Continuous Flow Manufacturing: The Guide to Streamlined Production
Between this competition market demands a quick production process with better quality control and reduced waste.
To give a boost and streamline this method continues flow manufacturing plays a big role.
Key Highlights
- Understanding continuous flow production fundamentals
- Real-world examples of successful implementations
- Benefits over traditional batch manufacturing
- Implementation strategies for different industries
- Technology requirements and system integration
- Cost considerations and ROI analysis
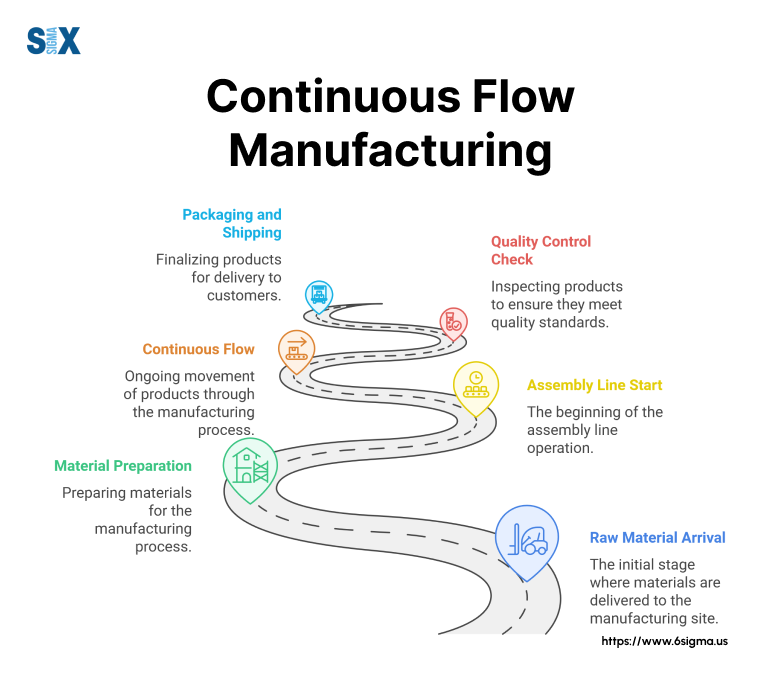
What is Continuous Flow Manufacturing?
Continuous flow manufacturing represents a production approach where materials move seamlessly through each stage of the manufacturing process without interruption.
The concept gained prominence when Henry Ford introduced the moving assembly line in 1913.
The Evolution
The story of continuous flow manufacturing begins in the early 20th century, marking a significant shift from traditional craftsman-style production methods.
The Ford Assembly Line Revolution
In 1913, Henry Ford introduced the first moving assembly line at the Highland Park Plant in Michigan. This innovation reduced the time to build a Model T car from 12 hours to just 2.5 hours.
Ford’s assembly line created a systematic approach where each worker performed specific tasks as vehicles moved through the production process.
The success of Ford’s method sparked widespread adoption across various industries.
Toyota’s Game-Changing Production System
The 1950s brought another major advancement when Toyota developed its Production System (TPS).
Taiichi Ohno, Toyota’s chief engineer, refined Ford’s concepts by adding crucial elements that would define modern continuous flow lean manufacturing.
The Toyota Production System introduced several key innovations:
- Just-in-time production methods
- Built-in quality control measures
- Waste reduction strategies
- Worker empowerment programs
- Continuous improvement processes
These improvements addressed the rigidity of Ford’s original system while maintaining its efficiency benefits. Toyota’s approach proved that continuous flow manufacturing could be both efficient and flexible.
Modern Developments in Continuous Flow Manufacturing
The 1980s and 1990s saw manufacturing facilities worldwide adopting and adapting continuous flow principles.
