Design for Assembly: The Cornerstone of Modern Manufacturing Efficiency
Did you know that assembly operations typically account for 40-60% of total manufacturing costs?
For complex products like electronics or automotive components, this figure can climb even higher.
These eye-opening numbers reveal why Design for Assembly (DFA) has become crucial for companies looking to stay competitive.
Design for Assembly is a systematic approach that simplifies product designs to make assembly faster, easier, and less expensive.
Struggling with high assembly costs eating into your profits?
Learn the fundamentals of Lean thinking. Explore our Lean Introduction program.
Rather than fixing assembly problems after production begins, DFA tackles these challenges during the initial design phase—when changes cost pennies instead of thousands of dollars.
What DFA offers manufacturers:
- Reduced production costs
- Faster time to market
- Higher product quality
- Streamlined manufacturing processes
Key Highlights
- Core DFA principles simplified
- Cost-cutting assembly design techniques
- Industry-specific implementation strategies
- DFA-Six Sigma integration methods
- Step-by-step optimization framework
What Is Design For Assembly (DFA)?
Design for Assembly refers to a product design methodology that focuses on simplifying the assembly process. Engineers analyze each component and connection point to create products that require fewer parts, less time, and lower costs to assemble.
This approach shifts assembly considerations to the early design phase rather than addressing problems during production.
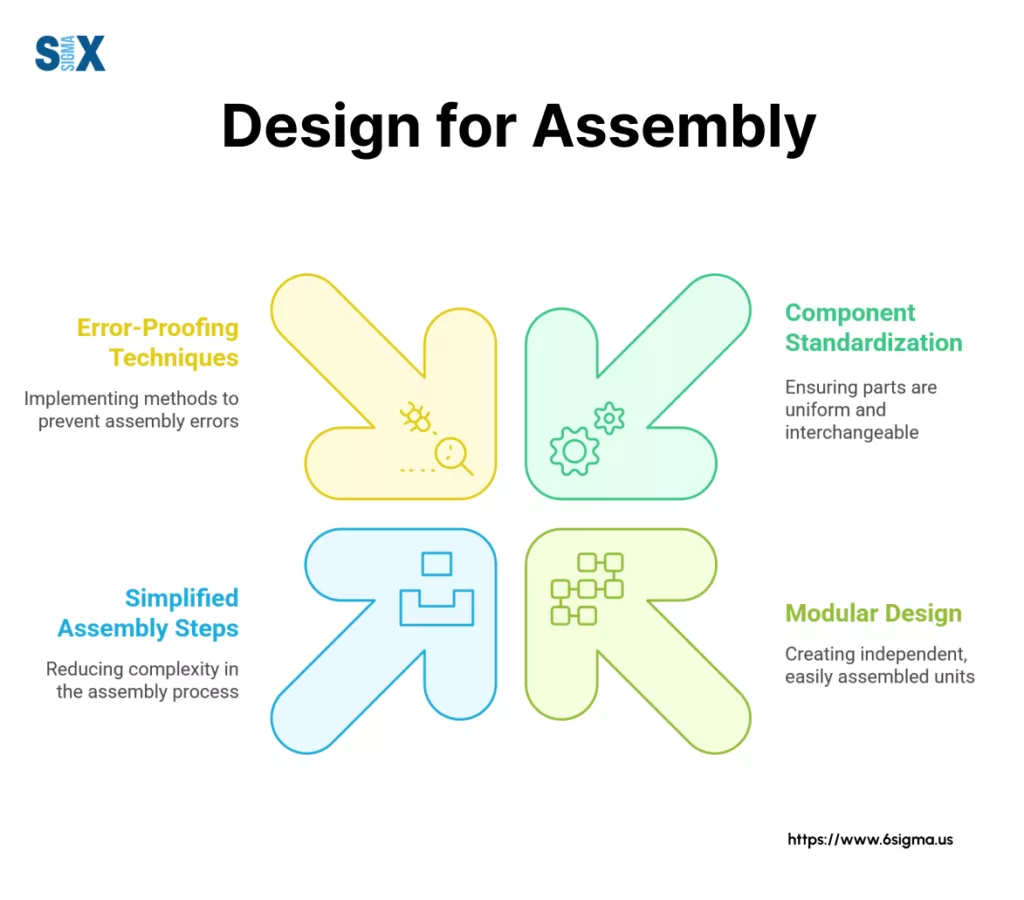
Definition And Core Concepts
What is Design for Assembly exactly? It’s both a philosophy and a practical toolkit. DFA pushes designers to question every component: “Is this part necessary?” or “Can these two parts be combined?”
