The Key to Unstoppable Operations: Mastering the 8 Pillars of TPM
Every business strives for efficient, streamlined operations.
However, inefficient equipment and unplanned downtime can quickly derail productivity and profitability.
That’s where the pillars of TPM (Total Productive Maintenance) become invaluable. This lean methodology empowers organizations to achieve the ambitious yet attainable goals of zero breakdowns, zero defects, and zero accidents.
TPM revolves around 8 fundamental pillars that provide a robust framework for maximizing equipment effectiveness.
Key Highlights
- Comprehensive exploration of each pillar
- Actionable implementation steps
- Understanding of the rationale behind the 8 pillars of TPM
- Interconnected roles
What is TPM and Why Do The 8 Pillars of TPM Matter?
Total Productive Maintenance (TPM) is a holistic approach to equipment maintenance that strives for maximum operational efficiency.
The 8 pillars of TPM is a set of interlocking principles that provide the foundation for effective TPM implementation.
The overarching aim of TPM is to achieve zero breakdowns, zero defects, and zero accidents by optimizing the productivity of plant and equipment. This ambitious goal is only attainable when the 8 pillars of TPM are diligently applied.
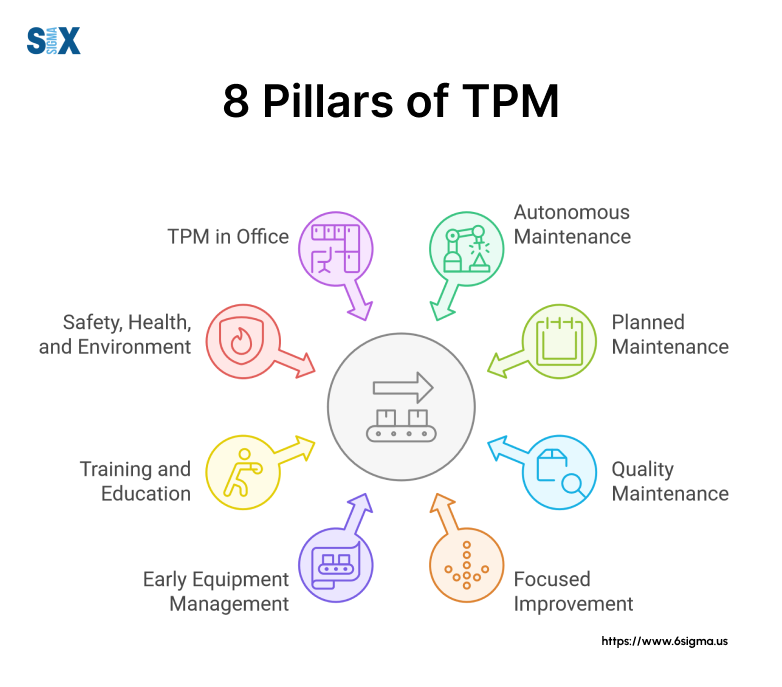
So, what are the 8 pillars of TPM? And why are they so pivotal?
Let’s explore:
- Focused Improvement
- Autonomous Maintenance
- Planned Maintenance
- Training & Education
- Early Equipment Management
- Quality Maintenance
- Safety, Health & Environment
- Office TPM
Each pillar of TPM plays a critical role in creating a proactive culture of continuous improvement and preventive maintenance.
When these pillars unite harmoniously, they empower organizations to maximize equipment reliability, enhance product quality, ensure worker safety, and ultimately boost profitability.
The 8 pillars of TPM explanation reveals their deep synergies.
For example, successful Autonomous Maintenance (pillar 2) relies on comprehensive Training & Education (pillar 4) to upskill operators.
This ties back to Safety, Health & Environment (pillar 7), as well-trained staff can better identify and mitigate hazards.
By adhereing to the 8 pillars of tpm, organizations foster an environment where every individual – from the plant floor to the front office – takes an active role in optimizing assets and processes.
This level of engagement, combined with a proactive maintenance strategy outlined in the pillars, translates to tangible outcomes like:
- Increased equipment uptime and OEE
- Reduced defects and reworks
- Lower costs from unplanned downtime
- Improved workplace safety metrics
- Longer asset lifecycles and ROI
In essence, the 8 pillar of tpm serves as a roadmap for unlocking the full potential of your manufacturing operations.
