Cellular Manufacturing in Lean Six Sigma: A Complete Implementation Guide
Manufacturing has evolved significantly since the days of traditional assembly lines. Today’s production floors demand smarter, more efficient systems that reduce waste while maintaining quality.
This is where cellular manufacturing steps in as a game-changing approach within the Lean Six Sigma methodology.
Cellular manufacturing transforms how products move through production by organizing workstations and equipment into cells, each dedicated to specific product families.
Key Highlights
- Quality control through cell optimization
- Waste reduction strategies
- Workflow efficiency improvements
- Employee cross-training methods
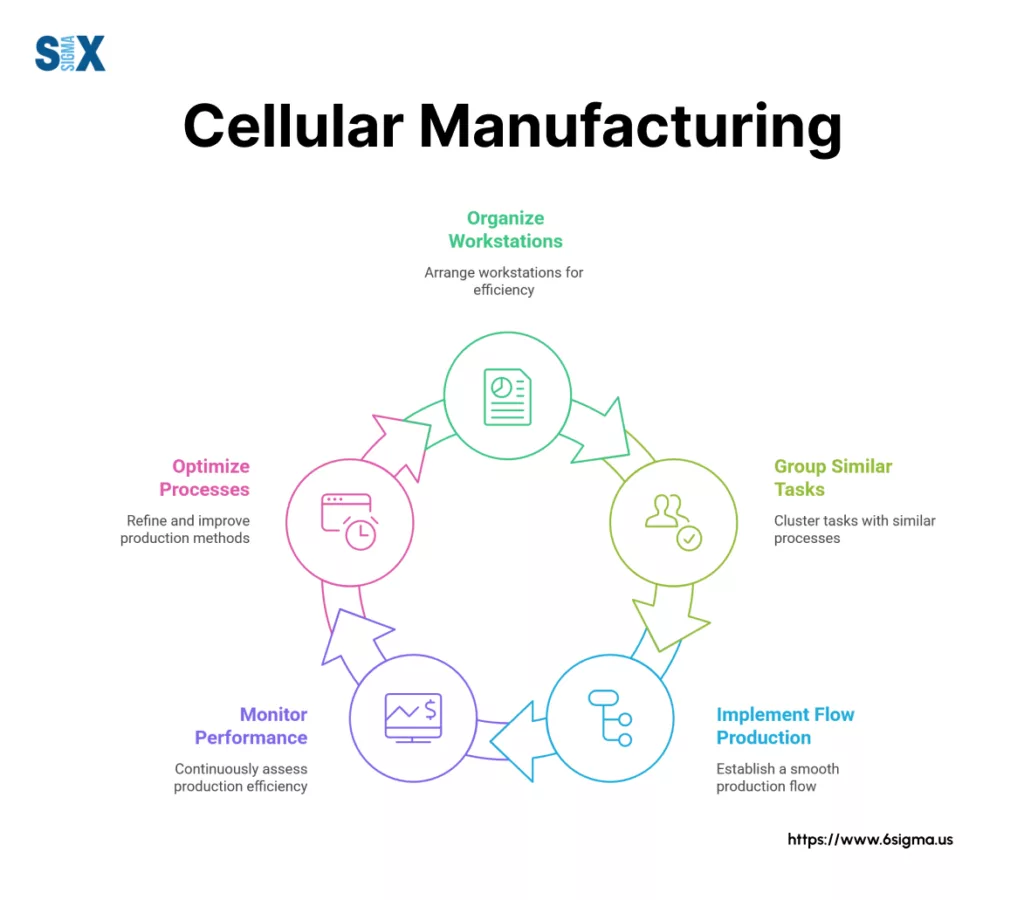
What Is Cellular Manufacturing Systems?
Cellular manufacturing systems organize production equipment and workstations into groups called cells, where each cell handles specific product families.
This arrangement enables efficient production flow while minimizing waste and maximizing quality control through the Six Sigma methodology.
Core Elements of Cellular Manufacturing
The foundation of cellular manufacturing rests on grouping similar products into families based on their production requirements.
Each cell contains the necessary machines, tools, and skilled operators to produce these product families from start to finish.
This setup drastically reduces transport time between operations and enables quick identification of quality issues.
