Lean Flow: The Ultimate Guide to Streamlining Your Business Processes
Imagine a workplace where tasks flow seamlessly, waste is minimized, and productivity soars. Welcome to the world of lean flow.
Understanding and implementing lean flow principles can be the key to unlocking unprecedented efficiency and success.
But what exactly is lean flow, and why is it so crucial for modern businesses?
Lean flow is a philosophy and set of practices derived from lean manufacturing that focuses on creating continuous, uninterrupted movement of work through a system.
It’s about optimizing processes, eliminating waste, and ensuring that value flows smoothly to the customer.
Key Highlights
- Lean flow meaning
- Fundamental principles
- Step-by-step implementation process
- Common barriers and solutions
- Essential metrics for measuring success
What is Lean Flow?
Lean flow, a cornerstone of modern efficiency strategies, is more than just a buzzword in business circles.
Lean flow meaning encompasses a systematic approach to optimizing processes and minimizing waste. But what is lean flow exactly?
Lean flow can be defined as a methodology that focuses on creating a smooth, uninterrupted flow of work through a system, ensuring that value is continuously delivered to the customer.
Transform your operations with lean principles with our Lean Introduction course provides the essential knowledge and tools to get started.
This lean flow definition emphasizes the importance of eliminating bottlenecks, reducing waiting times, and streamlining operations.
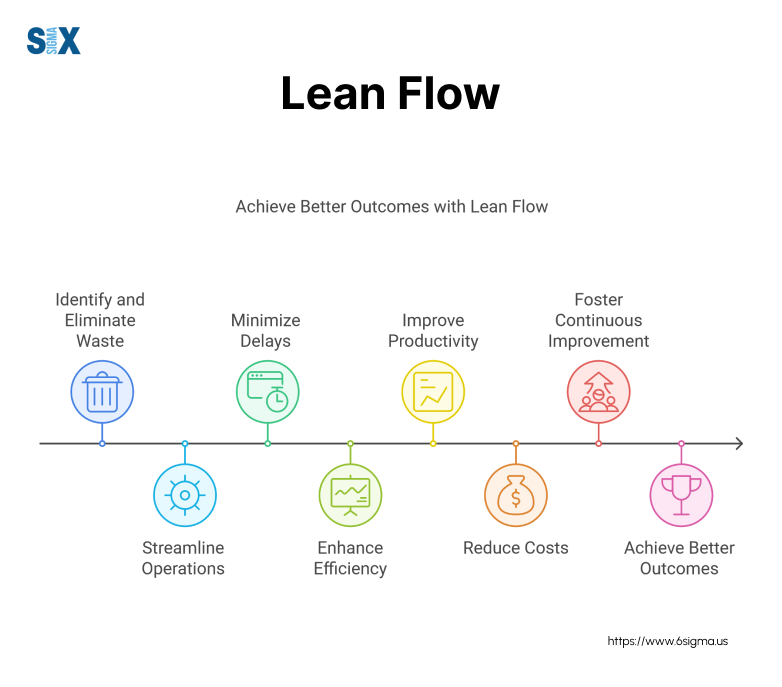
The key principles of lean flow include:
- Identifying value from the customer’s perspective
- Mapping the value stream to eliminate non-value-adding activities
- Creating flow by removing barriers between steps
- Establishing pull systems to respond to customer demand
- Continuously improving processes
These principles are closely related to broader lean manufacturing concepts, where flow in lean is considered crucial for achieving optimal efficiency.
By implementing lean flow, organizations can significantly reduce lead times, improve quality, and enhance overall productivity.
The Philosophy Behind Lean Flow
The lean flow philosophy has its roots in the Toyota Production System, developed in the mid-20th century.
This approach revolutionized manufacturing by focusing on eliminating waste and improving flow. However, the lean flow philosophy extends far beyond the factory floor.
