Quality Assurance vs Quality Control: A Comprehensive Comparison
While often used interchangeably, quality assurance vs quality control serve distinct yet complementary roles in ensuring excellence.
Afterall, delivering high-quality products and services is paramount to success.
Key Highlights
- Quality Management Systems: Foundation for excellence
- QA: Process-oriented, proactive approach to quality
- QC: Product-focused, reactive measures for defect detection
- Prevention vs. Detection: Core difference between QA and QC
- Integration of QA and QC for comprehensive quality management
- Best practices: SOPs, audits, and continuous improvement
What is Quality Management?
Quality management is the cornerstone of successful businesses.
It encompasses a range of practices and methodologies aimed at ensuring consistent excellence in products and services.
Defining Quality in Manufacturing and Services
Quality in manufacturing and services is not just about meeting specifications; it’s about exceeding customer expectations.
It involves creating products and delivering services that are reliable, durable, and provide value to the end-user.
In manufacturing, quality might mean precision in measurements and consistency in output. For services, it often translates to reliability, responsiveness, and customer satisfaction.
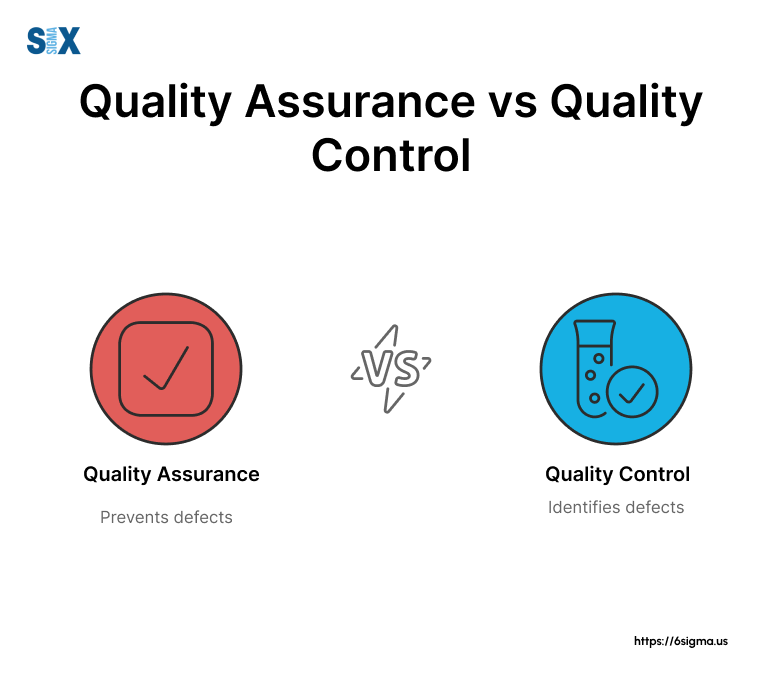
The Role of Quality Management Systems (QMS)
A Quality Management System (QMS) is the backbone of an organization’s quality efforts.
It’s a formalized system that documents processes, procedures, and responsibilities for achieving quality policies and objectives.
A well-implemented QMS helps coordinate and direct an organization’s activities to meet customer and regulatory requirements and improve its effectiveness and efficiency on a continuous basis.
Understanding Quality Assurance (QA)
Quality Assurance is a proactive approach to preventing defects and ensuring that quality standards are consistently met.
It focuses on the processes that lead to the final product or service.
Core Principles of Quality Assurance
The core principles of QA include:
- Prevention over detection
- Continuous improvement
- Fact-based decision making
- Process focus
- Customer-centric approach
These principles guide organizations in establishing robust quality processes that minimize the defects occurring in the first place.
Process-Oriented Approach
QA adopts a process-oriented approach, focusing on the entire production or service delivery system rather than just the end result.
This involves mapping out processes, identifying potential weak points, and implementing measures to strengthen these areas.
By doing so, QA aims to create a system where quality is built into every step of the process.
Proactive Strategies for Quality Planning
Proactive quality planning is a key aspect of QA.