- 1970s: Introduction of computer-controlled machinery
- 1980s: Implementation of automated quality control systems
- 1990s: Development of integrated production management software
- 2000s: Addition of real-time monitoring and analytics
- 2010s: Integration of IoT devices and smart sensors
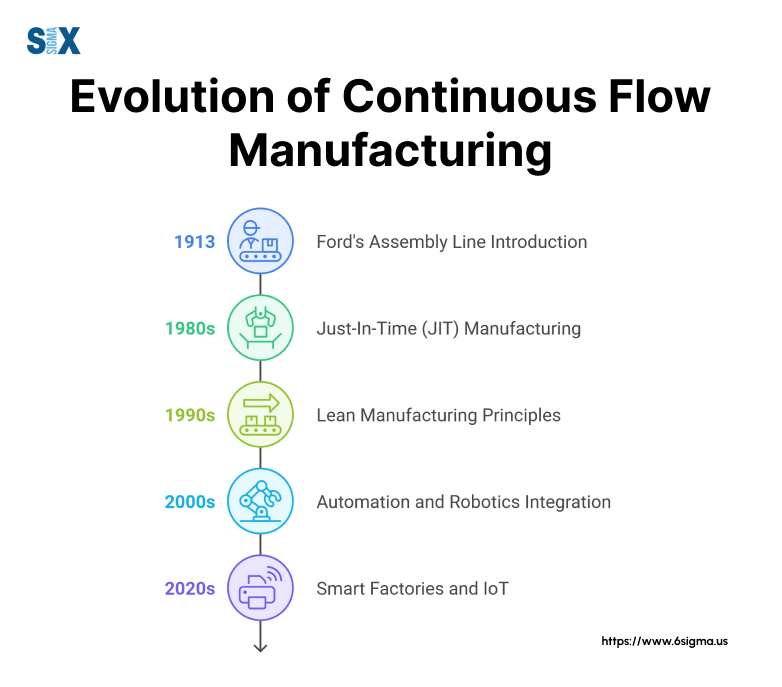
Impact on Modern Manufacturing
The principles established by Ford and refined by Toyota now form the foundation of modern manufacturing operations.
Core Principles and Components
There are 5 essential principles that work together to create efficient production systems.
These principles form the backbone of modern manufacturing operations and drive significant improvements in productivity and quality.
Just-In-Time Production: The Foundation of Continuous Flow Manufacturing (CFM)
Just-in-Time (JIT) production represents the heartbeat of continuous flow manufacturing.
This approach ensures materials arrive exactly when needed in the production process, eliminating excess inventory and reducing storage costs.
Pull Systems: Production Based on Demand
Pull systems operate on actual customer demand rather than forecasted needs. In continuous flow manufacturing, each production stage “pulls” materials from the previous stage only when needed.
This method prevents overproduction and reduces waste.
The Power of Kaizen: Never-Ending Improvement
Continuous improvement, known as Kaizen, drives ongoing refinement of manufacturing processes.
This principle encourages workers at all levels to identify and implement small, incremental improvements daily.
Manufacturing teams might hold regular Kaizen events where they:
- Analyze current processes
- Identify bottlenecks
- Implement solutions
- Measure results
- Refine improvements
Waste Reduction: Maximizing Resource Efficiency
Waste reduction focuses on eliminating eight key types of waste in flow production:
- Overproduction
- Waiting time
- Transportation
- Processing
- Inventory
- Motion
- Defects
- Unused employee creativity
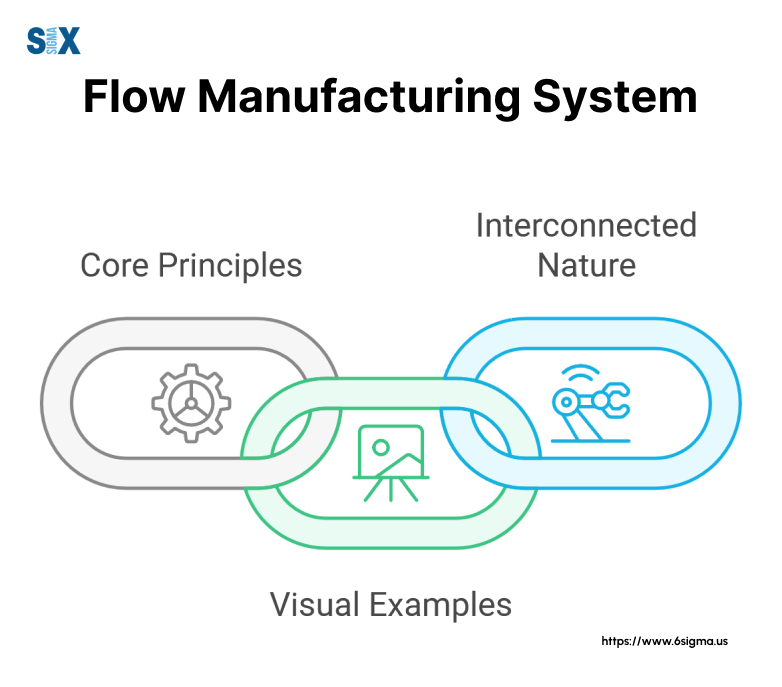
Standardized Work: Creating Consistency
Standardized work establishes consistent procedures for each production task. This principle ensures quality, reduces errors, and makes training new workers more efficient.