The methodology includes specific guidelines for part handling, insertion, and fastening to make assembly more efficient.
The fundamental goal of DFA design is to create products that practically assemble themselves. This means designing parts that:
- Can only be inserted one way (preventing errors)
- Require minimal fasteners
- Need fewer specialized tools
- Allow for easy handling by workers or machines
Historical Development
DFA emerged in the late 1970s when Geoffrey Boothroyd and Peter Dewhurst developed the first formal methodology at the University of Massachusetts. Their groundbreaking work created quantitative metrics to evaluate assembly efficiency.
Throughout the 1980s and 1990s, companies like Ford, IBM, and Motorola adopted these principles, documenting dramatic cost reductions.
The methodology evolved from manual calculation methods to sophisticated software tools that could simulate assembly processes and predict time requirements.
Relationship With DFM And DFMA
DFA doesn’t exist in isolation. It works alongside Design for Manufacturing (DFM), which focuses on making individual parts easier to manufacture. Together, they form Design for Manufacturing and Assembly (DFMA).
Think of it this way:
- DFM ensures each part can be produced efficiently
- DFA ensures all parts can be assembled efficiently
- DFMA combines both approaches for optimal results
While DFM might focus on material selection or tolerance specifications, DFA concentrates on reducing part count and simplifying assembly operations. Both methodologies share the goal of reducing costs, but they approach the challenge from different angles.
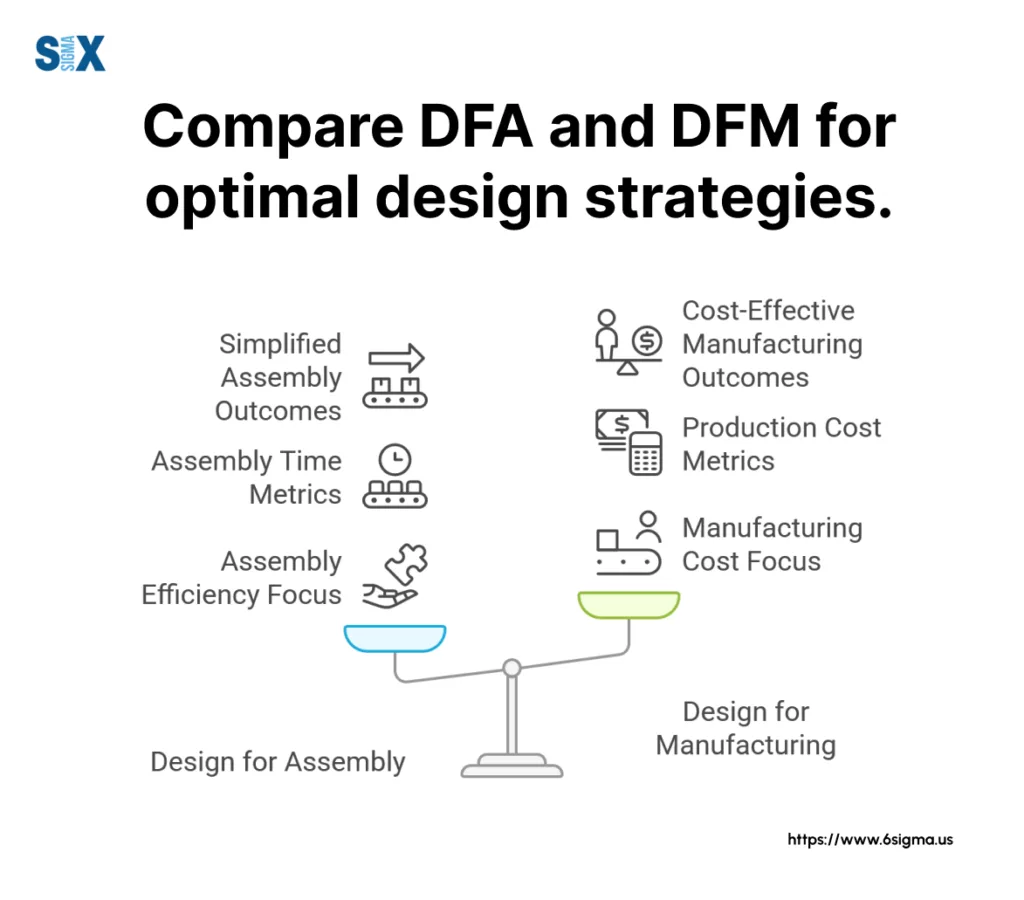
Many manufacturing challenges stem from disconnects between design and production teams.