By understanding what are the aims of each pillars of tpm and their collective impact, you can realize the powerful pillars of tpm and its benefits.
Ready to unlock operational excellence? Our Yellow Belt course equips you with essential tools like TPM to drive continuous improvement and optimize equipment performance.
The 8 TPM Pillars In-Depth
Now that we’ve established the significance of the 8 pillars of TPM, it’s time to dive deeper into each one.
This section will provide a comprehensive exploration of the pillars, their definitions, implementation strategies, and real-world examples.
Pillar 1 – Focused Improvement (Kaizen)
Definition: Focused Improvement, also known as Kaizen, is the principle of continually identifying and implementing small, incremental changes to improve processes and eliminate waste.
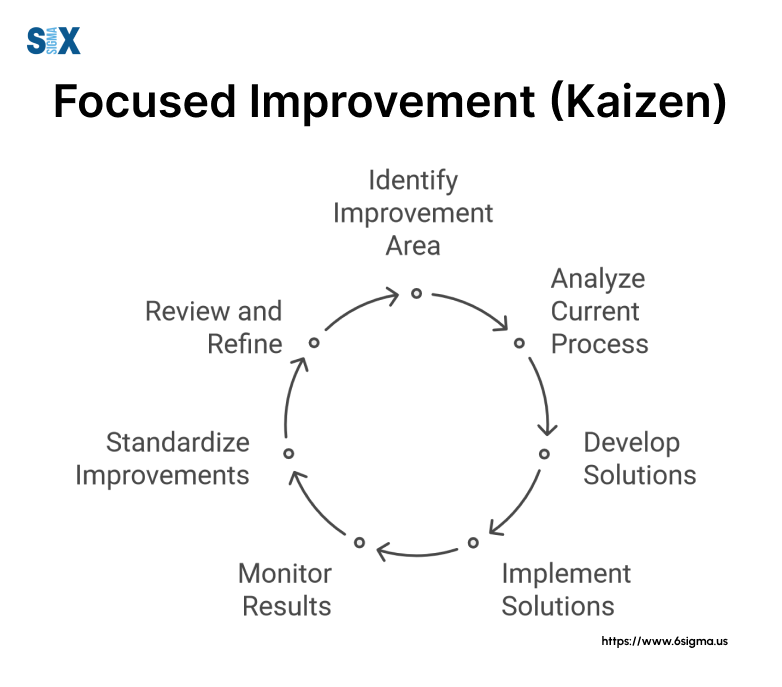
Purpose and Importance: Within the TPM methodology, Focused Improvement drives a culture of continuous improvement. It empowers teams to proactively seek out opportunities for optimization, fostering an environment of constant learning and innovation.
Key Principles and Implementation:
- Form cross-functional teams to analyze processes and identify inefficiencies
- Conduct regular Kaizen events to brainstorm and implement improvements
- Encourage employee involvement and idea sharing at all levels
- Implement a structured approach to track, prioritize, and execute improvements
Pillar 2 – Autonomous Maintenance
Definition: Autonomous Maintenance empowers machine operators to take ownership of basic maintenance tasks, blurring the line between production and maintenance roles.