Manufacturing cells typically feature:
- Grouped equipment for complete product processing
- Cross-trained operators managing multiple machines
- Minimal distance between workstations
- Built-in quality control checkpoints
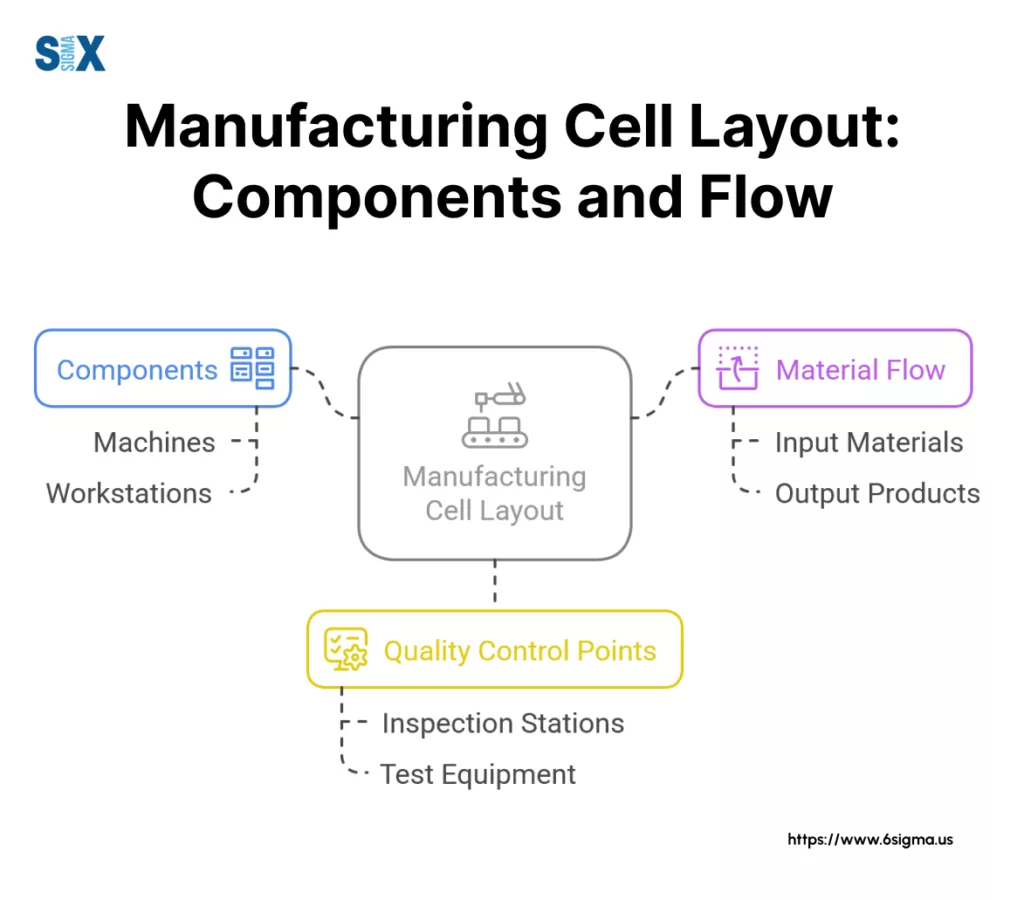
Aligning With Lean Six Sigma
Cellular manufacturing systems directly support Six Sigma goals by creating controlled environments where defects become immediately visible.
When operators work within cells, they can quickly spot and address quality issues before they cascade through the production process.
The cellular manufacturing process aligns perfectly with the DMAIC framework:
- Define: Cells help clearly define process boundaries and product family specifications.
- Measure: Contained work areas make data collection and performance measurement easier.
- Analyze: Localized operations enable quick root cause analysis of quality issues.
- Improve: Cell layouts facilitate rapid implementation of process improvements.
- Control: Standardized cell operations maintain quality improvements over time.
Quality Control Through Cell Design
Each manufacturing cell serves as a mini quality control center. Operators become experts in their product families, leading to better defect detection and prevention.
This expertise, combined with the close proximity of operations, creates multiple opportunities for quality checks throughout the production process.
Impact of Cellular Manufacturing on Production Efficiency
Manufacturing cells significantly reduce:
- Material handling time
- Work-in-progress inventory
- Production lead times
- Quality defects
- Space requirements
These reductions directly contribute to improved quality metrics and reduced variation in output, key goals in any Six Sigma initiative.
Training and Skill Development
Success in cellular manufacturing systems depends heavily on operator training. Workers must develop multiple skills to manage various machines within their cells.
This cross-training creates a more flexible workforce and helps maintain consistent quality standards across all operations.
Measuring Cell Performance with Cellular Manufacturing
Key metrics for cellular manufacturing systems include:
- Cycle time per product family
- First-pass yield rates
- Cell productivity
- Quality metrics
- Operator efficiency
These measurements help track both production efficiency and quality improvements, ensuring the cellular manufacturing process maintains Six Sigma standards.