This involves:
- Developing comprehensive quality plans
- Setting clear quality objectives
- Identifying potential risks and mitigation strategies
- Establishing quality metrics and measurement systems
These strategies help organizations anticipate and address quality issues before they arise, saving time, resources, and maintaining customer trust.
For teams seeking structured frameworks, our Six Sigma Green Belt certification program provides methodologies for risk identification and mitigation.
ISO Standards and Their Importance in QA
ISO standards, particularly ISO 9001, play a crucial role in QA.
These internationally recognized standards provide a framework for implementing and maintaining effective quality management systems.
Adhering to ISO standards not only ensures consistency in quality practices but also enhances an organization’s credibility and competitiveness in the global market.
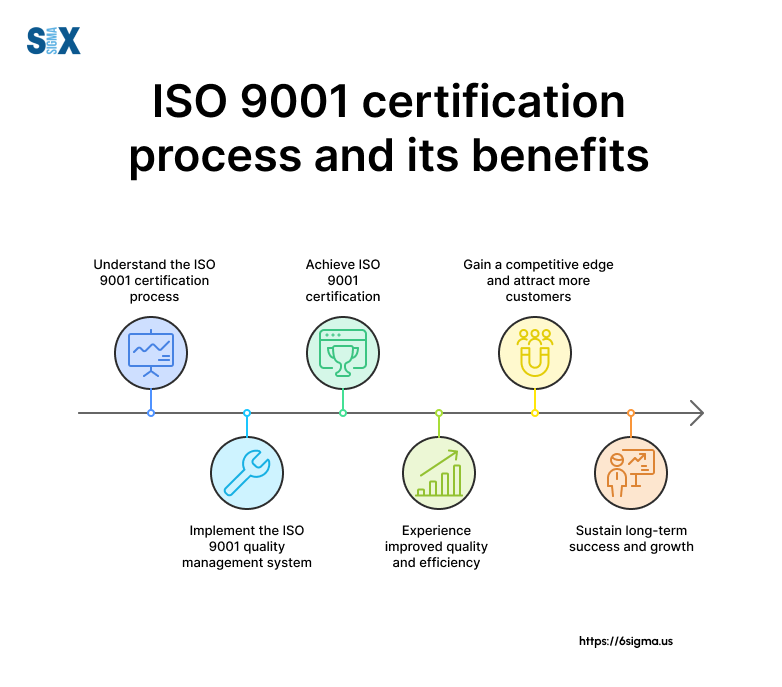
Exploring Quality Control (QC)
Quality Control is a reactive process that focuses on identifying and correcting defects in the final product or service.
It serves as the last line of defense in ensuring that only quality products reach the customer.
Fundamentals of Quality Control
The fundamentals of QC include:
- Inspection and testing
- Statistical sampling
- Defect identification and classification
- Corrective action implementation
- Documentation and reporting
These elements work together to ensure that products or services meet predetermined quality standards before they are delivered to customers.
Product-Oriented Focus
Unlike QA’s process focus, QC is product-oriented. It involves thorough inspection and testing of the final product or service to ensure it meets specified requirements.
This might include dimensional checks in manufacturing, functionality tests in software development, or customer feedback analysis in service industries.
Reactive Measures in Quality Management
QC is inherently reactive, dealing with issues as they are discovered.
When a defect is found, QC processes trigger corrective actions to address the immediate problem and prevent similar issues in future production.
While this approach can be effective in catching defects, it can also be more costly and time-consuming than preventive QA measures.
Statistical Process Control (SPC) in QC
Statistical Process Control is a powerful tool in QC.
It uses statistical methods to monitor and control a process, ensuring it operates at its full potential.
SPC helps in:
- Reducing variability in processes
- Predicting process performance
- Identifying out-of-control situations early
- Providing data-driven insights for continuous improvement
Quality Assurance vs Quality Control: Key Differences
While QA and QC are both integral to quality management, they differ significantly in their approach, timing, and focus.