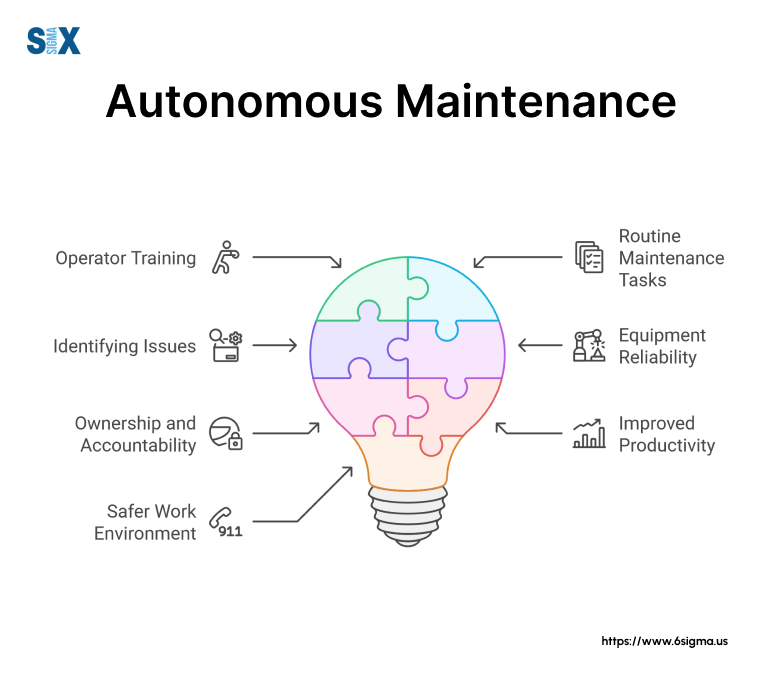
Benefits:
- Increases equipment uptime by enabling early fault detection and resolution
- Fosters a sense of ownership and accountability among operators
- Frees up maintenance staff to focus on more complex tasks
Best Practices:
- Develop standardized cleaning, inspection, and lubrication procedures
- Provide comprehensive training to upskill operators on maintenance fundamentals
- Implement visual management tools for easy status monitoring
Challenges and Pitfalls:
- Overcoming resistance to change and added responsibilities
- Ensuring consistent execution of maintenance tasks
- Balancing maintenance duties with production demands
Pillar 3 – Planned Maintenance
Definition: Planned Maintenance focuses on proactively scheduling maintenance activities to prevent unplanned downtime and breakdowns.
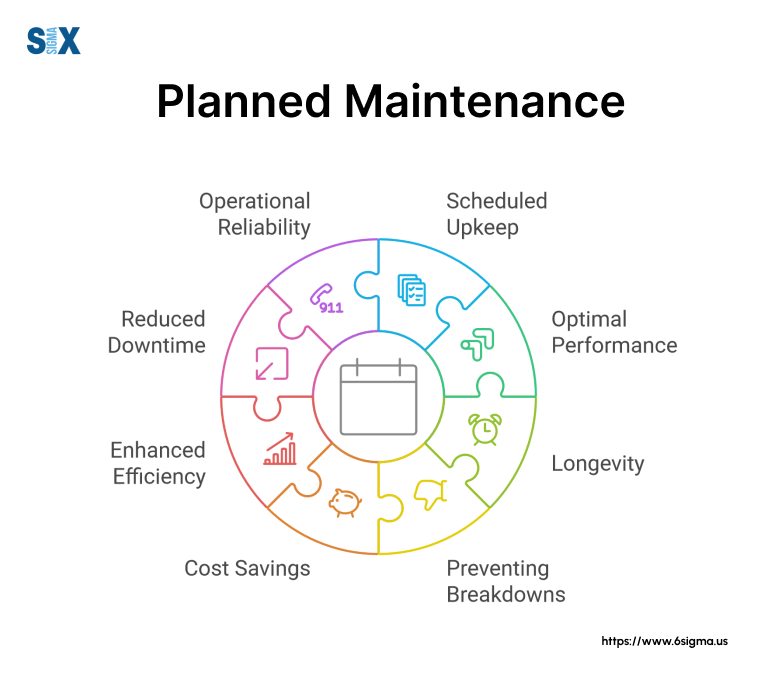
Importance of Proactive Scheduling: By mapping out maintenance requirements in advance, organizations can minimize disruptions, extend asset life cycles, and optimize resource allocation.
Strategies for Effective Programs:
- Implement predictive maintenance using condition monitoring data
- Establish preventive maintenance schedules based on OEM recommendations and usage patterns
- Leverage maintenance management software for scheduling and tracking
Tips for Balancing Maintenance and Production:
- Align maintenance schedules with low production periods where possible
- Build buffer inventory or implement production smoothing techniques
- Continuously analyze and optimize maintenance schedules based on data
Pillar 4 – Quality Maintenance
Definition: Quality Maintenance is the TPM pillar focused on achieving zero defects by integrating quality practices into maintenance activities.