By implementing DFA principles early, companies can avoid costly redesigns and production delays. Learn more about lean fundamentals in manufacturing to see how DFA fits into broader efficiency frameworks.
DFA With Six Sigma: A Powerful Combination
When organizations pair Design for Assembly principles with Six Sigma methodologies, they create a formidable approach to product development and manufacturing excellence.
This integration allows companies to address both design efficiency and process quality simultaneously, rather than treating them as separate initiatives.
DFA In The DMAIC Framework
The DMAIC framework (Define, Measure, Analyze, Improve, Control) provides a structured approach for implementing DFA within existing manufacturing operations:
Define: Teams identify assembly-related problems causing delays, defects, or excessive costs. These might include difficult-to-align components or error-prone assembly steps.
Measure: Engineers collect data on assembly times, error rates, and part variations to establish a baseline for improvement.
Analyze: Using DFA metrics and principles, teams evaluate which design elements contribute most to assembly difficulties.
Improve: Designers modify products based on DFA guidelines, often reducing part counts or simplifying connection methods.
Control: The improved designs are standardized and monitored to ensure sustained benefits.
This systematic approach ensures that DFA improvements are data-driven rather than based on assumptions or preferences.
Role In Design For Six Sigma (DFSS)
While DMAIC works for existing products, DFA and DFSS integration shines during new product development.
The DFSS methodology (often following DMADV: Define, Measure, Analyze, Design, Verify) incorporates assembly considerations from the earliest concept stages.
During the Design phase of DFSS, teams apply DFA principles to prevent assembly problems before they occur.
This proactive approach typically yields greater benefits than retrofitting existing designs. The Verify phase then confirms that the assembly process meets efficiency targets before full production begins.
Organizations with six sigma certification expertise often see faster adoption of DFA principles because teams already understand the importance of measurement and systematic improvement.
Ensure your designs are optimized for assembly from the start by integrating DFA within a proven DFSS framework
Quality Improvement Through DFA
Beyond efficiency gains, DFA contributes significantly to quality outcomes:
- Fewer parts mean fewer opportunities for defects
- Simplified assembly reduces operator errors
- Standardized components improve consistency
- Self-aligning features prevent misassembly
- Reduced fastener count minimizes loosening and failure points
When products are designed for efficient assembly, they typically exhibit better reliability metrics. This alignment between assembly efficiency and quality performance explains why many organizations pursue DFA as part of their broader quality strategy.
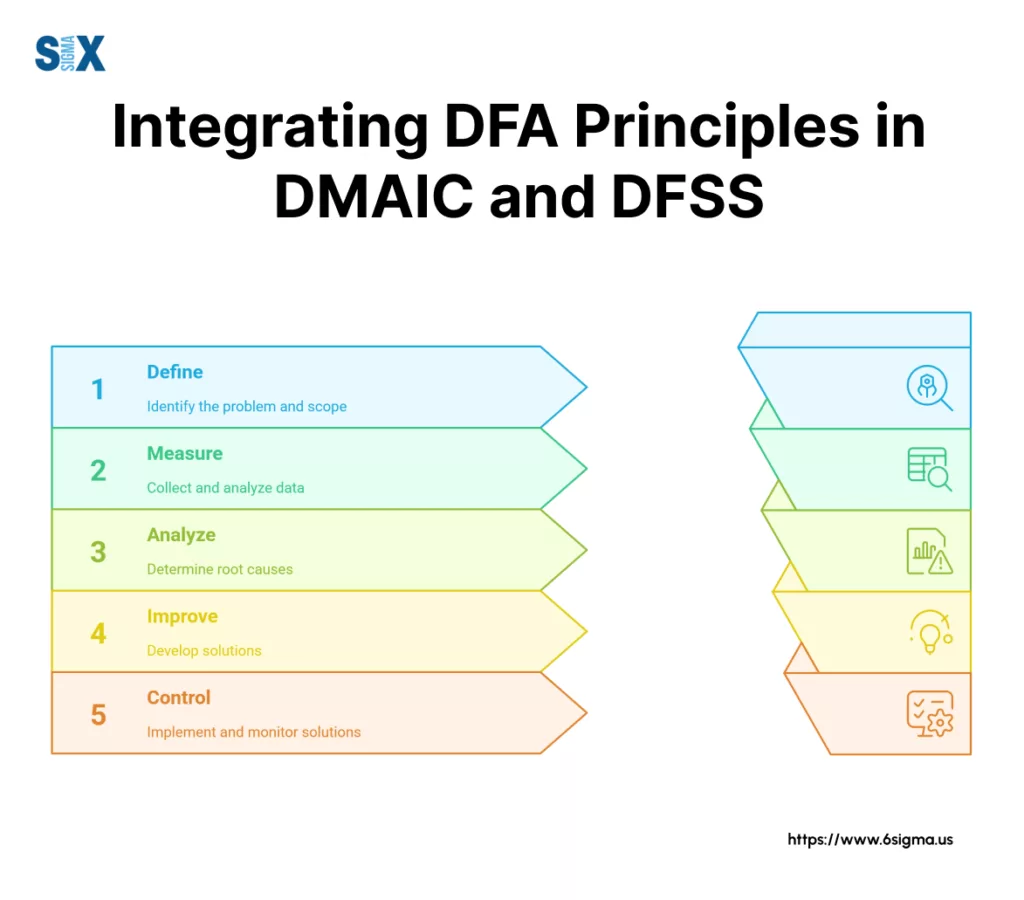
The marriage of DFA with Six Sigma methodologies creates a powerful approach that addresses both design and process excellence.
Organizations seeking to maximize the benefits of this integration often invest in developing team members with specialized knowledge in both areas.