Master Cellular Manufacturing Techniques
Change your manufacturing approach with proven Six Sigma strategies with Six Sigma Green Belt Certification Course
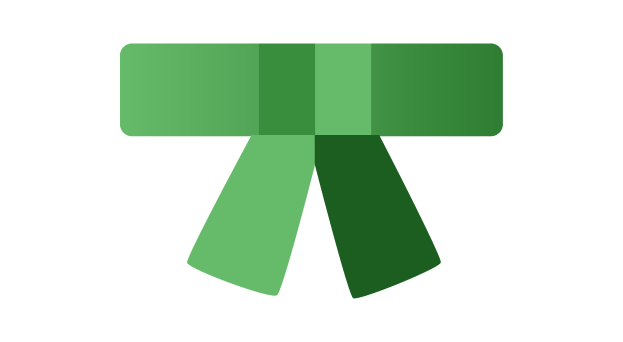
Traditional vs. Cellular Manufacturing: A Six Sigma Perspective
The shift from traditional to lean cellular manufacturing marks a significant evolution in production methodology.
This transformation affects everything from floor layouts to quality control processes, creating new opportunities for waste reduction and process improvement.
Layout and Workflow Differences
Traditional manufacturing typically follows a departmental layout where similar machines are grouped together.
Products move between departments, often traveling long distances and creating significant work-in-progress inventory.
This setup makes quality control challenging and increases the risk of defects going unnoticed.
In contrast, cellular flow manufacturing arranges equipment based on product families.
Each cell contains all necessary machines to complete a product or component, minimizing travel distance and allowing for immediate quality checks.
This arrangement naturally supports Six Sigma goals by reducing variation and enabling faster problem detection.
Quality Metrics and Performance of Cellular Manufacturing
Traditional manufacturing often struggles with:
- Long lead times between quality checks
- Delayed defect detection
- High work-in-progress inventory
- Difficult root cause analysis
- Limited operator ownership
Lean cellular manufacturing addresses these challenges through:
- Immediate quality feedback
- Reduced defect propagation
- Minimal inventory buildup
- Clear problem ownership
- Enhanced process control
Waste Reduction Through Cell Design
The cellular approach specifically targets the eight forms of waste identified in Six Sigma:
- Transportation: Cells minimize product movement between operations.
- Inventory: Smaller batch sizes reduce work-in-progress.
- Motion: Operators work within compact cells, reducing unnecessary movement.
- Waiting: Continuous flow reduces delays between operations.
- Over-processing: Clear standardization prevents redundant work.
- Overproduction: Pull systems match production to demand.
- Defects: Quick detection prevents defect multiplication.
- Skills: Cross-training maximizes operator capabilities.
Impact of Cellular Manufacturing on Process Control
Traditional manufacturing often relies on end-of-line quality checks, making it difficult to identify where defects originate.
The cellular flow manufacturing model enables continuous quality monitoring throughout the production process. Operators can spot issues immediately and implement corrections before defects multiply.
Data Collection and Analysis of Cellular Manufacturing
Quality data collection becomes more straightforward in cellular manufacturing.
Each cell serves as a natural data collection point, allowing for:
- Real-time process monitoring
- Quick performance feedback
- Accurate root cause analysis
- Effective improvement tracking
Employee Engagement and Quality
The cellular approach transforms how operators interact with quality control. Instead of specialized quality inspectors, operators become responsible for quality within their cells.
This ownership leads to:
- Better defect prevention
- Faster problem-solving
- Improved process understanding
- Enhanced quality consciousness
The transition from traditional to lean cellular manufacturing requires careful planning and implementation.
However, the benefits in terms of quality improvement, waste reduction, and process control make this transformation valuable for organizations committed to Six Sigma excellence.
Build Your Foundation in Process Improvement with Six Sigma Yellow Belt Course
Types of Cellular Manufacturing Layouts
Manufacturing cells come in various configurations, each designed to optimize specific production requirements and quality control needs.
The right cellular manufacturing design can significantly impact process efficiency and defect reduction capabilities.