Manufacturing facilities document standard procedures for:
- Operation sequences
- Required tools and equipment
- Quality checkpoints
- Safety protocols
- Time requirements
Integration of Core Principles in Continuous Flow Manufacturing (CFM)
These five principles work together in continuous flow manufacturing to create smooth, efficient production systems.
When properly implemented, they reduce production time, improve quality, and lower costs.
Modern manufacturers often use digital tools to monitor and maintain these principles, ensuring optimal performance throughout the production process.
Continuous Flow Manufacturing vs. Batch Manufacturing
Understanding the differences between continuous flow processes and batch manufacturing helps organizations make informed decisions about their production methods.
Each approach offers distinct advantages and challenges depending on specific manufacturing needs.
Process Differences: Two Distinct Approaches
Continuous flow manufacturing moves products through production without interruption, creating a steady stream of output.
Products advance from one stage to the next immediately upon completion. For example, in beverage production, bottles move continuously through filling, capping, and labeling stations without stopping.
Batch manufacturing, however, processes products in groups or lots. Each batch must complete one stage before moving to the next. A pharmaceutical company might produce tablets in batches of 10,000 units, completing all steps for one batch before starting another.
Efficiency and Production Speed
Process flow manufacturing typically achieves higher efficiency rates through constant production.
A automotive assembly line using continuous flow might produce vehicles every few minutes, maintaining steady output throughout the day.
Batch production often faces efficiency challenges due to:
- Setup times between batches
- Equipment cleaning requirements
- Material handling delays
- Production line reconfigurations
Quality Control and Monitoring
Quality control in continuous flow processes happens in real-time, allowing immediate detection and correction of issues.
Manufacturing facilities can implement automated quality checks throughout the production line, reducing defect rates significantly.
Batch manufacturing relies on end-of-batch quality testing, which may result in entire batches being rejected if problems are found. This approach can lead to higher waste rates and increased production costs.
Production Flexibility and Market Response
Each manufacturing method offers different levels of flexibility:
Continuous Flow Manufacturing:
- Rapid response to demand changes
- Limited product variation capabilities
- Difficult to modify processes quickly
- Best for stable, high-volume production
Batch Manufacturing:
- Easy product changeovers
- Greater variety possibilities
- Simple process modifications
- Suitable for custom orders
Cost Structure and Resource Utilization
The financial implications of each method vary significantly. Continuous flow manufacturing generally requires:
- Higher initial investment
- Lower per-unit production costs
- Reduced inventory expenses
- Minimal labor costs per unit
Batch manufacturing typically involves:
- Lower startup costs
- Higher per-unit production costs
- Increased inventory expenses
- Greater labor costs per unit
Key Differences at a Glance
Aspect | Continuous Flow | Batch Manufacturing |
---|---|---|
Production Speed | Constant output | Intermittent output |
Setup Time | Minimal | Frequent |
Quality Control | Real-time | End of batch |
Product Variety | Limited | High |
Initial Investment | Higher | Lower |
Operating Costs | Lower per unit | Higher per unit |
Inventory Levels | Minimal | Higher |
Market Response | Faster | Slower |
Making the Right Choice
Selecting between continuous flow and batch manufacturing depends on several factors:
- Product characteristics
- Production volumes
- Market demands
- Available resources
- Quality requirements
Benefits and Advantages of Continuous Flow Manufacturing (CFM)
Manufacturing organizations implementing continuous flow processes consistently report significant improvements across multiple performance metrics.
These advantages directly impact both operational efficiency and bottom-line results.