Lean flow is about creating value for the customer while minimizing waste in all forms. This philosophy is built on core values such as:
- Respect for people
- Continuous improvement
- Long-term thinking
- Problem-solving at the source
What sets lean flow apart from traditional process management is its holistic approach.
While conventional methods often focus on optimizing individual steps, lean flow looks at the entire value stream.
This perspective allows organizations to identify and eliminate systemic inefficiencies that might be overlooked in a more siloed approach.
A lean flow chart is an essential tool in this philosophy, visually representing the flow of work and highlighting areas for improvement.
By using such visual aids, teams can more easily identify bottlenecks and waste in their processes.
In practice, implementing lean flow principles can lead to dramatic improvements.
As businesses continue to evolve, so does the application of lean flow. Today, we see lean flow principles being successfully applied in diverse sectors, from healthcare to software development.
The flexibility of this approach makes it adaptable to various contexts, always with the goal of creating more value with less waste.
By understanding and applying these lean flow principles, organizations can create more efficient, responsive, and customer-focused operations.
The Benefits of Implementing Lean Flow
Implementing lean flow principles can revolutionize your business operations, leading to significant improvements across various aspects of your organization.
Let’s explore the key benefits that make lean flow a game-changer in modern business.
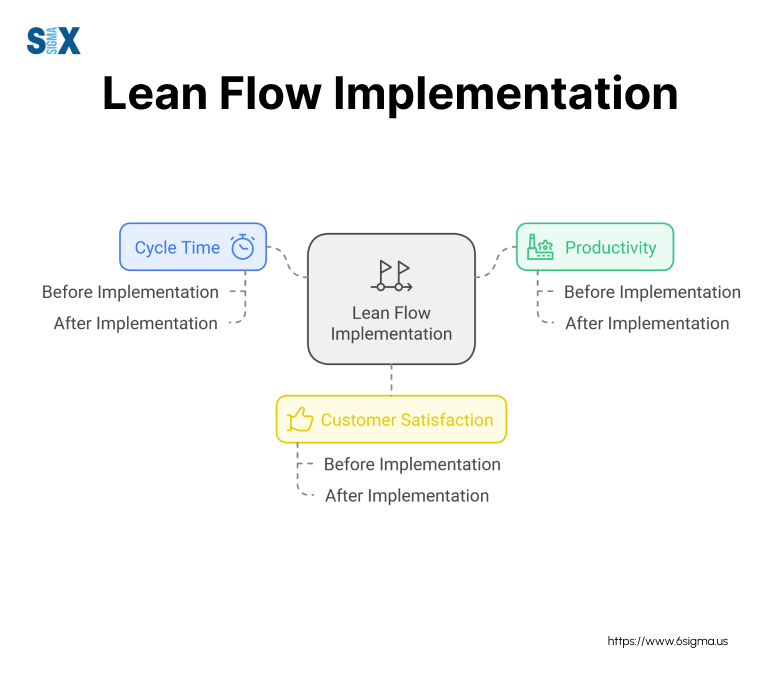
Efficiency and Productivity Gains
One of the primary advantages of adopting lean flow is the remarkable boost in efficiency and productivity.
By optimizing processes and eliminating waste, organizations can achieve impressive results.
Case Study: Manufacturing Success with Lean Flow
A leading automotive parts manufacturer implemented lean flow principles in their production line. By creating a lean flow chart and reorganizing their workspace, they achieved:
- 40% reduction in production lead time
- 35% increase in overall productivity
- 50% decrease in work-in-progress inventory
These improvements not only boosted their output but also significantly enhanced their competitive edge in the market.
Waste Reduction and Cost Savings
Lean flow is fundamentally about eliminating waste, which translates directly into cost savings. The lean flow philosophy identifies several types of waste:
- Overproduction
- Waiting
- Transportation
- Over-processing
- Inventory
- Motion
- Defects
By addressing these areas, companies can realize substantial cost reductions:
- A McKinsey study found that companies implementing lean flow principles achieved cost savings of 15-20% within 12 months.