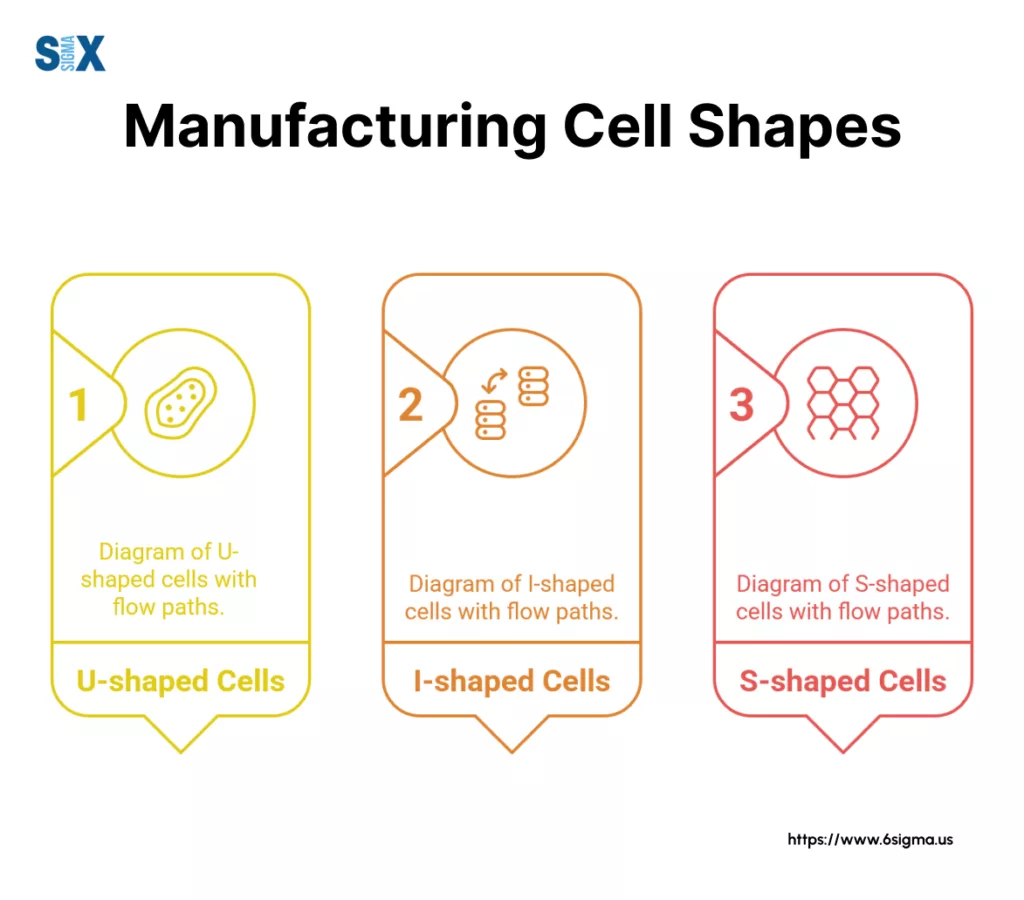
U-Shaped Cell Configuration
U-shaped manufacturing cells rank among the most popular layouts due to their efficiency and operator accessibility.
This design places machines and workstations in a U pattern, allowing operators to move easily between the beginning and end of the production sequence.
Key advantages of U-shaped cells include:
- Minimal operator movement
- Enhanced visual control
- Flexible staffing options
- Improved communication
- Easy access to multiple processes
I-Shaped Cell Layout
I-shaped cells, also known as linear cells, arrange equipment in a straight line.
This cellular manufacturing design works well for products requiring sequential operations with minimal backflow.
The layout particularly suits:
- Simple product sequences
- Limited space configurations
- Single-operator cells
- High-volume production
- Automated material handling
S-Shaped Cell Configuration
S-shaped manufacturing cells offer solutions for complex processes requiring multiple operations while maximizing available floor space.
These cells excel in:
- Complex product routing
- Space-constrained environments
- Multi-product families
- Variable process sequences
- Team-based operations
Selecting The Right Cell Design for Cellular Manufacturing
Six Sigma tools help determine the optimal cell layout through systematic analysis of:
Process Requirements:
- Product family characteristics
- Operation sequences
- Material handling needs
- Quality control points
- Operator movement patterns
Space Considerations:
- Available floor space
- Access requirements
- Material flow paths
- Utility connections
- Safety clearances
Quality Integration In Cell Design
Each layout type presents unique opportunities for quality control integration.
The cellular manufacturing design must incorporate:
- Strategic quality check points
- Error-proofing stations
- Visual management systems
- Data collection locations
- Quick response areas
Optimizing Cell Performance for Cellular Manufacturing
Manufacturing cells require regular evaluation and adjustment to maintain peak performance.
Key optimization factors include:
Flow Analysis:
- Material movement patterns
- Operator motion studies
- Cycle time variations
- Quality metrics tracking
- Bottleneck identification
Equipment Placement:
- Machine accessibility
- Maintenance requirements
- Tool storage location
- Safety considerations
- Visual management needs
Future-Proofing Cell Layouts
Modern manufacturing cells must accommodate potential changes in:
- Product mix variations
- Volume fluctuations
- Technology upgrades
- Quality requirements
- Automation integration
The success of any cellular manufacturing design depends on careful consideration of current needs while maintaining flexibility for future modifications.
