The Guide to Creating an Effective Quality Control Plan in Six Sigma [2025]
A quality control plan serves as the foundation for maintaining product and service standards across organizations.
This systematic approach defines processes, responsibilities, and metrics to ensure consistent quality outputs.
Modern businesses implement these plans to meet customer expectations, reduce operational costs, and maintain their competitive edge in the market.
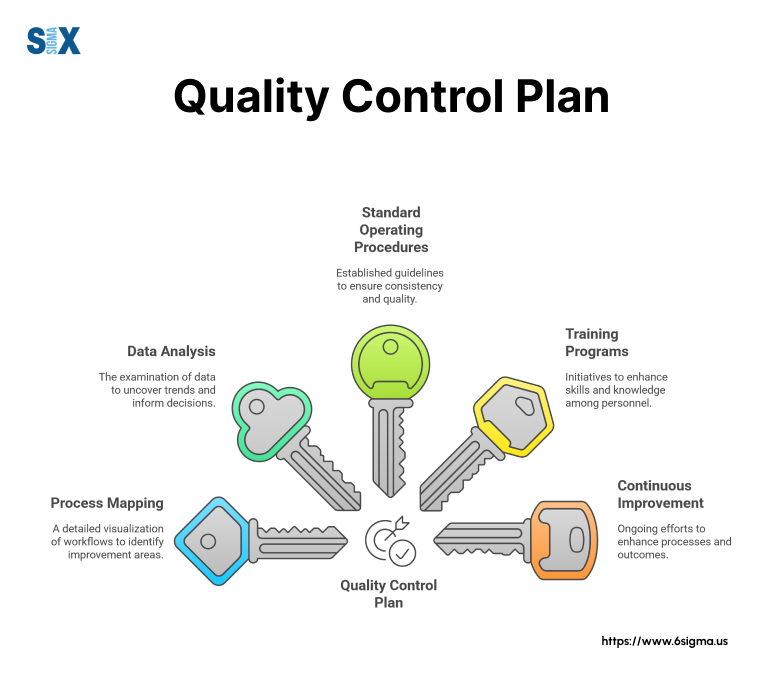
Key Highlights About Quality Control Plans
- Steps to develop robust quality control measures
- Essential elements of successful quality plans
- Digital tools for quality management
- Implementation strategies and best practices
What is a Quality Control Plan?
A quality control plan functions as a documented framework that outlines specific procedures, standards, and responsibilities for maintaining product or service quality.
This strategic document guides organizations in meeting customer requirements while optimizing operational efficiency.
Manufacturing firms, service providers, and project teams rely on these plans to establish consistent quality standards across their operations.
Defining Elements Of Quality Control Plans
Quality control plans establish clear guidelines for product specifications, testing protocols, and acceptance criteria.
These plans detail inspection methods, sampling procedures, and corrective actions when deviations occur.
Organizations use these elements to prevent defects, reduce waste, and ensure customer satisfaction through standardized quality measures.
Essential Components For Effective Quality Management
Several key components form the foundation of a successful quality control plan. The first component involves detailed product or service specifications that set measurable standards.
Next, the plan must outline specific testing and inspection procedures for various production stages. Documentation requirements ensure proper record-keeping of quality-related activities.
Finally, the plan should specify roles and responsibilities for quality management tasks.
Quality Control Vs. Quality Assurance Vs. Quality Management
While often used interchangeably, these terms represent distinct aspects of quality operations. Quality control focuses on product testing and inspection to identify defects.
Quality assurance emphasizes preventing quality issues through process improvements and standardization.
Quality management systems encompass both quality control and assurance, creating an overarching framework for quality operations.
The Role Of Quality Management Systems
A quality management system coordinates various quality initiatives across an organization.
This system integrates quality control plans with broader business objectives, ensuring alignment between quality goals and organizational strategy.
Modern quality management systems often incorporate digital tools for monitoring, reporting, and analyzing quality metrics.
Implementation Across Different Industries
Quality control plans vary based on industry requirements and operational needs. Manufacturing operations might focus on product specifications and testing procedures.