Core Principles Of Design For Assembly
Successful implementation of Design for Assembly requires more than just good intentions—it demands adherence to specific, proven principles.
These foundational concepts guide engineers and designers toward creating products that assemble efficiently while maintaining functionality and quality.
Minimizing Part Count
The most powerful DFA principle is part count reduction. Every component eliminated from a design removes an assembly step, reduces inventory needs, and eliminates a potential failure point. Engineers should constantly question whether each part serves an essential function.
To minimize parts effectively, ask these questions for each component:
- Does this part move relative to other parts during operation?
- Must this part be made of a different material for functional reasons?
- Must this part be separate to allow assembly or disassembly?
If the answer to all three questions is “no,” the part is a candidate for elimination or combination with other components.
For example, a plastic housing with molded-in snap features eliminates separate fasteners while maintaining the same functionality.
Companies that rigorously apply this principle often discover that 30-50% of parts in typical products serve no essential function and can be eliminated through clever redesign.
Standardization
Standardization represents another cornerstone of Design for Assembly principles.
Using common components across multiple products reduces training requirements, minimizes tooling changes, and simplifies inventory management.
Effective standardization includes:
- Using identical fasteners throughout a product
- Implementing common connection methods
- Leveraging standard components across product lines
- Creating modular subassemblies that can be reused
A classic example comes from automotive manufacturing, where standardizing on a single screw type across multiple interior components dramatically reduced assembly time and error rates.
Orientation And Handling
Parts that are difficult to handle or orient create assembly bottlenecks. DFA principles address this through specific design guidelines:
- Design parts with symmetry where possible
- When symmetry isn’t possible, exaggerate asymmetry to make orientation obvious
- Include features that prevent incorrect assembly
- Avoid parts that tangle, nest, or stick together
- Design for end-effector compatibility if using automation
The ideal part is self-aligning and can only be assembled the correct way.
Consider how modern USB-C connectors improved upon older USB designs by allowing insertion in any orientation—this exemplifies good DFA thinking.
Assembly Motion Analysis
The final core principle examines the physical movements required during assembly. Efficient Design for Assembly minimizes complex motion sequences and reduces the force needed to join components.
Key motion considerations include:
- Favoring straight-line “top-down” assembly motions
- Eliminating the need to flip or reorient the assembly
- Designing for progressive assembly in a single direction
- Reducing the need for simultaneous multi-handed operations
- Minimizing fastening operations, especially those requiring tools
When designers analyze assembly motions, they often discover opportunities for root cause analysis in assembly optimization that reveals deeper design improvements.