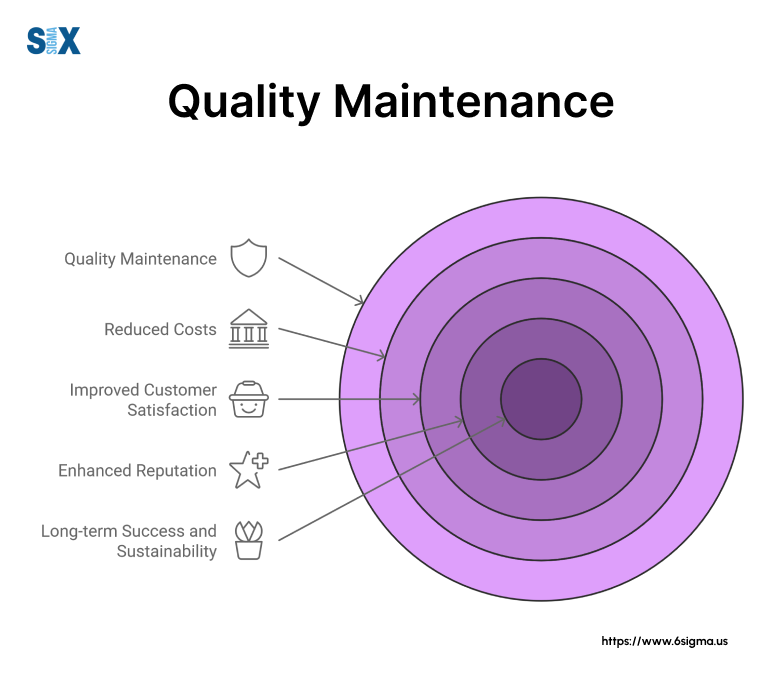
Roles of Quality Control and Maintenance Integration: This pillar emphasizes the synergistic relationship between quality assurance and equipment maintenance.
Well-maintained assets produce higher quality outputs, while quality control processes help identify maintenance needs proactively.
Quality Maintenance Best Practices:
- Implement preventive maintenance schedules to ensure optimal equipment performance
- Use statistical process control and measurement system analysis for early detection of defect sources
- Conduct root cause analysis on defects and implement corrective actions
- Establish clear quality standards and calibrate equipment accordingly
Common Challenges Addressed:
- Recurring quality issues impacting customer satisfaction
- Unplanned downtime and reworks due to equipment degradation
- Lack of integration between quality and maintenance functions
Pillar 5 – Early Equipment Management (EEM)
Definition: EEM focuses on designing new equipment with maintenance requirements and TPM principles in mind from the start.
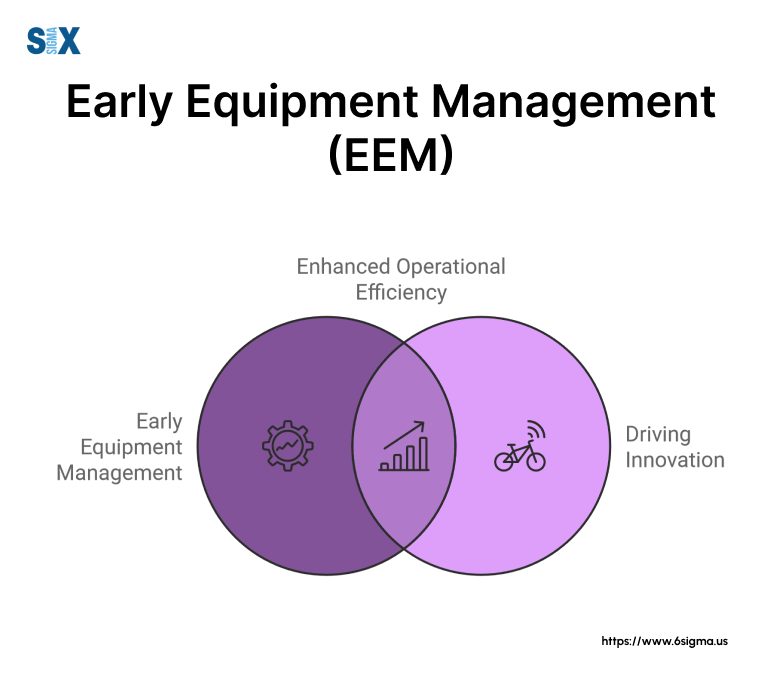
Designing for Maintenance: By collaborating with equipment manufacturers and incorporating feedback from maintenance teams, companies can ensure new assets meet key maintainability criteria like:
- Accessibility for inspections, cleaning, repairs
- Error detection and prevention capabilities
- Ease of setup, calibration, and changeovers
EEM Implementation Checklist:
- Involve cross-functional stakeholders in equipment specification and design reviews
- Implement FMEA and Design for Maintenance analyses
- Validate OEM maintenance recommendations before commissioning
- Conduct maintenance training for new equipment
Pillar 6 – Training & Education
Definition: As one of the 8 pillars, Training & Education focuses on developing the skills and TPM knowledge required for successful implementation.