Regular evaluation using Six Sigma tools ensures continued effectiveness and quality improvement opportunities.
Implementing Cellular Manufacturing with DMAIC
Successfully implementing cellular manufacturing requires a structured approach.
The DMAIC methodology provides a proven framework for transitioning from traditional to cell production manufacturing while maintaining quality standards and minimizing disruption.
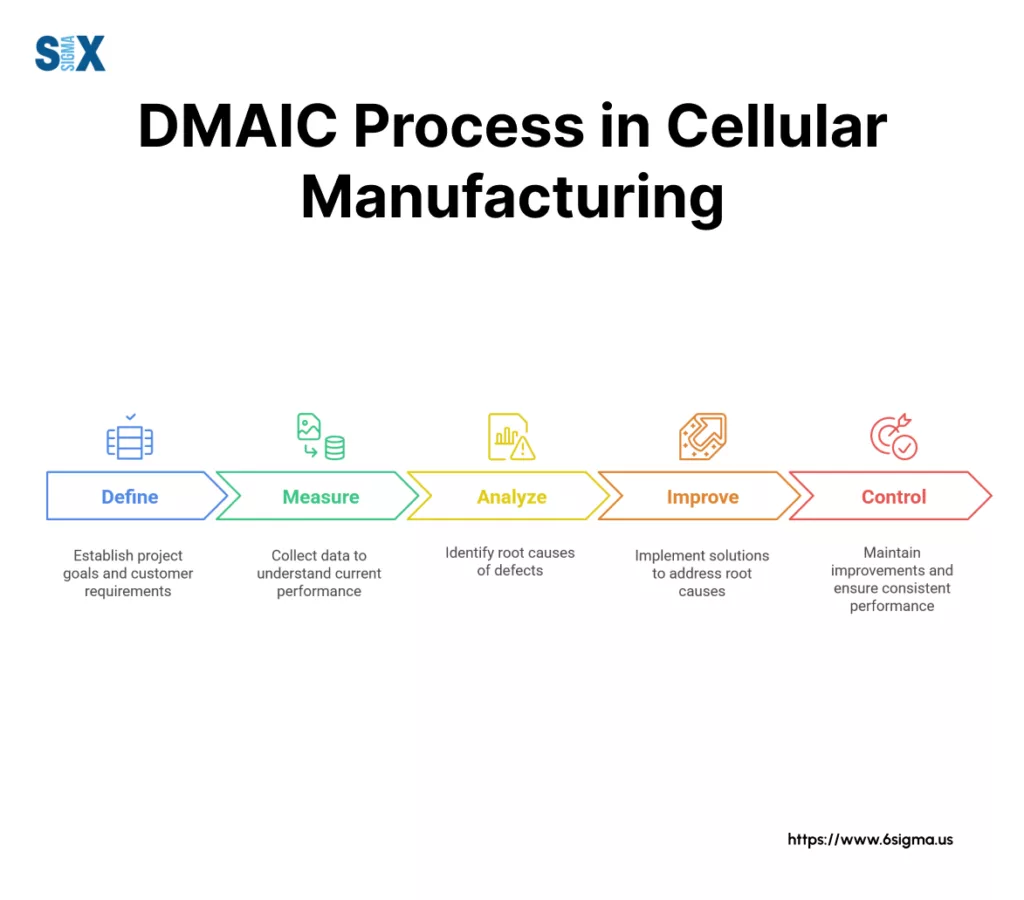
Define Phase: Setting The Foundation
The Define phase establishes clear objectives and scope for implementing cellular manufacturing.
This phase focuses on identifying specific products or product families suitable for cellular production.
Key Activities:
- Project charter development
- Product family analysis
- Current state documentation
- Resource requirement planning
- Stakeholder communication strategy
Success in this phase depends on gathering input from operators, supervisors, and management to ensure alignment with organizational goals.
Measure Phase: Establishing Baselines
During the Measure phase, teams collect data about current operations to establish performance benchmarks. This information guides decision-making throughout the implementation process.
Critical Measurements Include:
- Current cycle times
- Quality metrics
- Production volumes
- Process variations
- Resource utilization rates
These measurements provide the foundation for comparing future cell performance against existing operations.
Analyze Phase: Understanding Process Dynamics
The Analysis phase examines collected data to identify improvement opportunities and potential challenges in implementing cellular manufacturing.
Teams use various tools to understand process relationships and dependencies.
Key Analysis Tools:
- Value stream mapping
- Process flow analysis
- Cause-and-effect diagrams
- Capacity studies
- Workflow simulations
This analysis helps teams design optimal cell layouts and workflow patterns.