Example: Service Industry Cost Savings
A large call center implemented lean flow principles to streamline their customer service process:
- They reduced average call handling time by 25%
- Customer wait times decreased by 40%
- Overall operational costs were cut by 18%
These improvements not only saved money but also significantly enhanced customer experience, demonstrating that lean flow is equally effective in service industries as it is in lean flow manufacturing.
Enhanced Quality and Customer Satisfaction
Lean flow doesn’t just make processes faster and more efficient; it also leads to higher quality outputs and increased customer satisfaction. Here’s how:
- Continuous flow reduces the likelihood of defects by identifying and addressing issues immediately.
- Standardized processes ensure consistency in product or service delivery.
- Faster response times and reduced lead times improve customer experience.
A study by the Lean Enterprise Institute found that companies implementing lean flow saw:
- 50% reduction in defect rates
- 25% improvement in customer satisfaction scores
Customer Satisfaction Metrics: Before and After Lean Flow Implementation
A software development company tracked their customer satisfaction metrics before and after implementing lean flow:
Before:
- Customer satisfaction score: 7.2/10
- On-time delivery rate: 68%
- Defect rate: 15%
After (6 months of lean flow):
- Customer satisfaction score: 9.1/10
- On-time delivery rate: 95%
- Defect rate: 3%
These impressive results highlight how lean flow can transform not just internal processes, but also the end-user experience.
The benefits of implementing lean flow are clear and significant.
From boosting efficiency and reducing costs to enhancing quality and customer satisfaction, lean flow principles offer a comprehensive approach to business improvement.
Whether you’re in manufacturing, services, or any other industry, understanding and applying lean flow can be the key to unlocking your organization’s full potential.
Step-by-Step Guide to Implementing Lean Flow
Implementing lean flow in your organization can seem daunting, but with a structured approach, you can successfully transform your processes.
This step-by-step guide will walk you through the key stages of lean flow implementation, ensuring you capture the full benefits of this powerful methodology.
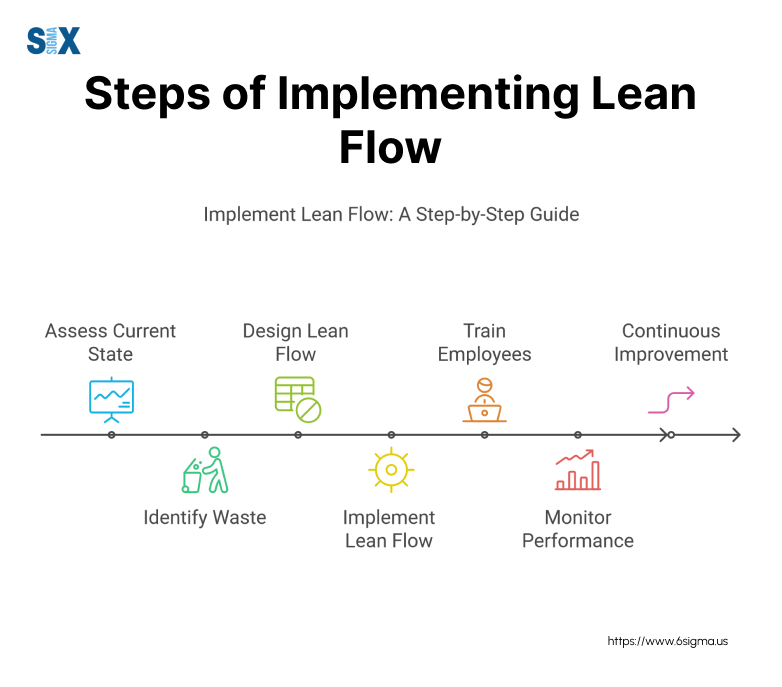
Assessing Your Current Processes
Before diving into lean flow implementation, it’s crucial to understand your current processes thoroughly. This assessment phase sets the foundation for your lean journey:
- Process Mapping: Use tools like value stream mapping to visualize your entire process flow. This helps identify areas where lean flow principles can be applied most effectively.