Before/after examples of each principle ↓
Minimizing Part Count
Standardization
Orientation and Handling
Assembly Motion Analysis
These four core principles form the foundation of effective Design for Assembly. When systematically applied, they transform products from complex assemblies into streamlined designs that save time, reduce costs, and improve quality.
DFA Implementation Guidelines
Implementing Design for Assembly requires more than just understanding the principles—it demands a structured approach and proper execution.
Organizations that follow established design for assembly guidelines typically achieve better results than those attempting ad-hoc implementation.
Step-By-Step Process
A successful DFA implementation follows a logical sequence:
1. Baseline Analysis: Begin by documenting the current assembly process, including time studies, defect rates, and cost breakdowns. This establishes metrics for measuring improvement.
2. Team Formation: Create a cross-functional team including design engineers, manufacturing engineers, assembly operators, and quality specialists. Each brings crucial perspective to the analysis.
3. Product Teardown: Disassemble the product while documenting every step, noting difficult operations and time-consuming tasks. This hands-on activity often reveals opportunities invisible on engineering drawings.
4. Apply DFA Metrics: Evaluate each component using formal design for assembly guidelines such as handling time, insertion difficulty, and fastening complexity.
5. Redesign: Generate alternative designs that address identified issues, focusing first on the highest-impact components.
6. Prototype and Test: Build physical prototypes to validate assembly improvements before committing to production tooling.
7. Implementation: Roll out the improved design, ensuring proper training for assembly personnel.
8. Verification: Measure the new assembly process against baseline metrics to quantify improvements.
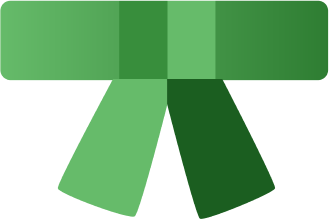
Gain the skills to map processes, analyze data with tools like Minitab.
Explore our Lean Six Sigma Green Belt Certification options.
Tools And Methodologies
Several established methodologies support Design for Assembly implementation:
Boothroyd-Dewhurst Method: This pioneering approach assigns time values to handling and insertion operations based on part characteristics. It provides a quantitative DFA index to compare design alternatives.
Lucas Method: Focuses on feeding, fitting, and fastening operations with a simplified scoring system suitable for quick analyses.
Hitachi Assembly Evaluation Method: Uses an E-score (efficiency) based on the ratio of theoretical minimum parts to actual parts, combined with assembly difficulty ratings.
Many organizations also use specialized software tools that automate calculations and provide visualization capabilities. These range from dedicated DFA software to modules within CAD systems.
Common Pitfalls To Avoid
Even well-planned DFA initiatives encounter obstacles. Watch for these frequent challenges:
Premature Optimization: Applying DFA too early in conceptual design can stifle innovation. Allow creative concepts to develop before rigorous DFA analysis.
Ignoring Manufacturing Constraints: Some DFA improvements may create manufacturing difficulties. Always consider DFM alongside DFA.
Overlooking Assembly Sequence: The order of assembly operations significantly impacts efficiency. Analyze the entire sequence, not just individual components.
Resistance to Change: Engineers may resist redesigning familiar components. Emphasize data-driven decisions and involve stakeholders early.
Neglecting Verification: Without measuring results, organizations can’t validate improvements or build support for future initiatives.
Teams seeking to enhance their DFA implementation capabilities often benefit from Six Sigma green belt certification for manufacturing professionals, which provides structured problem-solving methods that complement DFA techniques.