Service industries emphasize customer satisfaction metrics and service delivery standards. Construction projects require specific quality control measures for materials and workmanship.
Technology companies implement quality control plans for software development and testing.
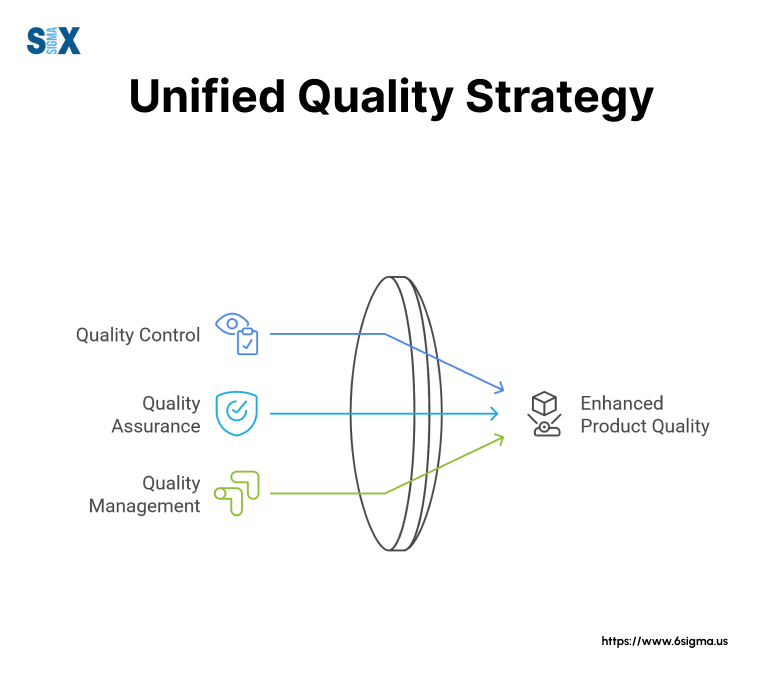
Steps To Write An Effective Quality Control Plan
Creating an effective quality control plan requires systematic planning and clear documentation. Organizations must follow specific steps to ensure their plan addresses all quality aspects while remaining practical and implementable.
Setting Quality Objectives And Standards
The first step involves defining clear, measurable quality objectives that align with organizational goals. These objectives should specify acceptable quality levels, performance metrics, and customer requirements.
Standards must be specific enough to measure but flexible enough to accommodate process improvements. For example, a manufacturing facility might set objectives for product defect rates, while a service organization could focus on customer satisfaction scores.
Identifying Key Processes And Activities
Quality control plans must outline the essential processes that impact product or service quality. This includes mapping production workflows, identifying critical control points, and determining potential quality risks.
Each process requires detailed documentation of standard operating procedures and quality checkpoints. The plan should also address process inter-dependencies and their potential impact on quality outcomes.
Assigning Roles And Responsibilities
Success in quality control depends on clear role assignment and accountability. The plan must specify who oversees quality checks, conducts inspections, and manages corrective actions.
This section should detail the quality control team structure, reporting relationships, and specific responsibilities for each team member.
Training requirements and qualification standards for quality personnel should also be included.
Establishing Inspection And Testing Procedures
Detailed inspection and testing protocols form the backbone of quality control plans. These procedures must specify testing frequencies, sampling methods, and acceptance criteria.
The plan should outline equipment calibration requirements, testing documentation, and procedures for handling non-conforming items.
Organizations must also establish clear guidelines for test result interpretation and decision-making processes.
Developing Documentation And Reporting Systems
Effective quality control requires robust documentation and reporting mechanisms.
The plan should specify required forms, checklists, and reports for quality monitoring. Modern quality control plans often incorporate digital tools for real-time data collection and analysis.
Documentation systems must enable easy tracking of quality metrics and facilitate quick identification of quality trends.
Planning For Continuous Improvement
The final step involves establishing mechanisms for ongoing quality improvement.
This includes procedures for reviewing quality data, identifying improvement opportunities, and implementing corrective actions.
The plan should outline schedules for quality audits, management reviews, and system updates. Regular evaluation of quality metrics helps organizations adapt their quality control plans to changing business needs.