- Bottleneck Analysis: Employ techniques such as the Theory of Constraints to pinpoint bottlenecks in your system. These are prime targets for lean flow improvements.
- Waste Identification: Conduct a waste walk to identify the eight types of wastes (TIMWOODS) in your processes. This aligns with core lean flow principles and sets the stage for targeted improvements.
Pro Tip: Involve team members from different levels and departments in this assessment. Their diverse perspectives can uncover hidden inefficiencies and opportunities for improvement.
Designing Your Lean Flow System
With a clear understanding of your current state, it’s time to design your lean flow system:
- Create a Lean Flow Chart: Develop a visual representation of your ideal process flow. This lean flow chart should illustrate how work will move smoothly through your system, minimizing waste and maximizing value creation.
- Implement Visual Management: Set up visual management systems like Kanban boards or digital dashboards. These tools make flow visible and help teams quickly identify and address issues.
- Establish Pull Systems: Design pull systems that align with lean flow principles. This ensures that work is only initiated when there’s a downstream demand, preventing overproduction and reducing work-in-progress.
Example: A manufacturing company redesigned their production line based on lean flow principles. By creating a detailed lean flow chart and implementing visual management tools, they reduced lead times by 40% and increased throughput by 25%.
Training Your Team
The success of your lean flow implementation heavily depends on your team’s understanding and buy-in:
- Educate on Lean Flow Philosophy: Conduct workshops to explain what lean flow is and its benefits. This helps build a shared understanding and commitment to the new approach.
- Hands-on Training: Use simulation exercises to demonstrate lean flow principles in action. This practical approach helps team members internalize the concepts.
- Address Resistance: Be prepared for resistance to change. Use change management techniques to address concerns and highlight the benefits of lean flow for individual team members and the organization as a whole.
Case Study: A software development firm struggled with initial resistance to lean flow adoption. By implementing a comprehensive training program that included both theoretical and practical elements, they achieved a 90% buy-in rate within three months, leading to a 30% increase in project delivery speed.
Continuous Improvement and Monitoring
Lean flow is not a one-time implementation but an ongoing journey of improvement:
- Establish KPIs: Define key performance indicators that align with lean flow objectives. These might include cycle time, lead time, work-in-progress levels, and quality metrics.
- Regular Review Process: Implement daily stand-up meetings and weekly review sessions to monitor progress and address issues promptly.
- Kaizen Events: Organize regular kaizen events focused on specific aspects of your lean flow system. These concentrated improvement efforts can lead to significant breakthroughs.
- Adapt and Evolve: As your team becomes more proficient in lean flow, continuously refine your processes. Be open to adjusting your lean flow chart and systems based on new insights and changing business needs.
Remember, the essence of lean flow is continuous improvement.
By following this step-by-step guide and maintaining a commitment to ongoing refinement, you can unlock the full potential of lean flow in your organization.
Whether you’re in manufacturing, services, or knowledge work, these principles can dramatically enhance your operational efficiency and effectiveness.
Take your lean implementation skills to the next level. Our Green Belt course equips you with advanced tools and strategies to drive significant, lasting improvements in your organization.
Overcoming Common Barriers to Lean Flow
While the benefits of lean flow are clear, implementing this methodology often comes with challenges. Understanding and addressing these barriers is crucial for successful lean flow adoption.
Let’s explore some common obstacles and strategies to overcome them.