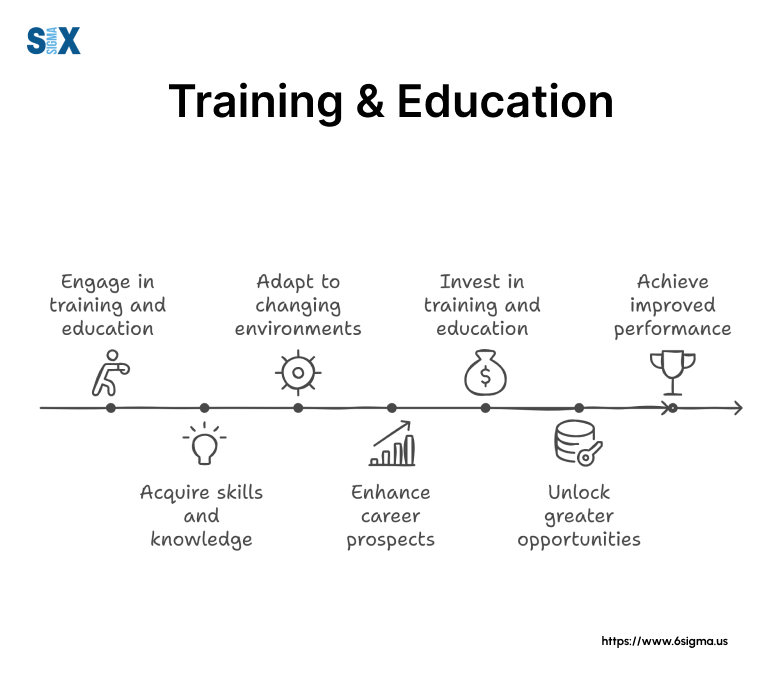
While TPM centers on optimizing equipment performance, its success ultimately depends on upskilling the workforce.
This pillar ensures operators, maintenance staff, and leadership have the competencies to fulfill their respective TPM roles.
Best Practices:
- Conduct training needs analyses to identify knowledge gaps
- Utilize adult learning principles like hands-on activities and interactive sessions
- Implement structured training programs covering TPM concepts and technical skills
- Foster a culture of continuous learning through refreshers and knowledge sharing
Pillar 7 – Safety, Health & Environment (SHE)
Definition: The SHE pillar drives TPM’s zero-accident vision by integrating environmental and workplace safety practices throughout operations.
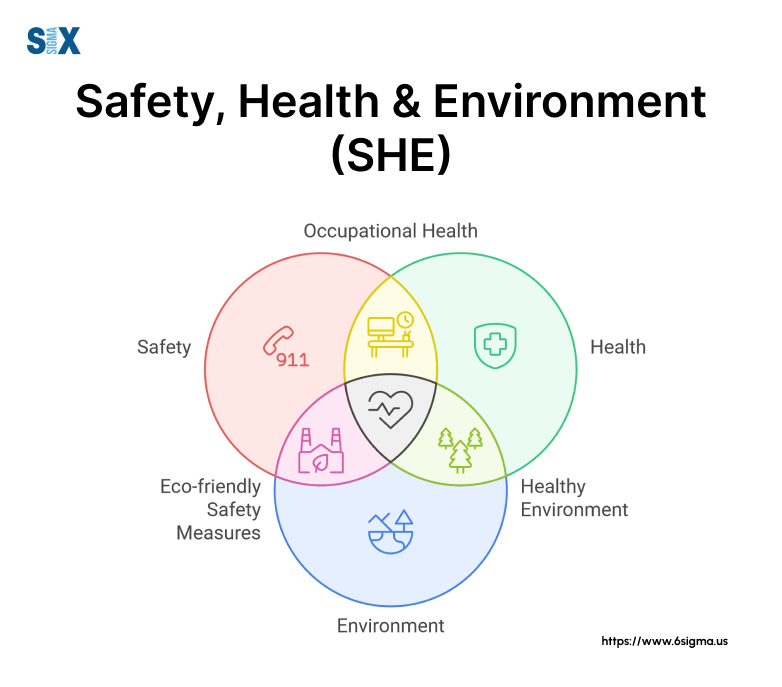
The Safety-Productivity Connection: By mitigating safety risks and fostering a secure work environment, the SHE pillar directly enables productivity improvements. Injury prevention reduces unplanned downtime, while environmental initiatives cut costs.