Improve Phase: Creating Effective Cells
The Improve phase focuses on designing and implementing manufacturing cells based on analyzed data.
This phase requires careful planning and coordination to minimize production disruptions.
Implementation Steps:
- Cell layout design
- Equipment placement
- Operator training programs
- Standard work development
- Trial runs and adjustments
Each step builds upon previous phases to create efficient, quality-focused production cells.
Control Phase: Maintaining Excellence
The Control phase ensures sustained success of the implemented cellular manufacturing system through monitoring and continuous improvement processes.
Control Elements:
- Performance monitoring systems
- Standard operating procedures
- Regular audits
- Training programs
- Improvement mechanisms
Quality Integration Throughout Implementation
Quality considerations must remain central throughout the implementation process.
Each phase incorporates specific quality control elements:
- Define: Identifying critical quality characteristics
- Measure: Establishing quality metrics
- Analyze: Understanding quality impact points
- Improve: Building quality checks into cell design
- Control: Monitoring quality performance
Technology Integration In Cell Implementation
Modern cell production manufacturing often incorporates digital tools and technologies:
- Digital work instructions
- Real-time monitoring systems
- Quality data collection
- Performance analytics
- Predictive maintenance
Change Management Considerations of Cellular Manufacturing
Successful implementation requires careful attention to the human elements of change:
- Operator engagement
- Skills development
- Communication plans
- Feedback mechanisms
- Recognition programs
Measuring Implementation Success of Cellular Manufacturing
Key performance indicators help track implementation progress:
- Productivity improvements
- Quality metrics
- Lead time reduction
- Space utilization
- Employee satisfaction
Regular monitoring of these metrics ensures that the implementation meets its objectives while identifying areas for continued improvement.
Benefits and Limitations Through Six Sigma Lens
Cellular manufacturing lean principles offer significant advantages when properly implemented, yet also present certain challenges that organizations must address.
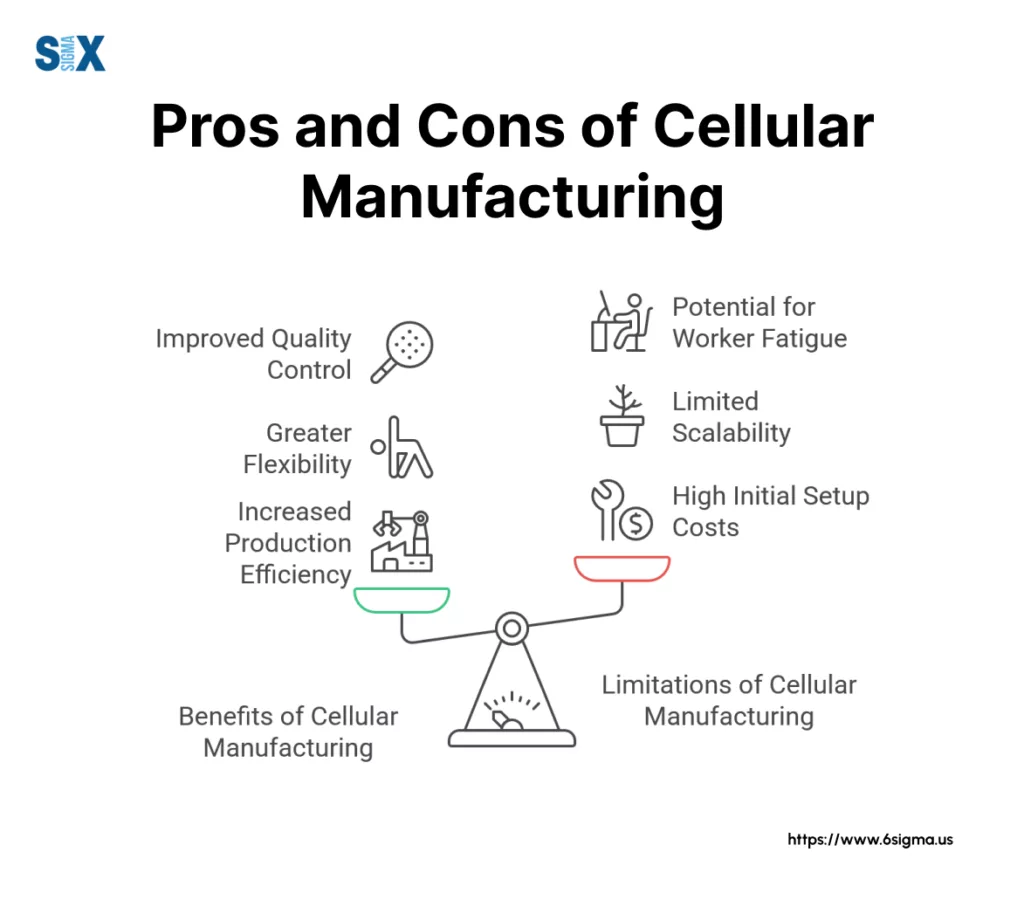
Quality Improvement Benefits
The integration of cellular manufacturing with Six Sigma methodologies drives substantial quality improvements.