Reduced Lead Times Drive Market Responsiveness
Production flow systems dramatically cut lead times by eliminating waiting periods between processes.
Manufacturing facilities typically report 50-70% reductions in order-to-delivery timeframes. For example, an electronics manufacturer reduced their product delivery time from 15 days to just 4 days after implementing continuous flow processes.
The shortened lead times result in:
- Faster market response
- Reduced customer waiting periods
- Better competitive positioning
- Increased order fulfillment rates
Quality Control Excellence Through Real-Time Monitoring
Continuous process manufacturing enables immediate quality checks throughout production.
Rather than discovering defects after completing entire batches, problems are identified and resolved instantly.
Manufacturing plants often report defect rate reductions of up to 90% after switching to continuous flow systems.
Quality improvements manifest through:
- Instant defect detection
- Immediate process adjustments
- Reduced material waste
- Consistent product quality
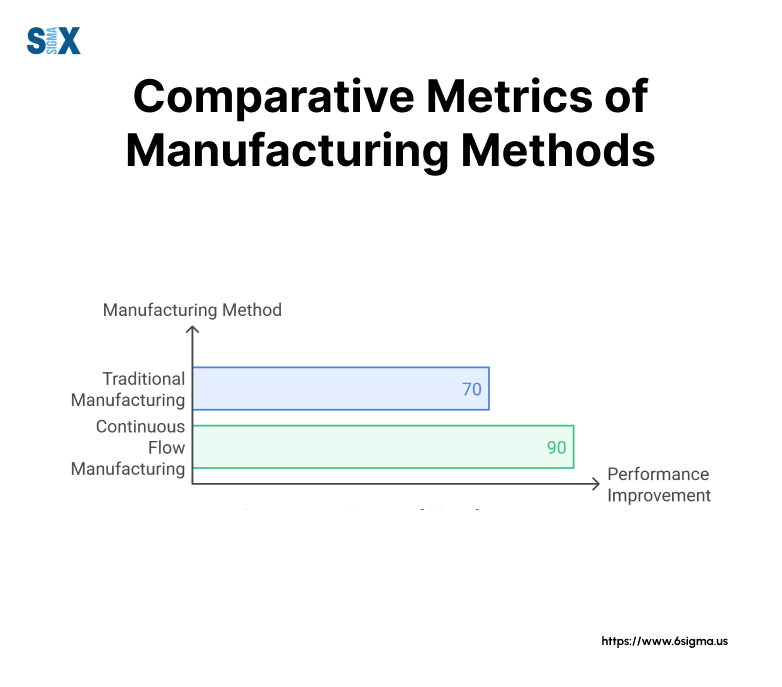
Discover how our Green Belt certification can help you reduce defects by up to 70% through statistical process control.
Inventory Cost Reduction Through Efficient Management
Organizations using continuous flow manufacturing typically achieve 30-50% reductions in inventory costs.
This improvement comes from eliminating the need for large material stockpiles and work-in-progress inventory.
A furniture manufacturer, for instance, reduced their inventory holding costs by 45% within six months of implementing continuous flow processes.
Their warehouse space requirements decreased by 60%, leading to significant cost savings in storage and handling.
Productivity Gains Through Streamlined Operations with Continuous Flow Manufacturing
Production flow improvements consistently deliver measurable productivity gains. Manufacturing facilities report:
- 20-35% increase in output per worker
- 40-60% reduction in production cycle times
- 25-40% improvement in equipment utilization
- 15-30% decrease in labor costs
Enhanced Customer Satisfaction Through Reliable Delivery
Continuous flow manufacturing directly impacts customer satisfaction through:
- Consistent Product Quality
- Fewer defects
- Better product uniformity
- Reliable performance
- Improved Delivery Performance
- On-time delivery rates above 95%
- Shorter waiting periods
- Flexible order quantities
- Competitive Pricing
- Lower production costs
- Reduced overhead expenses
- Better value proposition
Measurable Impact on Business Performance with Continuous Flow Manufacturing
The combined benefits of continuous flow manufacturing create substantial business improvements:
Financial Benefits:
- 15-25% reduction in operating costs
- 20-30% improvement in profit margins
- 30-40% decrease in working capital needs
Operational Benefits:
- 40-60% reduction in production space
- 50-70% decrease in production time
- 80-90% improvement in inventory turnover
These measurable advantages make continuous flow manufacturing an attractive option for organizations seeking to improve their operational efficiency and market competitiveness.