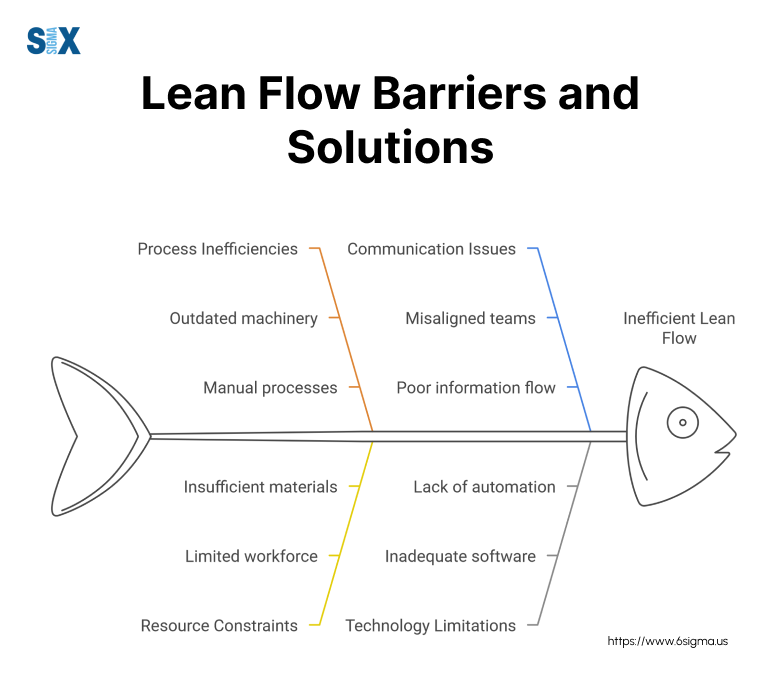
Organizational Resistance
One of the most significant hurdles in implementing lean flow is resistance from within the organization. This resistance can stem from fear of change, lack of understanding, or perceived threats to job security.
Strategies for gaining buy-in:
- Education: Conduct workshops explaining lean flow meaning and its benefits to all levels of the organization.
- Involvement: Include employees in the lean flow planning process to foster ownership.
- Clear Communication: Regularly share the vision and progress of lean flow implementation.
- Quick Wins: Start with small, visible improvements to demonstrate the value of lean flow principles.
Case Study: Tech Company Overcomes Resistance
A mid-sized software company faced initial pushback when introducing lean flow. They overcame this by:
- Organizing “Lean Flow Days” where teams could experiment with lean techniques in a low-stakes environment.
- Appointing “Lean Champions” from various departments to advocate for and support the transition.
- Implementing a suggestion system that rewarded employees for lean flow improvement ideas.
Result: Within six months, employee engagement in lean flow initiatives increased by 70%, leading to a 25% reduction in project delivery times.
Resource Constraints
Many organizations hesitate to implement lean flow due to perceived high costs or lack of resources. However, lean flow can be adapted to work within existing constraints.
Creative solutions on a budget:
- Start Small: Begin with pilot projects in key areas rather than company-wide implementation.
- Leverage Free Tools: Utilize open-source software for creating lean flow charts and tracking metrics.
- Cross-functional Teams: Form teams from different departments to pool knowledge and resources.
- Virtual Training: Use online resources and webinars for lean flow training instead of expensive in-person sessions.
Tip: Remember, the lean flow philosophy itself is about doing more with less. Apply this principle to your implementation strategy as well.
Complexity in Processes
Complex processes can make lean flow implementation seem daunting. However, lean flow principles are particularly effective in simplifying and streamlining complex workflows.
Breaking down complex processes:
- Value Stream Mapping: Use this tool to visualize and understand complex processes.
- Process Chunking: Break large processes into smaller, manageable segments for lean flow application.
- Standardization: Create standard operating procedures to reduce variability in complex tasks.
- Automation: Identify repetitive, complex tasks that can be automated to improve flow.
Tools and techniques for simplification:
- 5S Methodology: Organize workspaces for efficiency and eliminate unnecessary steps.
- Kanban Boards: Visualize workflow and identify bottlenecks in complex processes.
- SMED (Single-Minute Exchange of Die): Reduce setup times in manufacturing processes.
Example: A healthcare provider simplified their patient intake process using lean flow principles.
By creating a detailed lean flow chart and eliminating redundant steps, they reduced patient wait times by 40% and increased staff productivity by 30%.
While barriers to lean flow implementation are common, they are far from insurmountable.