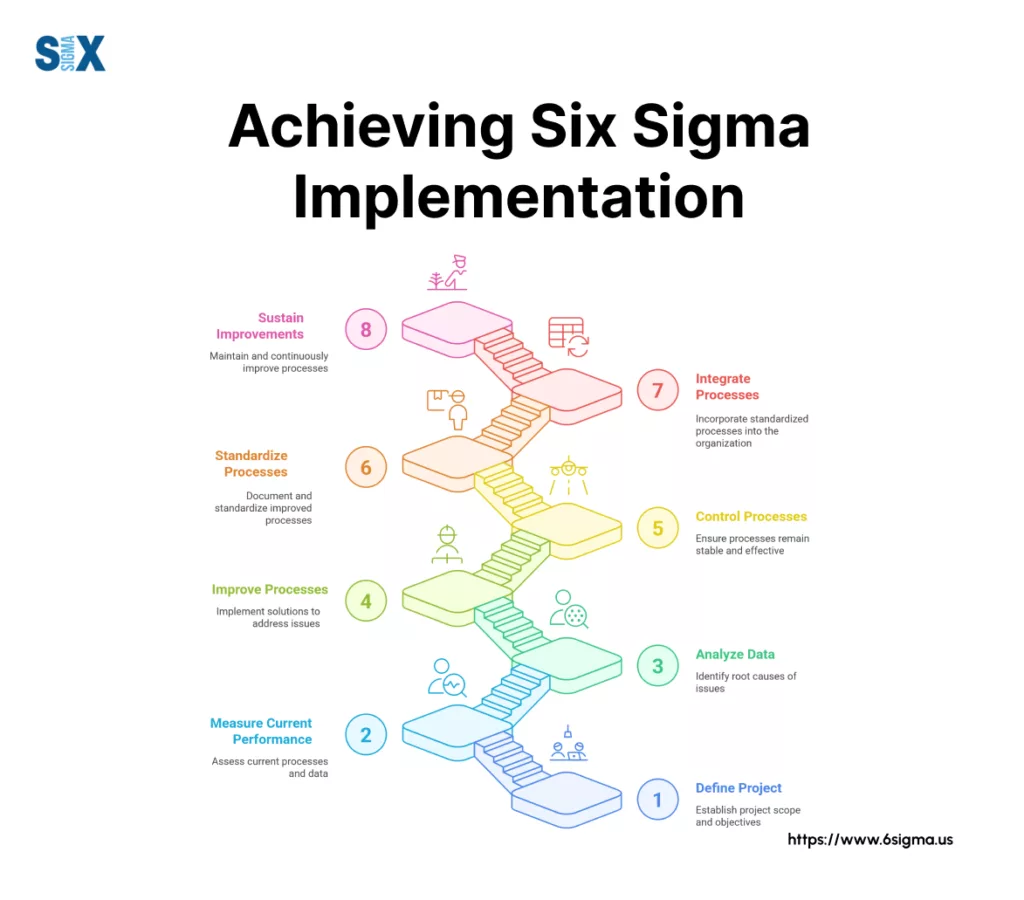
With proper planning and execution, Design for Assembly implementation can transform product development and manufacturing operations, delivering substantial cost savings and quality improvements.
Modern DFA Tools And Technologies
Today’s Design for Assembly practices leverage sophisticated digital tools that transform how engineers analyze and optimize product designs.
These technologies have dramatically expanded the capabilities of DFA engineering teams while reducing the time required for analysis.
Software Solutions
Dedicated DFA software platforms now offer powerful capabilities beyond basic calculations:
Boothroyd Dewhurst DFMA Software remains the industry standard, providing detailed analysis of handling and insertion times based on extensive research data.
The software guides users through systematic evaluation of each component and suggests specific improvements.
Siemens Teamcenter Manufacturing integrates DFA capabilities within broader PLM systems, allowing teams to evaluate assembly implications throughout the product lifecycle rather than as a separate activity.
DFMPro works as a CAD-embedded solution for NX, CATIA, and SolidWorks, providing real-time feedback on assembly issues during the design process. This immediate guidance helps engineers avoid problems before designs are finalized.
Digital Analysis Tools
Beyond dedicated DFA software, complementary technologies enhance DFA engineering capabilities:
Digital Twin Simulation allows virtual testing of assembly sequences, identifying interference issues and ergonomic challenges before physical prototypes exist. Engineers can visualize the entire assembly process and optimize the sequence digitally.
Motion Capture Systems record actual assembly operations to identify inefficiencies that might not be apparent in theoretical analyses. These systems provide quantitative data on worker movements and time requirements.
AR/VR Technologies enable assembly planners to experience proposed designs in virtual environments, testing assembly sequences and identifying potential issues without physical prototypes. This capability proves especially valuable for large or complex assemblies.
Future Trends
The evolution of Design for Assembly tools continues with several emerging technologies:
AI-Assisted Design systems can now suggest DFA improvements automatically based on pattern recognition from thousands of previous designs. These systems identify non-obvious optimization opportunities that human analysts might miss.