Implementation Timeline And Resources
The quality control plan must include realistic timelines for implementation and resource allocation.
This involves scheduling training sessions, acquiring necessary equipment, and establishing monitoring systems.
Organizations should also consider budget requirements and potential return on investment from quality improvements.
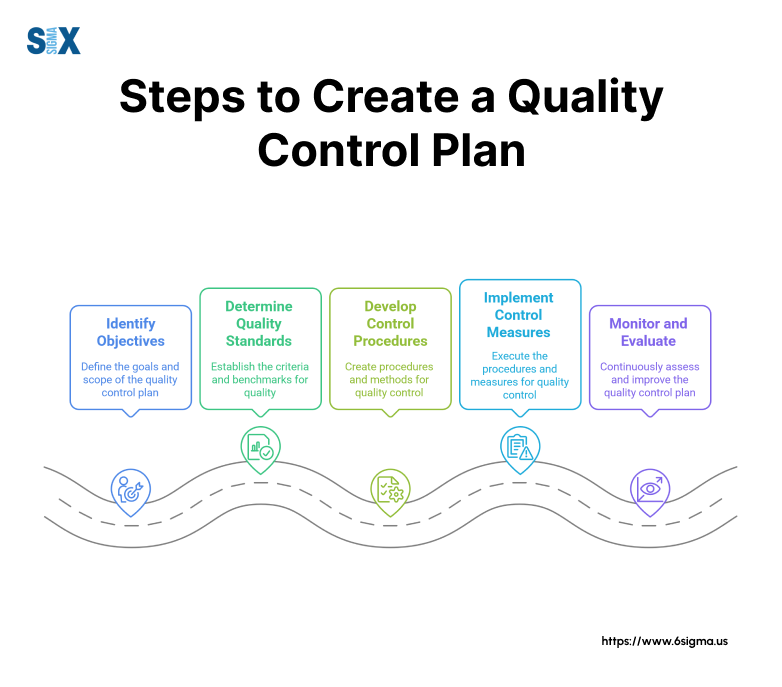
Essential Elements Of A Quality Control Plan
Every successful quality control plan contains specific elements that ensure its effectiveness and practicality.
These components work together to create a structured approach to quality management that meets both organizational goals and industry standards.
Defining Scope And Quality Objectives
The scope section establishes boundaries for quality control activities and sets clear, measurable objectives. This element should specify which products, services, or processes fall under the plan’s purview.
Quality objectives must align with business goals while remaining specific and achievable. For example, a manufacturing facility might target a 99.9% first-pass yield rate, while a service organization could aim for a 95% customer satisfaction score.
Establishing Organizational Structure
Quality control plans must outline clear reporting relationships and decision-making authority. This includes defining the roles of quality managers, inspectors, and team leaders.
The organizational structure should show how quality teams interact with other departments and specify escalation paths for quality issues.
Clear authority lines ensure quick resolution of quality concerns and effective implementation of corrective measures.
Allocating Resources And Personnel
Resource allocation details the equipment, tools, and personnel needed for quality control activities. This section should specify required testing equipment, monitoring devices, and software systems.
Personnel requirements must include staffing levels, shift coverage, and backup personnel arrangements. The plan should also address budget considerations for quality control activities.
Implementing Quality Standards
Quality standards form the foundation of effective quality control plans. This element details product specifications, acceptable tolerance ranges, and performance criteria.
Standards should reference relevant industry regulations and customer requirements. The plan must specify methods for measuring compliance with these standards and procedures for updating them as needed.
Designing Inspection Procedures
Inspection and testing procedures outline how quality checks will be performed. This includes sampling methods, test frequencies, and measurement techniques.
The plan should specify calibration requirements for testing equipment and provide detailed instructions for conducting each type of inspection.
Documentation requirements for test results and inspection findings must be clearly defined.
Managing Non-Conformance
Procedures for handling non-conforming products or services are crucial.
The plan must specify authority levels for disposition decisions and outline procedures for implementing corrective actions. Clear guidelines for preventing recurrence of quality issues should be included.