Understanding these differences is crucial for effective implementation of quality strategies.
Prevention vs Detection Methods b/w Quality Assurance vs Quality Control
The primary distinction between Quality Assurance vs Quality Control lies in their fundamental approach:
- QA focuses on prevention, aiming to stop defects from occurring.
- QC emphasizes detection, identifying defects after they’ve happened.
This difference in approach significantly impacts the overall efficiency and cost-effectiveness of quality management efforts.
Timing in the Product Lifecycle
The timing of QA and QC activities in the product lifecycle is another key differentiator:
- QA is implemented throughout the entire process, from planning to execution.
- QC typically occurs at the end of the production process or at predetermined checkpoints.
This timing difference affects how and when quality issues are addressed, influencing the overall efficiency of the quality management process.
Scope of Involvement: Team-wide vs Dedicated Personnel
The scope of involvement varies between QA and QC:
- QA involves the entire organization, fostering a culture of quality across all departments.
- QC is often the responsibility of a dedicated team or department focused on inspection and testing.
This difference in scope impacts how quality is perceived and managed within the organization.
Cost Implications: Long-term vs Immediate
The cost implications of QA and QC differ:
- QA involves higher upfront costs but can lead to long-term savings through defect prevention.
- QC may have lower initial costs but can result in higher long-term expenses due to rework and waste.
Understanding these cost dynamics is crucial for making informed decisions about quality management investments.
Aspect | Quality Assurance (QA) | Quality Control (QC) |
---|---|---|
Approach | Proactive, Prevention-focused | Reactive, Detection-focused |
Timing | Throughout entire process | End of process or checkpoints |
Focus | Process-oriented | Product-oriented |
Involvement | Organization-wide | Dedicated team or department |
Cost Implication | Higher upfront, long-term savings | Lower initial, potential long-term costs |
Learn detailed explanation of QA and QC differences with our Lean Six Sigma Green Belt Certification
Integrating QA and QC for Comprehensive Quality Management
While QA and QC have distinct roles, their integration is crucial for a holistic approach to quality management.
This synergy ensures that quality is embedded throughout the product lifecycle.
Synergies Between QA and QC
The integration of QA and QC creates powerful synergies:
- QA processes inform QC activities, providing a framework for what to inspect and test.
- QC results feed back into QA processes, highlighting areas for improvement in the overall system.
- Together, they create a closed-loop system that drives continuous improvement.
This synergistic relationship enhances the overall effectiveness of quality management efforts.
Implementing Corrective and Preventive Actions (CAPA)
CAPA is a critical component that bridges QA and QC:
- Corrective actions address immediate issues identified through QC.
- Preventive actions, informed by QC findings, are implemented through QA processes to prevent recurrence.
A well-implemented CAPA system ensures that lessons learned from QC are systematically applied to improve overall quality.
Continuous Improvement Strategies
Continuous improvement is at the heart of integrated quality management:
- QA sets the stage for improvement by establishing processes and metrics.
- QC provides the data and insights needed to drive improvement efforts.
- Together, they create a cycle of ongoing enhancement in product quality and process efficiency.
Strategies like Kaizen, PDCA (Plan-Do-Check-Act) cycles, and Six Sigma methodologies can be effectively applied in this integrated approach.
Total Quality Management (TQM) and Six Sigma Approaches
TQM and Six Sigma represent comprehensive approaches that integrate QA and QC principles:
- TQM emphasizes organization-wide commitment to quality and customer satisfaction.
- Six Sigma focuses on reducing variability and defects through data-driven methods.
These approaches provide frameworks for organizations to leverage the strengths of both QA and QC in pursuit of excellence.
See the discussion of QA and QC integration and advanced methodologies in your process with our Lean Six Sigma Black Belt Certification
Best Practices in Quality Assurance and Quality Control
Implementing best practices in QA and QC is crucial for maximizing the effectiveness of quality management efforts.
These practices ensure that quality initiatives are well-structured, data-driven, and continuously improving.