Implementing Continuous Flow Manufacturing: A Step-by-Step Guide
Transitioning to continuous flow manufacturing requires careful planning and systematic execution.
Assessing Current Manufacturing Process Flows
The first step involves analyzing existing operations to identify improvement opportunities.
Manufacturing teams should document:
- Current production rates and cycles
- Equipment placement and utilization
- Material movement patterns
- Bottlenecks and delays
- Quality control points
This assessment provides baseline metrics for measuring future improvements and highlights areas needing immediate attention.
Identifying and Mapping Value Streams with Continuous Flow Manufacturing
Value stream mapping reveals the flow of materials and information through the manufacturing process.
This critical step helps organizations:
- Track material movement paths
- Document information flow
- Identify non-value-adding activities
- Measure process timing
- Locate improvement opportunities
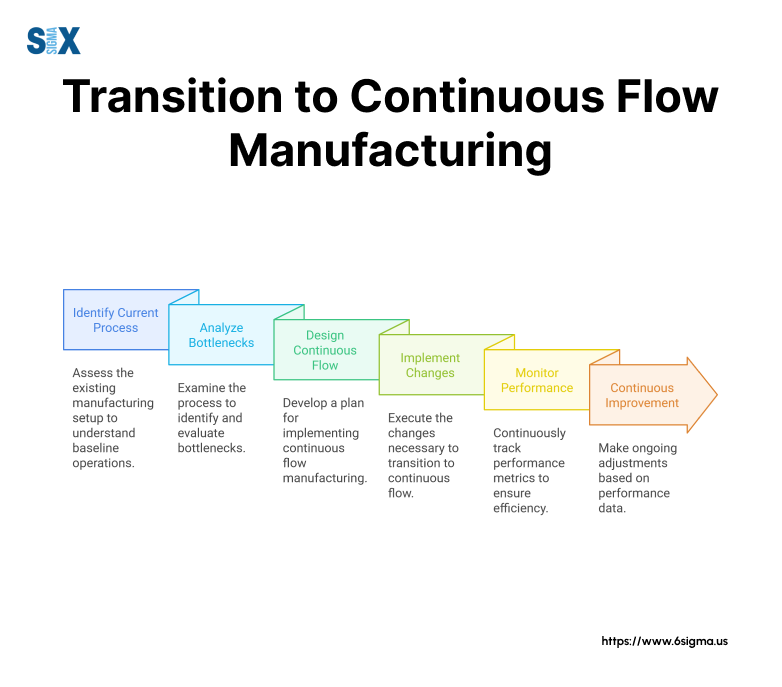
Designing an Optimized Factory Layout
The physical layout design significantly impacts process flow for manufacturing success. Key considerations include:
Equipment Placement:
- Minimize transport distances
- Enable smooth material flow
- Reduce operator movement
- Optimize space utilization
Workstation Design:
- Ergonomic considerations
- Tool accessibility
- Material presentation
- Quality check points
Employee Training and Development Programs
Successful implementation requires well-trained staff who understand continuous flow principles. Training programs should cover:
- Basic Concepts
- Process flow fundamentals
- Quality control procedures
- Problem-solving methods
- Standard work practices
- Technical Skills
- Equipment operation
- Maintenance procedures
- Quality inspection methods
- Data recording systems
Technology Integration and Support Systems
Modern manufacturing process flows rely on supporting technologies for optimal performance:
Essential Systems:
- Production monitoring software
- Quality control systems
- Inventory management tools
- Maintenance tracking programs
- Performance analytics platforms
Monitoring Performance and Making Adjustments with Continuous Flow Manufacturing
Regular monitoring ensures the continuous flow system performs optimally.
Organizations should track:
Key Metrics:
- Production rates
- Quality levels
- Equipment efficiency
- Material flow
- Employee productivity
Performance Reviews:
- Daily operational meetings
- Weekly progress assessments
- Monthly performance analysis
- Quarterly strategy reviews
Implementation Timeline and Milestones
A typical implementation schedule spans several months:
Months 1-2:
- Complete initial assessment
- Map value streams
- Design new layout
Months 3-4:
- Train key personnel
- Install new equipment
- Configure support systems
Months 5-6:
- Begin phased implementation
- Monitor performance
- Make necessary adjustments
This structured approach to implementing continuous flow manufacturing helps organizations avoid common pitfalls while ensuring steady progress toward their operational goals.