Maintaining Documentation Systems
Documentation requirements ensure consistent record-keeping across quality control activities. The plan should specify required forms, reports, and data collection methods.
Modern quality control plans often incorporate digital documentation systems for easier tracking and analysis. Record retention policies and access controls must be clearly defined.
Developing Training Programs
Training requirements ensure personnel possess necessary skills for quality control tasks.
This element should outline initial training programs, ongoing skill development, and competency assessment methods.
The plan must specify qualification requirements for different quality control roles and establish procedures for maintaining training records.
Each element of the quality control plan plays a vital role in maintaining product quality and process efficiency.
Regular review and updates of these elements ensure the plan remains effective and adapts to changing business needs.
Organizations should tailor these elements to their specific operations while maintaining alignment with industry standards and customer expectations.
Quality Control Plan Examples Across Industries
Different industries require unique approaches to quality control, tailored to their specific processes and requirements.
These examples demonstrate how quality control plans adapt to various business environments while maintaining core quality principles.
Manufacturing Quality Control Plan Example
Manufacturing quality control plans focus on product specifications and production processes.
A metal fabrication company’s quality control plan typically includes incoming material inspection protocols, in-process testing requirements, and final product verification steps.
The plan specifies measurement tolerances, sampling frequencies, and equipment calibration schedules.
Key elements include:
- Statistical process control methods for monitoring production variations
- Equipment maintenance and calibration schedules
- Product testing protocols at various production stages
- Defect classification and handling procedures
- Material traceability requirements
Construction Quality Control Plan Example
Construction projects require quality control plans that address both materials and workmanship.
These plans outline inspection requirements for each construction phase, from foundation work to final finishing.
The plan includes specific checkpoints for structural elements, mechanical systems, and architectural features.
Quality requirements cover:
- Material testing and verification procedures
- Inspection schedules for different construction phases
- Subcontractor quality requirements
- Safety compliance measures
- Documentation requirements for building code compliance
Software Development Quality Control Plan Example
Software quality control plans emphasize code quality, functionality testing, and user experience.
These plans detail testing methodologies for different development stages and specify acceptance criteria for software releases.
The plan includes:
- Code review protocols and standards
- Unit testing requirements
- Integration testing procedures
- User acceptance testing criteria
- Bug tracking and resolution procedures
- Performance testing parameters
Service Industry Quality Control Plan Example
Service-oriented businesses focus their quality control plans on customer experience and service delivery standards.
A hospitality company’s plan might address service timing, customer interaction protocols, and facility maintenance standards.
Key components include:
- Service delivery standards and timing requirements
- Customer feedback collection methods
- Staff performance metrics
- Quality audit procedures
- Service recovery protocols
Implementing Industry-Specific Quality Measures
Each industry example demonstrates how quality control plans adapt to specific operational needs while maintaining essential quality management principles.
These plans share common elements like documentation requirements and corrective action procedures but differ in their specific quality metrics and control methods.
Customizing Quality Control Templates
Organizations can use these examples as starting points for developing their own quality control plans.
The key lies in adapting these templates to specific operational requirements while maintaining alignment with industry standards and regulatory requirements.
Regular updates ensure these plans remain effective as business needs evolve.
Modern Approaches To Quality Control
Quality control methods have evolved significantly with technological advancements and new management philosophies.
Modern organizations now integrate various methodologies to create more effective quality control plans that meet current market demands.
Six Sigma In Quality Control Planning
Six Sigma methodology brings statistical precision to quality control processes. This data-driven approach focuses on reducing defects to 3.4 per million opportunities.
Organizations implementing Six Sigma in their quality control plans use specific tools like DMAIC (Define, Measure, Analyze, Improve, Control) to solve quality issues.
The methodology requires detailed measurement systems and statistical analysis to identify process variations and implement improvements.
Lean Manufacturing Integration
Lean principles enhance quality control plans by eliminating waste and streamlining processes. This approach emphasizes continuous flow, pull systems, and standardized work procedures.
Quality control teams using lean principles focus on value-adding activities while removing unnecessary steps that might introduce errors.