By addressing organizational resistance, working creatively within resource constraints, and tackling process complexity head-on, organizations can successfully transition to a lean flow model.
Remember, the journey to lean flow is itself a process of continuous improvement. Each challenge overcome is a step towards a more efficient, productive, and competitive organization.
Struggling with lean implementation? Our Lean Fundamentals course provides practical solutions to common challenges and deepens your understanding of lean principles.
Measuring Success: Lean Flow Metrics and KPIs
To truly use the power of lean flow, it’s essential to measure its impact accurately.
By tracking the right metrics and Key Performance Indicators (KPIs), you can quantify improvements, identify areas for further optimization, and demonstrate the value of lean flow to stakeholders.
Essential Lean Flow Metrics
To gauge the success of your lean flow implementation, focus on these key metrics:
- Cycle Time: The time it takes to complete one unit of work from start to finish.
- Lead Time: The total time from customer order to delivery.
- Throughput: The number of units processed per time period.
- Work in Progress (WIP): The amount of work currently in the system.
- Quality Metrics: Defect rates, rework percentages, and first-pass yield.
- Customer Satisfaction Scores: Net Promoter Score (NPS) or Customer Satisfaction Index (CSI).
These metrics align closely with lean flow principles and provide a comprehensive view of your process efficiency and effectiveness.
Implementing a Measurement System
To effectively track these metrics, you need a robust measurement system:
- Set up Visual Dashboards: Create lean flow charts and digital dashboards that display real-time metrics. This visibility helps teams quickly identify issues and opportunities for improvement.
- Use Reporting Tools: Implement software tools that can automatically collect and analyze data. Many lean management software options integrate with existing systems to streamline this process.
- Establish Regular Review Processes: Schedule daily stand-ups, weekly reviews, and monthly deep dives to analyze trends and discuss improvements.
- Train Teams on Metrics: Ensure all team members understand what each metric means and how their work impacts these numbers.
Using Data to Drive Continuous Improvement
Collecting data is just the first step. The real value comes from using this information to drive continuous improvement:
- Identify Patterns: Look for trends and correlations in your metrics. For example, how does reducing WIP impact lead times?
- Set Improvement Targets: Use current data as a baseline to set realistic improvement goals.
- Conduct Root Cause Analysis: When metrics indicate a problem, use techniques like the ‘5 Whys‘ to identify the root cause.
- Implement and Test Solutions: Use data to validate the effectiveness of process changes.
Case Study: Data-Driven Improvements in Healthcare
A hospital emergency department implemented lean flow principles and a robust measurement system.
By closely tracking cycle times and patient satisfaction scores, they identified that long wait times for lab results were a major bottleneck.
Actions taken:
- Streamlined the lab testing process
- Implemented a rapid results system for common tests
- Trained staff on new procedures
Results:
- 40% reduction in average patient cycle time
- 25% increase in patient satisfaction scores
- 15% increase in department throughput
This case demonstrates how leveraging lean flow metrics can lead to significant, measurable improvements in even complex environments like healthcare.
Conclusion
Throughout this article, we’ve explored the fundamental concepts of lean flow, from its definition and principles to practical implementation strategies and measurement techniques.
We’ve seen how lean flow can transform organizations across various industries, leading to increased efficiency, reduced waste, and improved customer satisfaction.
The lean flow philosophy, with its focus on continuous improvement and respect for people, provides a powerful framework for organizations looking to thrive.
Implementing lean flow is not without its challenges, but with the right approach, tools, and metrics, these obstacles can be overcome.
The key is to start small, measure consistently, and continuously refine your processes based on data and feedback.
The path to greater efficiency and success begins with that first step towards lean thinking.
SixSigma.us offers both Live Virtual classes as well as Online Self-Paced training. Most option includes access to the same great Master Black Belt instructors that teach our World Class in-person sessions. Sign-up today!
Virtual Classroom Training Programs Self-Paced Online Training Programs