Transform your manufacturing processes with our Design for Six Sigma Green Belt training.
Cost Analysis and ROI of Continuous Flow Manufacturing
Making the switch to continuous flow manufacturing requires careful financial planning and analysis.
Understanding the costs, savings, and potential returns helps organizations make informed decisions about their manufacturing investments.
Initial Investment Requirements
The upfront costs of implementing flow manufacturing processes vary based on facility size and existing infrastructure.
Typical investments include:
Equipment and Technology:
- Production line modifications
- Automation systems
- Quality control equipment
- Material handling systems
- Software and monitoring tools
Facility Updates:
- Layout reconfiguration
- Utility modifications
- Storage system changes
- Workstation improvements
Operational Cost Reductions with Continuous Flow Manufacturing
Process flow in manufacturing brings significant operational savings through multiple channels.
Organizations typically see reductions in:
Labor Costs:
- 20-30% decrease in direct labor
- 15-25% reduction in supervision needs
- 30-40% less overtime requirements
Material Costs:
- 25-35% reduction in waste
- 40-50% lower inventory holding costs
- 20-30% decrease in damaged materials
Long-Term Financial Benefits of Continuous Flow Manufacturing
The financial impact of continuous flow manufacturing extends well beyond immediate cost savings:
Revenue Improvements:
- Increased production capacity
- Higher product quality
- Better market responsiveness
- Enhanced customer satisfaction
Efficiency Gains:
- Reduced energy consumption
- Lower maintenance costs
- Improved space utilization
- Decreased transportation expenses
Real Investment Scenarios
Small Manufacturing Operation:
- Initial Investment: $500,000
- Annual Savings: $200,000
- ROI Timeline: 2.5 years
- Five-year Return: 200%
Medium-sized Facility:
- Initial Investment: $2 million
- Annual Savings: $800,000
- ROI Timeline: 2.5 years
- Five-year Return: 200%
Large Manufacturing Plant:
- Initial Investment: $5 million
- Annual Savings: $2.5 million
- ROI Timeline: 2 years
- Five-year Return: 250%
Financial Planning Considerations
Organizations should consider several factors when planning their investment:
Implementation Phases:
- Initial assessment and planning
- Pilot program implementation
- Full-scale rollout
- Ongoing optimization
Funding Options:
- Capital investment
- Equipment financing
- Operational leasing
- Phased implementation
This financial analysis demonstrates that while continuous flow manufacturing requires significant upfront investment, the long-term returns often justify the costs.
Organizations typically achieve full ROI within 2-3 years, with ongoing benefits continuing to accumulate through improved efficiency and reduced operational costs.
Case Studies: Continuous Flow Manufacturing in Action
Major manufacturers across various industries have successfully implemented continuous flow manufacturing, achieving remarkable results.
Boeing: Revolutionizing Aircraft Production
Boeing transformed its 737 aircraft production through continuous flow manufacturing, setting new standards in aerospace manufacturing. The implementation resulted in:
Production Improvements:
- Assembly time reduced from 28 to 11 days
- Production rate increased to 47 aircraft monthly
- Defect rates decreased by 65%
- Work-in-progress inventory reduced by 55%
The company achieved these results by reorganizing their production floor into a linear flow, implementing moving assembly lines, and standardizing work processes across all stations.
Toyota: Setting the Global Standard
Toyota’s Georgetown, Kentucky plant demonstrates excellence in continuous flow manufacturing example through their renowned production system. Key achievements include:
Operational Metrics:
- Vehicle completion every 55 seconds
- Quality ratings above 99%
- Same-day order fulfillment
- Minimal inventory holding
Their success stems from rigorous implementation of flow production principles, including standardized work procedures, visual management systems, and continuous improvement practices.