Generative Design tools create multiple design alternatives optimized for assembly while meeting functional requirements. By exploring design spaces beyond human imagination, these tools often produce revolutionary assembly-friendly solutions.
Cloud-Based Collaboration platforms enable distributed teams to conduct DFA analyses together, sharing insights and evaluations regardless of location. This capability has become essential as product development teams grow increasingly global.
As manufacturing becomes more automated, DFA engineering tools increasingly consider both human and robotic assembly requirements, optimizing designs for either scenario or creating flexible designs suitable for mixed assembly environments.
These evolving tools ensure that Design for Assembly remains relevant even as manufacturing technologies change, providing engineers with increasingly powerful capabilities to optimize products for efficient production.
Measuring DFA Success
Quantifying the impact of Design for Assembly initiatives provides crucial feedback for continuous improvement and helps justify investment in DFA methodologies.
Organizations that measure results systematically achieve better long-term outcomes than those relying on subjective assessments.
DFA Index Explanation
The DFA index serves as the primary metric for evaluating design efficiency. This numerical score compares the theoretical minimum assembly time to the actual estimated assembly time:
DFA Index = Theoretical Minimum Assembly Time / Estimated Assembly Time
The theoretical minimum assumes ideal conditions: perfect parts, optimal assembly sequence, and minimal fasteners. A higher index (closer to 1.0) indicates a more assembly-efficient design.
Different methodologies calculate this index slightly differently:
Boothroyd-Dewhurst assigns standard time values to handling and insertion operations based on part characteristics, then compares the total to a theoretical minimum.
Lucas Method combines feeding ratio, fitting ratio, and fastening ratio scores to generate an overall efficiency rating.
Hitachi’s AEM uses an E-score based on the ratio of theoretical minimum parts to actual parts, multiplied by a penalty factor for assembly difficulty.
Performance Metrics
Beyond the DFA index, organizations track several operational metrics to evaluate implementation success:
- Assembly Time Reduction: The percentage decrease in total assembly time compared to previous designs.
- Part Count Reduction: The percentage decrease in total component count.
- First-Pass Yield: The percentage of products that pass quality checks without rework after assembly.
- Assembly Error Rate: The frequency of assembly-related defects per unit.
- Tooling Reduction: The percentage decrease in specialized fixtures or tools required.
These metrics provide a balanced view of Design for Assembly impact across efficiency, quality, and cost dimensions.
Aiming to maximize the ROI of your DFA initiatives through advanced optimization?
Lead complex improvement projects and mentor others. Advance your skills with our Lean Six Sigma Black Belt certification.
ROI Calculation
Calculating return on investment for DFA initiatives requires comparing implementation costs against realized benefits:
Implementation costs typically include:
- Training expenses
- Software licensing
- Engineering time for analysis and redesign
- Prototype development
- Tooling modifications
Benefits generally include:
- Reduced direct labor costs
- Lower material costs from fewer parts
- Decreased inventory carrying costs
- Reduced warranty claims from improved quality
- Faster time-to-market from simplified designs
A typical ROI formula for Design for Assembly initiatives:
ROI = (Total Annual Savings × Product Lifecycle) / Implementation Costs
Many companies report ROI ratios of 10:1 or higher for well-executed DFA projects, with payback periods often under six months.
Assembly Cost Estimator
The Road Ahead
Design for Assembly represents one of the most powerful methodologies available to manufacturing organizations seeking to improve efficiency and reduce costs.
By focusing on simplification, standardization, and assembly-friendly features, DFA delivers benefits that extend far beyond the assembly line.
The principles and methodologies outlined in this guide provide a foundation for implementing DFA in any manufacturing environment.
From basic guidelines to sophisticated analysis tools, these approaches help engineering teams create products that are inherently easier to assemble.
As manufacturing continues to evolve with increased automation and digital integration, Design for Assembly principles remain relevant—though the specific implementation techniques will adapt to new technologies and production methods.
Organizations that master these fundamentals position themselves for sustained competitive advantage in increasingly challenging markets.
SixSigma.us offers both Live Virtual classes as well as Online Self-Paced training. Most option includes access to the same great Master Black Belt instructors that teach our World Class in-person sessions. Sign-up today!
Virtual Classroom Training Programs Self-Paced Online Training Programs