The methodology promotes visual management tools and quick feedback loops to maintain quality standards.
Total Quality Management Implementation
TQM approaches quality control as an organization-wide responsibility. This methodology integrates quality considerations into every business process and decision.
Modern quality control plans incorporating TQM principles emphasize employee involvement, customer focus, and continuous improvement.
Organizations implement cross-functional teams and regular quality circles to identify and address quality issues proactively.
Industry 4.0 And Digital Quality Control
Digital transformation has revolutionized quality control processes through automated monitoring and real-time data analysis.
Smart sensors and IoT devices now provide continuous quality monitoring, while artificial intelligence systems predict potential quality issues before they occur.
Modern quality control plans must account for:
- Digital data collection and analysis systems
- Real-time quality monitoring capabilities
- Automated inspection processes
- Predictive maintenance programs
- Cloud-based quality management systems
Integration Of Multiple Quality Methodologies
Modern organizations often combine elements from different quality control approaches to create more robust systems.
This hybrid approach allows quality control plans to address various operational aspects while maintaining flexibility.
Teams might use Six Sigma tools for specific problem-solving while implementing lean principles for daily operations.
Technology-Enabled Quality Control
Advanced technology now enables remote quality monitoring and virtual inspections.
Quality control plans must incorporate these new capabilities while ensuring data security and system reliability.
Digital tools provide:
- Real-time quality metrics dashboards
- Automated quality alert systems
- Digital documentation and tracking
- Remote inspection capabilities
- Advanced analytics for quality improvement
Future Trends In Quality Control
Quality control continues to evolve with new technologies and methodologies.
Organizations must prepare their quality control plans for emerging trends like blockchain for quality verification, augmented reality for quality inspections, and machine learning for defect detection.
These advances promise greater accuracy and efficiency in quality control processes.
The integration of modern approaches requires careful planning and systematic implementation. Organizations should evaluate their specific needs and capabilities when incorporating these methodologies into their quality control plans.
Regular assessment and updates ensure these modern approaches continue to meet evolving quality requirements and operational needs.
Master Six Sigma methodologies to revolutionize your quality control processes. Join our Six Sigma Champion Leadership Program.
Implementing And Maintaining A Quality Control Plan
Successful implementation of a quality control plan requires dedicated effort and systematic maintenance.
Organizations must focus on proper training, consistent monitoring, and regular updates to ensure their quality planning efforts yield desired results.
Employee Training And Development
Effective training forms the foundation of quality control plan implementation.
Organizations must develop structured training programs that cover quality procedures, testing methods, and documentation requirements.
New employees need orientation sessions focusing on quality standards, while existing staff require regular refresher training.
Training programs should include:
- Technical skills development for quality testing procedures
- Documentation and reporting requirements training
- Quality tools and equipment operation instruction
- Problem-solving methodology education
- Team collaboration and communication training
Performance Monitoring Systems
Regular performance monitoring ensures the quality control plan meets its objectives. Organizations must establish clear metrics and measurement systems to track quality performance.
Daily monitoring activities should focus on key quality indicators while tracking longer-term trends. Modern monitoring systems often incorporate digital tools for real-time data collection and analysis.
Quality Metrics And Measurement
Successful quality planning requires specific, measurable indicators to evaluate performance. Organizations should track both leading and lagging indicators of quality performance.
Key measurements might include defect rates, customer complaints, process capability indices, and first-pass yield rates.
Regular analysis of these metrics helps identify trends and potential issues before they become significant problems.
Conducting Quality Audits
Regular audits verify compliance with quality control procedures and identify improvement opportunities.
Internal audits should occur on a scheduled basis, while external audits provide independent verification of quality systems.
Audit findings must be documented and addressed through formal corrective action processes.
Organizations should:
- Schedule regular internal quality audits
- Prepare for external certification audits
- Document audit findings thoroughly
- Track corrective actions to completion
- Verify the effectiveness of implemented changes
Review And Update Procedures
Quality control plans require regular reviews and updates to remain effective. Organizations should establish formal review schedules and update procedures.