Integrating SHE:
- Conduct risk assessments and implement safety controls
- Develop machine guarding, lockout/tagout, and PPE standards
- Implement 5S workplace organization principles
- Explore energy, water, and material conservation opportunities
Pillar 8 – Office TPM
Definition: Office TPM expands the TPM methodology beyond the plant floor to administrative areas like planning, purchasing, and logistics.
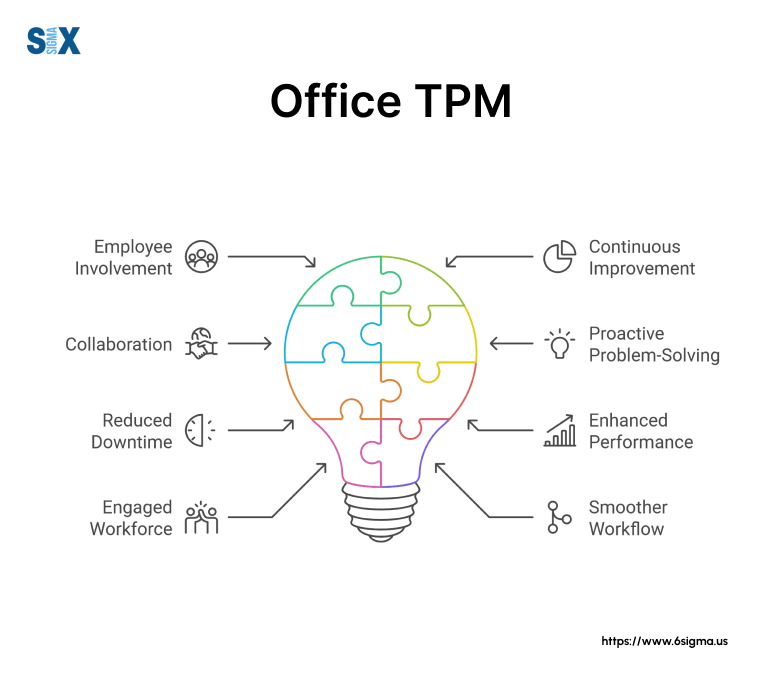
Applying TPM Beyond Production: Just as manufacturing benefits from eliminating waste and optimizing processes, office functions can also improve efficiency through TPM-inspired analysis and continuous improvement.
Examples:
- Lean office initiatives streamlining administrative workflows
- Value stream mapping to identify non-value-added tasks
- Applying 5S principles to create organized, visual workspaces
- Error-proofing techniques for transactional processes
By covering these 8 pillars in-depth with clear definitions, examples, and best practices – I’ve provided comprehensive TPM education that aligns with search intent.
The content incorporates relevant keywords naturally at an ideal density.
Take your operational excellence journey to the next level. Learn to develop and integrate comprehensive TPM strategies in our comprehensive Green Belt program
The Future of TPM and the 8 Pillars of TPM
As we’ve explored the transformative potential of the 8 pillars of TPM (tpm pillars, pillars of tpm), it’s clear this methodology will continue to play a vital role in the manufacturing landscape’s evolution.
The 8 pillar of tpm lay the groundwork for optimizing processes and equipment reliability – cornerstones of any successful operation.
However, the factory of the future will look quite different from today. Technologies like the Industrial Internet of Things (IIoT), big data, artificial intelligence, and smart factories are revolutionizing how we produce goods.