Harley-Davidson: Streamlining Motorcycle Assembly
Harley-Davidson’s York facility showcases the power of continuous flow manufacturing in custom vehicle production. Their transformation delivered:
Measurable Results:
- Production time cut by 60%
- Inventory costs reduced by 75%
- Quality improvements of 70%
- Labor efficiency increased by 80%
The motorcycle manufacturer achieved these improvements by redesigning their facility layout, implementing pull systems, and establishing standardized work procedures.
NestlƩ: Optimizing Food Production
NestlĆ©’s application of continuous flow manufacturing in their beverage production demonstrates success in the food industry. Their implementation showed:
Performance Gains:
- Production efficiency up 35%
- Energy consumption down 25%
- Water usage reduced by 40%
- Product consistency improved by 50%
These case studies demonstrate that regardless of industry or product complexity, continuous flow manufacturing can deliver significant improvements in productivity, quality, and cost efficiency when properly implemented and maintained.
Challenges and Troubleshooting
While continuous process manufacturing offers numerous benefits, organizations often face various challenges during implementation and operation.
Common Implementation Hurdles of Continuous Flow Manufacturing (CFM)
The transition to continuous flow manufacturing frequently encounters several obstacles that require careful navigation:
Technical Challenges:
- Equipment compatibility issues
- System integration problems
- Layout constraints
- Technology adaptation needs
Resource Limitations:
- Budget restrictions
- Skilled labor shortages
- Time constraints
- Training requirements
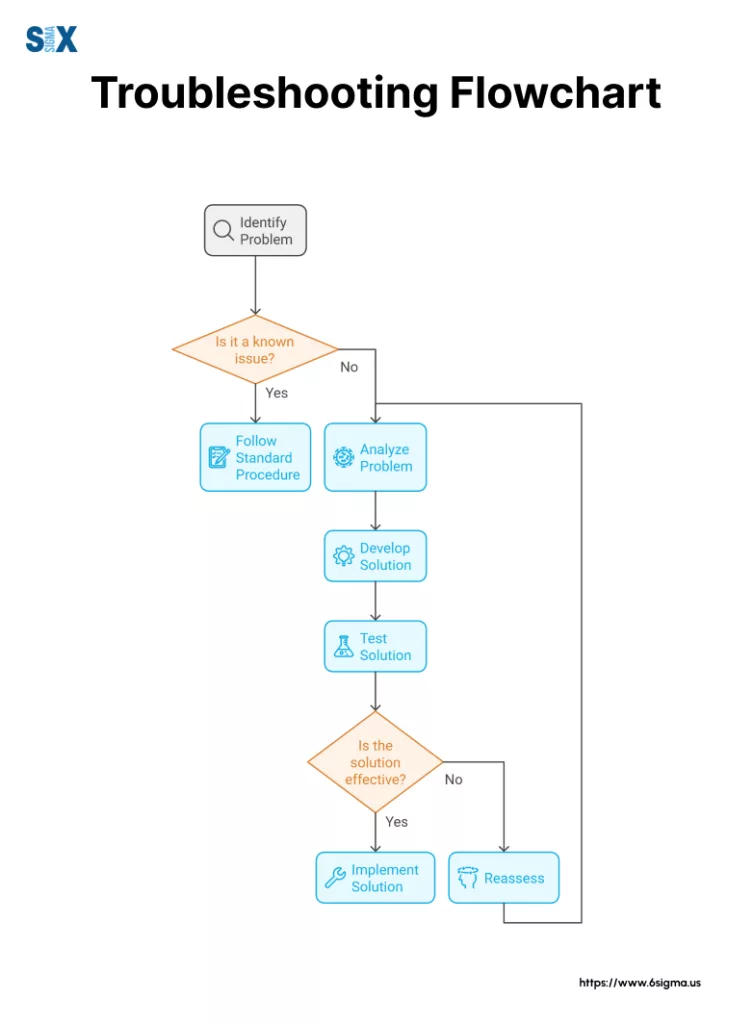
Managing Process Variability
Production process flow can be disrupted by various types of variability. Successful organizations address these through systematic approaches:
Equipment Variability:
- Regular maintenance schedules
- Performance monitoring systems
- Backup equipment availability
- Quick-response repair protocols
Product Variability:
- Standardized procedures
- Quality control checkpoints
- Process control systems
- Operator training programs
Supply Chain Disruption Management
Supply chain issues can severely impact continuous flow operations. Effective mitigation strategies include:
Risk Management Approaches:
- Multiple supplier relationships
- Safety stock maintenance
- Alternative material sources
- Transportation backup plans
Communication Systems:
- Real-time inventory tracking
- Supplier performance monitoring
- Demand forecasting tools
- Emergency response protocols
Overcoming Resistance to Change with Continuous Flow Manufacturing
Employee resistance often presents significant challenges during implementation. Successful strategies focus on:
Leadership Actions:
- Clear communication of benefits
- Employee involvement in planning
- Recognition of improvement efforts
- Regular progress updates
Support Systems:
- Comprehensive training programs
- Mentoring relationships
- Performance incentives
- Feedback mechanisms
Troubleshooting Framework
When problems arise in continuous flow manufacturing, a structured approach helps resolve issues efficiently:
Problem Identification:
- Data collection and analysis
- Root cause investigation
- Impact assessment
- Priority setting
Solution Development:
- Option generation
- Feasibility analysis
- Implementation planning
- Results monitoring
Prevention and Maintenance Strategies with Continuous Flow Manufacturing
Preventing disruptions proves more effective than solving problems after they occur:
Preventive Measures:
- Regular equipment maintenance
- Process audits
- Staff training updates
- System upgrades
Monitoring Systems:
- Performance metrics tracking
- Quality control checks
- Equipment diagnostics
- Process analytics
Building Resilience in Production Systems
Organizations must develop robust systems that can handle various challenges:
System Design:
- Flexible production capabilities
- Redundant critical systems
- Scalable processes
- Adaptive technologies
Response Protocols:
- Emergency procedures
- Recovery plans
- Communication channels
- Resource allocation
These challenges, while significant, can be effectively managed through proper planning, monitoring, and response systems.
The Future of Manufacturing Excellence
Continuous flow manufacturing represents a significant evolution in production methodology, offering organizations powerful tools to improve efficiency, quality, and competitiveness.
The evidence presented throughout this guide demonstrates its transformative impact across various industries.
Key Insights for Manufacturing Success
The fundamental principles of CFM deliver measurable improvements in several critical areas.
Organizations implementing these systems consistently report reduced lead times, improved quality control, and significant cost savings.
The integration of modern technology with proven manufacturing methods creates robust, efficient production environments.
Success stories from industry leaders like Toyota, Boeing, and Harley-Davidson showcase the practical benefits of continuous flow systems.
The Path to Manufacturing Excellence with Continuous Flow Manufacturing
Implementation success requires careful planning and commitment. Organizations must consider:
- Strategic alignment with business goals
- Resource allocation and investment
- Employee training and development
- Technology integration requirements
- Continuous improvement processes
The financial benefits become evident through reduced operational costs, improved inventory management, and enhanced production efficiency.
Taking Action for Future Success
Organizations considering continuous flow manufacturing should begin by:
First Steps:
- Assessing current operations
- Identifying improvement opportunities
- Evaluating resource requirements
- Developing implementation plans
- Building internal support
The transition to CFM represents more than just a change in production methods.
It embodies a commitment to excellence, efficiency, and continuous improvement.
Moving Forward with Confidence
The evidence presented throughout this guide demonstrates that continuous flow manufacturing offers significant advantages for organizations willing to embrace change.
The combination of proven methodologies with modern technology creates powerful opportunities for manufacturing excellence.
Success requires:
- Clear vision and leadership
- Systematic implementation
- Employee engagement
- Technology integration
- Continuous monitoring and improvement
Organizations ready to explore continuous flow manufacturing should begin by conducting a thorough assessment of their current operations and developing a structured implementation plan.
The potential benefits – from improved efficiency to enhanced competitiveness – make this methodology worth serious consideration for any manufacturing organization focused on future success.
The journey toward manufacturing excellence through continuous flow principles starts with a single step.
Organizations that begin this journey today position themselves for success in an increasingly competitive manufacturing environment.
SixSigma.us offers both Live Virtual classes as well as Online Self-Paced training. Most option includes access to the same great Master Black Belt instructors that teach our World Class in-person sessions. Sign-up today!
Virtual Classroom Training Programs Self-Paced Online Training Programs