Changes in processes, equipment, or requirements must trigger plan updates. The review process should involve key stakeholders and consider feedback from all levels of the organization.
Feedback Integration Systems
Employee and customer feedback provides valuable insights for improving quality control plans. Organizations should establish formal channels for collecting and reviewing feedback.
This information helps identify practical improvements and ensures the plan remains relevant to actual operational needs.
Continuous Improvement Process
Quality planning must incorporate mechanisms for continuous improvement. Organizations should regularly evaluate their quality control procedures and implement necessary changes.
This involves analyzing performance data, reviewing industry best practices, and incorporating new technologies when appropriate.
Documentation Management
Maintaining current documentation supports effective quality control implementation. Organizations must establish systems for managing quality documents and records.
This includes version control procedures, document access controls, and retention policies. Digital document management systems can streamline these processes while ensuring consistency.
Quality control plan implementation requires ongoing commitment and resources. Organizations must balance the need for consistent procedures with the flexibility to adapt to changing requirements.
Regular evaluation and updates ensure the plan continues to support quality objectives while meeting operational needs.
ROI And Benefits Of Quality Control Plans
Implementing a quality control plan delivers measurable returns across multiple business areas.
Organizations that invest in quality control systems often see significant improvements in operational efficiency and market position.
Product And Service Quality Improvements
Quality control plans drive substantial improvements in product and service delivery. Organizations typically experience reduced defect rates and increased consistency in their outputs.
Manufacturing operations often report higher first-pass yield rates, while service organizations see fewer customer complaints.
These improvements lead to reduced rework costs and increased production efficiency.
Customer Satisfaction And Loyalty
Enhanced quality control processes directly impact customer satisfaction levels. Consistent product quality builds customer trust and encourages repeat business.
Organizations with effective quality control plans report higher customer retention rates and increased referral business.
The resulting customer loyalty provides a stable revenue base and reduces marketing costs for new customer acquisition.
Operational Cost Reduction
Quality control plans generate significant cost savings through various channels. Reduced waste and rework requirements lower material costs.
Better process control decreases production downtime and improves resource utilization.
Organizations also benefit from lower warranty claims and reduced customer service expenses. These savings often exceed the initial investment in quality control systems.
Brand Value Enhancement
Strong quality control measures strengthen brand reputation in the marketplace. Organizations known for consistent quality command premium prices and attract quality-conscious customers.
This enhanced market position provides competitive advantages and supports business growth. The resulting brand value becomes a significant business asset.
Regulatory Compliance Benefits
Quality control plans help organizations maintain compliance with industry regulations and standards. This proactive approach reduces audit findings and potential penalties.
Organizations also spend less time addressing compliance issues, allowing teams to focus on improvement initiatives.
The documented procedures provide evidence of due diligence in meeting regulatory requirements.
Lead your organization’s quality transformation. Become a certified Six Sigma Champion.
Conclusion
Quality control plans serve as essential tools for maintaining operational excellence and driving business success.
These structured approaches to quality management deliver both immediate and long-term benefits across organizations.
The key elements of successful quality control plans include clear procedures, effective training programs, and regular monitoring systems.
Adapting To Organizational Needs
Each organization must tailor its quality control plan to specific operational requirements and industry standards.
This customization ensures the plan addresses unique challenges while maintaining alignment with business objectives. Regular reviews and updates keep the plan relevant as business needs evolve.
Moving Forward With Quality Control
Organizations should prioritize the development and implementation of robust quality control plans.
The investment in quality systems generates returns through improved efficiency, reduced costs, and enhanced market position.
Success requires commitment from leadership and active participation from all organizational levels.
Quality control plans will continue evolving with technological advances and changing market requirements.
Organizations must stay current with industry trends and best practices while maintaining focus on fundamental quality principles.
The future of quality control lies in balancing traditional quality methods with modern digital tools and automated systems.
SixSigma.us offers both Live Virtual classes as well as Online Self-Paced training. Most option includes access to the same great Master Black Belt instructors that teach our World Class in-person sessions. Sign-up today!
Virtual Classroom Training Programs Self-Paced Online Training Programs