Operators working in cells develop deeper product knowledge, leading to better defect detection and prevention. Quality metrics typically show:
Defect Reduction:
- 50-70% decrease in quality issues
- Faster defect detection
- Improved first-pass yield
- Reduced rework requirements
- Enhanced process control
Efficiency and Productivity Gains with Cellular Manufacturing
Lean cellular manufacturing creates significant operational improvements through streamlined workflows and reduced waste.
Organizations often report:
Production Improvements:
- 30-50% reduction in cycle time
- Decreased work-in-progress
- Shorter lead times
- Improved operator efficiency
- Enhanced resource utilization
Cost Reduction Opportunities
Financial benefits emerge through various operational improvements:
Direct Cost Savings:
- Lower inventory costs
- Reduced material handling
- Decreased space requirements
- Minimized transportation waste
- Lower quality-related costs
Implementation Challenges
Organizations must address several key challenges when transitioning to cellular manufacturing:
Technical Challenges:
- Equipment relocation costs
- Cell layout optimization
- Process standardization
- Technology integration
- Maintenance coordination
Operational Considerations of Cellular Manufacturing
Daily operations present specific challenges:
Production Flexibility:
- Volume fluctuation management
- Product mix variations
- Equipment breakdown impact
- Cross-training requirements
- Resource allocation
Change Management Issues
Human factors often present significant challenges:
Cultural Adaptation:
- Resistance to change
- Skill development needs
- Team dynamics
- Communication barriers
- Leadership support
Risk Mitigation Strategies of Cellular Manufacturing
Successful implementation requires proactive risk management:
Risk Management:
- Pilot program implementation
- Phased rollout approach
- Regular performance monitoring
- Contingency planning
- Continuous feedback loops
Long-Term Success Factors
Sustaining benefits requires ongoing attention to:
Maintenance Requirements:
- Regular cell optimization
- Continuous improvement programs
- Training updates
- Technology upgrades
- Performance monitoring
Measuring Success
Organizations should track specific metrics to evaluate cellular manufacturing effectiveness:
Key Performance Indicators:
- Quality metrics
- Productivity measures
- Cost reduction data
- Employee satisfaction
- Customer feedback
Future Optimization Opportunities with Cellular Manufacturing
Continuous improvement remains essential for long-term success:
Development Areas:
- Advanced automation integration
- Digital technology adoption
- Process refinement
- Skill enhancement
- Innovation opportunities
The success of it depends on balancing these benefits and limitations while maintaining focus on continuous improvement through Six Sigma methodologies.
Regular evaluation and adjustment ensure sustained performance improvements and competitive advantage.
Become a leader in operational excellence with Black Belt
Bring transformative improvements across your organization
Future Developments in Cellular Manufacturing
The manufacturing industry continues to evolve rapidly, bringing new technologies and methodologies that enhance cellular manufacturing systems.
These developments promise to revolutionize how manufacturing cells operate and deliver value.