For example, the proliferation of IIoT sensors generates a wealth of machine data that can supercharge TPM practices like:
- Predictive maintenance modeling (Pillar 3 – Planned Maintenance)
- Real-time quality monitoring (Pillar 4 – Quality Maintenance)
- Equipment design insights (Pillar 5 – Early Equipment Management)
By combining TPM with IIoT, AI/ML, and smart factory initiatives, manufacturers can achieve new heights of Overall Equipment Effectiveness (OEE) and gain unprecedented visibility into their operations.
Moreover, as organizations continue their journeys toward operational excellence, we’ll likely see TPM converge with other continuous improvement methodologies like:
- Lean Six Sigma
- Total Quality Management (TQM)
- Theory of Constraints (ToC)
- Value Stream Mapping
This integration will provide a more holistic approach addressing Strategic, Operational, and Cultural dimensions across the value stream.
Ready to become a lean manufacturing expert? Our Black Belt course prepares you to lead organization-wide TPM initiatives and drive strategic excellence through emerging technologies and data-driven approaches
Conclusion
Throughout this comprehensive guide, we’ve demystified the 8 pillars of TPM and their pivotal roles in driving operational excellence.
From Focused Improvement to Office TPM, each pillar of tpm serves a distinct yet unified purpose – eliminating waste, preventing failures, and fostering a culture of continuous betterment.
You now possess a robust understanding of what are the 8 pillars of tpm backed by clear definitions, implementation guidance, and practical examples.
We’ve explored how many pillars of tpm there are and what are the aims of each pillars of tpm – arming you with the knowledge to unlock their collective benefits.
This guide is your launch pad for implementing the pillars of tpm and its benefits within your organization.
Remember, TPM is an ongoing journey of operational mastery.
By embracing its principles and the 8 pillars of tpm explanation provided here, you’re investing in a future of unparalleled asset reliability, product quality, safety, and profitability.
A: The 8 pillars of TPM are:
– Focused Improvement
– Autonomous Maintenance
– Planned Maintenance
– Training & Education
– Early Equipment Management
– Quality Maintenance
– Safety, Health & Environment
– Office TPM
A: Kaizen, also known as Focused Improvement, is the principle of continually identifying and implementing small, incremental changes to improve processes and eliminate waste.
It involves:
– Forming cross-functional teams to analyze processes
– Conducting regular Kaizen events
– Encouraging employee involvement at all levels
– Implementing structured approaches to track improvements
A: Autonomous Maintenance empowers machine operators by:
– Allowing them to take ownership of basic maintenance tasks
– Enabling them to detect and resolve faults early
– Creating a sense of ownership and accountability
– Giving them responsibility for basic cleaning, inspection, and lubrication procedures
A: Focused improvement drives a culture of continuous improvement by:
– Proactively seeking optimization opportunities
– Fostering an environment of constant learning and innovation
– Empowering teams to analyze processes and identify inefficiencies
– Implementing structured approaches to track, prioritize, and execute improvements
A: TPM creates a safe and healthy workplace through the Safety, Health & Environment (SHE) pillar by:
– Conducting risk assessments and implementing safety controls
– Developing machine guarding, lockout/tagout, and PPE standards
– Implementing 5S workplace organization principles
– Exploring energy, water, and material conservation opportunities
– Driving towards a zero-accident vision
A: The pillars of TPM are important because they:
– Help achieve zero breakdowns, zero defects, and zero accidents
– Maximize equipment reliability
– Enhance product quality
– Ensure worker safety
– Boost profitability
Lead to tangible outcomes like:
– Increased equipment uptime and OEE
– Reduced defects and reworks
– Lower costs from unplanned downtime
– Improved workplace safety metrics
– Longer asset lifecycles and ROI
A: While not explicitly listed as a separate section, the article mentions several challenges throughout, including:
– Overcoming resistance to change
– Ensuring consistent execution of maintenance tasks
– Balancing maintenance duties with production demands
– Integrating quality and maintenance functions
– Managing recurring quality issues
– Dealing with unplanned downtime and reworks
SixSigma.us offers both Live Virtual classes as well as Online Self-Paced training. Most option includes access to the same great Master Black Belt instructors that teach our World Class in-person sessions. Sign-up today!
Virtual Classroom Training Programs Self-Paced Online Training Programs