuous improvement.
Teams should proactively identify potential barriers to implementation and develop contingency plans to address them.
Clear roles, responsibilities, and timelines should be established, along with mechanisms for capturing feedback and course-correcting as needed.
Doing – Putting the Plan into Action
With a well-crafted plan in place, the team can proceed to the “Do” phase of the PDCA cycle, which involves implementing the improvement strategy in a controlled and systematic manner.
This stage often involves conducting small-scale pilots or experiments to test the effectiveness of the proposed changes before rolling them out more broadly.
During the implementation phase, it is crucial to adhere to the established protocols and procedures, while remaining vigilant for any unexpected events or deviations from the plan.
Thorough documentation and data collection are essential, as these observations will inform subsequent analysis and decision-making.
Teams should also maintain open lines of communication with stakeholders, providing regular updates on progress and soliciting feedback.
This collaboration can help identify potential roadblocks or unforeseen consequences early on, allowing for timely adjustments and course corrections.
It’s important to note that the “Do” phase may involve multiple iterations or cycles, as interim results and feedback may necessitate refinements or modifications to the initial plan.
This iterative approach is a hallmark of the focus PDCA methodology, enabling organizations to continuously learn and adapt based on real-world data and observations.
Studying Results and Analyzing Data
Once the improvement strategy has been implemented and sufficient data has been gathered, the team enters the “Study” phase of the PDCA cycle.
This stage involves a rigorous analysis of the collected data to evaluate the effectiveness of the implemented changes and determine whether the desired improvements have been achieved.
During this phase, teams should leverage a variety of analytical tools and techniques to make sense of the data. Statistical methods, such as hypothesis testing, regression analysis, and control charts, can help identify patterns, trends, and deviations from expected outcomes.
Qualitative data, such as customer feedback or employee observations, can also provide valuable insights into the practical implications of the changes.
One critical aspect of the “Study” phase is the comparison of the post-implementation data against the baseline established during the planning stage.
This side-by-side analysis allows teams to quantify the impact of the improvement efforts and determine the extent to which the identified performance gaps have been closed.
If the desired results have not been achieved, or if unexpected outcomes arise, the team should engage in a thorough root cause analysis to understand the underlying reasons for the discrepancies.
This may involve revisiting the initial problem statement, assumptions, or improvement strategy, and potentially returning to earlier stages of the focus PDCA cycle for further refinement.
Conversely, if the improvement efforts have been successful, the team should carefully document the learnings, best practices, and success factors.
This knowledge can inform future improvement initiatives and contribute to the organization’s continuous learning and development.
Acting to Sustain Gains
The final step of the PDCA cycle is “Act,” which focuses on sustaining and building upon the gains achieved through the improvement efforts.
This stage involves institutionalizing the successful changes, ensuring they become embedded into the organization’s standard operating procedures and culture.
One key aspect of the “Act” phase is the development and implementation of control plans or monitoring mechanisms. These measures help detect and address any deviations from the new process or system, preventing backsliding or erosion of the improvements over time.
Additionally, teams should disseminate the learnings and best practices from the improvement initiative across the organization.
Knowledge-sharing platforms, training programs, and internal communications can facilitate the transfer of insights and encourage the replication of successful approaches in other areas or processes.
Continuous improvement is an ongoing journey, and the “Act” phase provides an opportunity to identify additional areas for optimization or further refinement.
By reflecting on the lessons learned and successes achieved, teams can prioritize new improvement opportunities and embark on subsequent focus PDCA cycles, perpetuating a culture of relentless pursuit of excellence.
It’s worth noting that the PDCA cycle is inherently iterative, and organizations may find themselves revisiting earlier stages or repeating the entire cycle as new challenges or goals emerge.
This flexibility and adaptability are key strengths of the focus PDCA methodology, enabling organizations to continuously evolve and stay ahead of changing market dynamics and customer expectations.
Benefits of Using Focus PDCA
The focus PDCA methodology has gained widespread acclaim and adoption across industries due to its ability to drive measurable improvements while fostering a culture of continuous learning and adaptation.
A Comprehensive Methodology
One of the key advantages of focus PDCA is its comprehensive nature, encompassing the entire improvement journey from problem identification to sustainable implementation.
Unlike piecemeal or siloed approaches, this methodology provides a holistic framework that guides organizations through a structured series of steps, ensuring no critical aspect is overlooked.
The focus phase lays a solid foundation by facilitating a deep understanding of the current process state, root causes of variation, and stakeholder needs.
This thorough groundwork increases the likelihood of selecting and implementing appropriate improvement strategies that address the underlying issues rather than merely treating symptoms.
Simplicity and Accessibility with Focus PDCA
Despite its robustness and comprehensive nature, focus PDCA is remarkably simple and accessible, making it a valuable tool for organizations of all sizes and across diverse industries.
Unlike complex statistical methodologies or specialized techniques requiring extensive training and expertise, focus PDCA leverages intuitive tools and concepts that cross-functional teams can easily understand and apply.