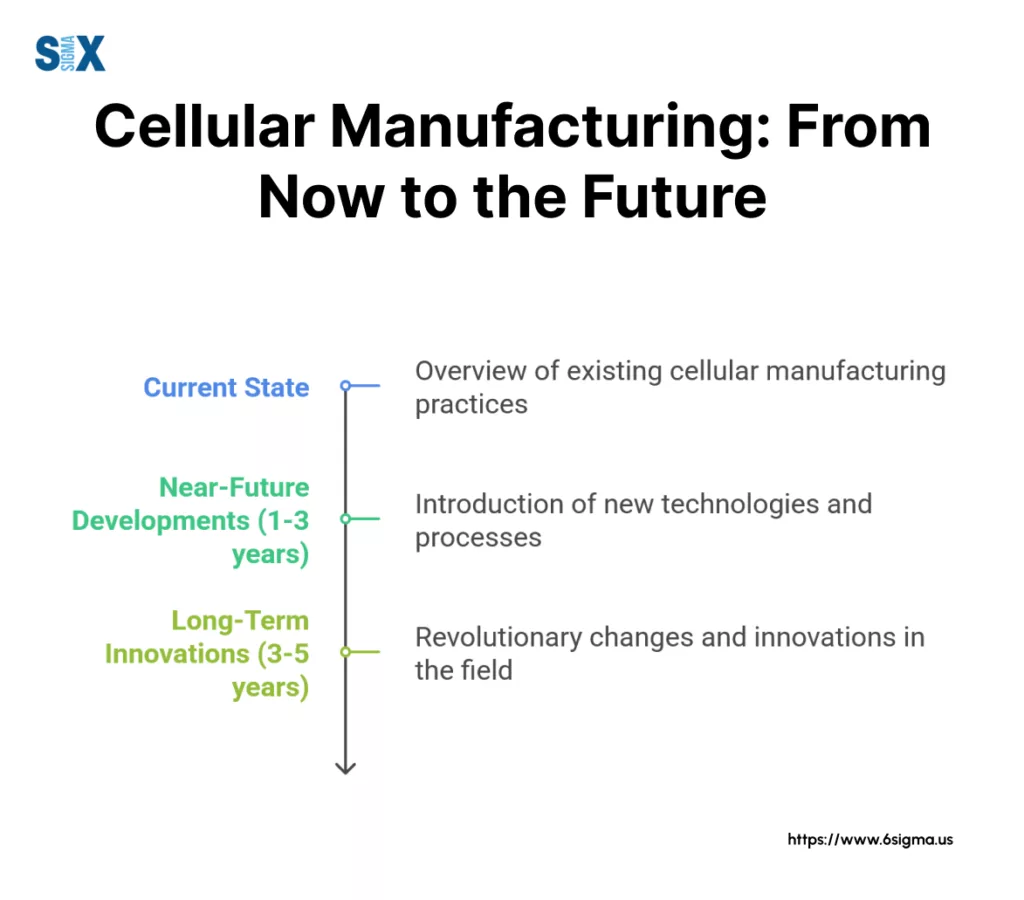
Digital Transformation in Manufacturing Cells
Smart technology integration transforms traditional manufacturing cells into connected production units.
Modern cells increasingly incorporate:
Digital Elements:
- Real-time monitoring systems
- Predictive maintenance alerts
- Digital work instructions
- Quality verification tools
- Performance analytics dashboards
These digital tools enable better decision-making and faster response to production issues.
Artificial Intelligence and Machine Learning Applications
AI and machine learning bring new capabilities to cellular manufacturing through:
Smart Operations:
- Automated cell balancing
- Quality prediction models
- Optimal scheduling systems
- Resource allocation optimization
- Preventive maintenance scheduling
Industrial Internet of Things (IIoT) Integration with Cellular Manufacturing
IIoT technology creates connected manufacturing environments where cells communicate and share data seamlessly.
This connectivity enables:
Enhanced Operations:
- Real-time performance tracking
- Automated material handling
- Environmental monitoring
- Energy usage optimization
- Remote cell management
Advanced Robotics and Automation
Next-generation robotics enhance cellular manufacturing through:
Robotic Applications:
- Collaborative robots in cells
- Automated quality inspection
- Flexible material handling
- Complex assembly operations
- Safety monitoring systems
Sustainable Manufacturing Practices with Cellular Manufacturing
Environmental considerations drive new developments in cellular manufacturing:
Green Initiatives:
- Energy-efficient cell designs
- Waste reduction systems
- Sustainable material handling
- Environmental monitoring
- Resource optimization tools
Integration With Extended Manufacturing Systems
Manufacturing cells increasingly connect with broader supply chain systems through:
Extended Integration:
- Supply chain synchronization
- Customer demand alignment
- Vendor managed inventory
- Quality data sharing
- Production scheduling coordination
Enhanced Training and Skill Development with Cellular Manufacturing
Future workforce development focuses on:
Advanced Training:
- Virtual reality training modules
- Augmented reality work instructions
- Remote expert assistance
- Digital skill development
- Continuous learning platforms
Quality Management Evolution
Quality control systems advance through:
Modern Quality Tools:
- AI-powered inspection systems
- Real-time quality monitoring
- Predictive quality analytics
- Automated correction systems
- Digital quality documentation
Flexible Manufacturing Capabilities
Future cells will offer increased flexibility through:
Adaptable Systems:
- Quick changeover capabilities
- Multi-product processing
- Modular cell designs
- Scalable production capacity
- Rapid reconfiguration options
These developments in cellular manufacturing point toward more efficient, flexible, and sustainable production systems.
Manufacturing professionals must stay informed about these trends to maintain competitive advantage and drive continuous improvement in their operations.
SixSigma.us offers both Live Virtual classes as well as Online Self-Paced training. Most option includes access to the same great Master Black Belt instructors that teach our World Class in-person sessions. Sign-up today!
Virtual Classroom Training Programs Self-Paced Online Training Programs