While Focus PDCA excels in simplicity, combining it with Six Sigma certification methodologies (like DMAIC) can add rigor for complex, high-stakes process overhauls.
The focus phase, for instance, relies on straightforward techniques such as process mapping, brainstorming, and root cause analysis, which can be readily grasped by individuals with varying levels of experience and technical backgrounds.
This inclusivity empowers organizations to tap into the collective wisdom and perspectives of their entire workforce, fostering a sense of ownership and buy-in that is critical for successful implementation.
This simplicity and accessibility not only facilitate widespread adoption but also contribute to a culture of continuous improvement, where employees at all levels feel empowered to identify opportunities and drive positive change within their respective areas of influence.
A Structured Framework
While focus PDCA’s simplicity is a significant advantage, it is important to note that this methodology is not merely a collection of tools or techniques but rather a structured framework that guides organizations through a consistent and repeatable process.
This structured approach ensures that improvement efforts are executed with rigor and discipline, reducing the likelihood of overlooking critical steps or deviating from established best practices.
The focus PDCA framework provides a clear roadmap, outlining the specific stages and activities that teams should follow, from problem identification and team formation to data collection, analysis, and implementation.
Industry Examples and Case Studies
The transformative power of the focus PDCA methodology extends across industries and organizational functions, enabling businesses to tackle a wide range of challenges and drive measurable improvements.
From enhancing healthcare quality and patient safety to optimizing business processes and fostering a culture of continuous improvement, these examples and case studies illustrate the versatility and effectiveness of this approach.
Healthcare Quality Improvements
Given its origins in the healthcare industry, it is no surprise that focus PDCA has played a pivotal role in driving quality improvements and enhancing patient safety across various healthcare settings.
One notable example comes from a large healthcare organization that faced a concerning pattern of medication administration errors on its hospital floors.
Recognizing the severity of this issue, the organization assembled a cross-functional team to leverage the focus PDCA methodology.
Through the focus phase, the team conducted a comprehensive analysis, identifying root causes such as handwritten prescriptions, inefficient labeling practices, and a lack of automation in the medication delivery process.
Business Process Optimization with Focus PDCA
Beyond the healthcare domain, focus PDCA has proven invaluable in optimizing business processes across diverse industries.
One compelling example comes from a leading retailer that sought to enhance its customer experience during the COVID-19 pandemic when consumer behavior and preferences were rapidly shifting.
Recognizing the need to adapt swiftly, the retailer assembled a cross-functional team to leverage the focus PDCA methodology.
Through the focus phase, the team identified opportunities for improvement in the company’s order fulfillment and delivery processes, recognizing the growing demand for contactless and efficient service.
The team’s improvement strategy involved the implementation of mobile ordering capabilities, curbside pickup options, and optimized logistics for home delivery.
The PDCA cycle facilitated a phased roll-out of these changes, allowing for continuous monitoring, data-driven adjustments, and refinement based on customer feedback and operational insights.
Continuous Improvement Culture with Focus PDCA
Perhaps one of the most profound impacts of focus PDCA is its ability to cultivate a culture of continuous improvement within organizations.
This methodology fosters a sense of ownership and accountability that transcends individual improvement initiatives by empowering employees at all levels to identify opportunities, contribute insights, and drive positive change.
The results were transformative – not only did the company achieve measurable improvements in key performance indicators, but it also fostered a culture of collaboration, continuous learning, and employee empowerment.
Employees felt valued and invested in the organization’s success, driving a self-sustaining cycle of improvement and innovation.
This example underscores the profound cultural impact that focus PDCA can have, enabling organizations to tap into their workforce’s collective intelligence and cultivate a relentless pursuit of excellence that permeates every aspect of their operations.
Conclusion
In the never-ending pursuit of workflow perfection and long-term success, focus PDCA proves a powerful teammate across many industries.
By smoothly combining the strengths of both cycles, this method offers an accessible, organized framework. It fuels measurable upgrades while cultivating a learning and adapting culture.
Real cases we looked at show its strength in transforming healthcare quality, empowering staff and optimizing operations.
Whether tackling thorny problems or chasing fresh chances, the tools keep businesses nimble and resilient against an evolving landscape.
Focus PDCA’s true power lies in how it cultivates a mindset of constant betterment – one ingrained throughout an organization.
Arming all levels with the skills and process to find and act on chances breeds ownership sparking self-sustaining innovation and excellence cycles.
Focus PDCA stands as a beacon, a proven route to operational brilliance and competitive longevity.
Embrace this approach and unlock your company’s full potential to continuously evolve, adapt and thrive through change.
SixSigma.us offers both Live Virtual classes as well as Online Self-Paced training. Most option includes access to the same great Master Black Belt instructors that teach our World Class in-person sessions. Sign-up today!
Virtual Classroom Training Programs Self-Paced Online Training Programs