Developing Effective Standard Operating Procedures (SOPs)
SOPs are the backbone of consistent quality management:
- They provide clear, step-by-step instructions for critical processes.
- SOPs ensure uniformity in operations, reducing variability and errors.
- Regular review and updating of SOPs are crucial to maintain their relevance and effectiveness.
Well-crafted SOPs bridge the gap between QA planning and QC execution, ensuring that quality standards are consistently met.
Conducting Quality Audits and Root Cause Analysis
Regular audits and root cause analysis are essential for maintaining and improving quality:
- Internal audits help identify gaps in processes and compliance.
- External audits provide an objective assessment of quality systems.
- Root cause analysis delves deep into issues to address underlying causes rather than symptoms.
These practices provide valuable insights for both QA process improvement and QC effectiveness.
Training and Skill Development for Quality Teams
Continuous training and skill development are critical for quality teams:
- Regular training ensures teams are up-to-date with the latest quality management techniques.
- Cross-training between QA and QC teams promotes better understanding and collaboration.
- Skill development in areas like statistical analysis and problem-solving enhances overall quality management capabilities, and our six sigma certification programs equips you with just that.
Investing in human capital is key to building a robust quality culture within the organization.
Leveraging Quality Tools and Technologies
Modern quality management leverages a range of tools and technologies:
- Quality management software for tracking, reporting, and analysis.
- Advanced statistical tools for process control and improvement.
- Automation and AI for enhancing inspection accuracy and efficiency.
These tools support both QA and QC efforts, making quality management more data-driven and effective.
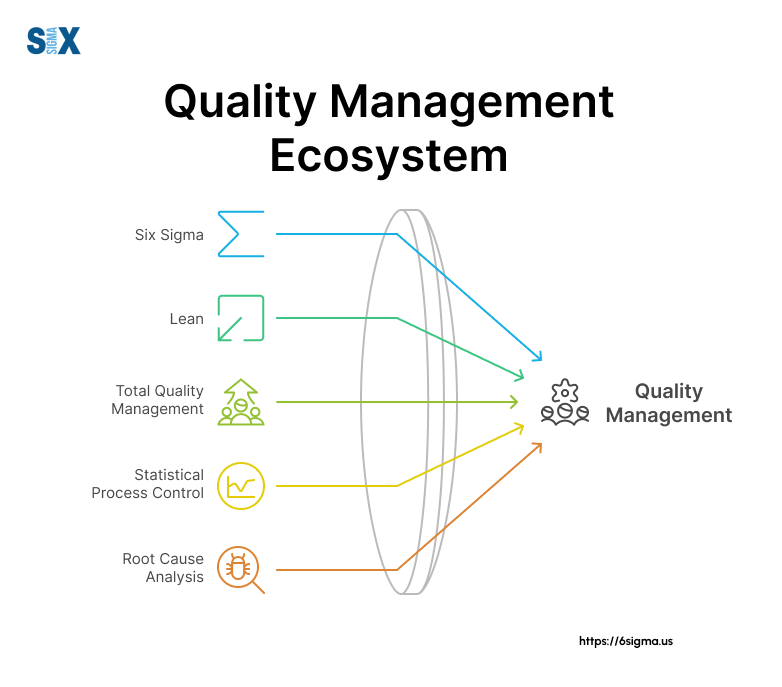
The Future of Quality Management
As industries grows, so do the approaches to quality management.
The future of QA and QC is shaped by technological advancements recently.
Emerging Trends in QA and QC
Several trends are shaping the future of quality management:
- Increased focus on predictive quality analytics.
- Integration of Internet of Things (IoT) for real-time quality monitoring.
- Emphasis on sustainability and ethical sourcing in quality standards.
- Shift towards more agile and flexible quality management approaches.
These trends are transforming how organizations approach quality, making it more proactive and integrated with overall business strategy.
SixSigma.us offers both Live Virtual classes as well as Online Self-Paced training. Most option includes access to the same great Master Black Belt instructors that teach our World Class in-person sessions. Sign-up today!
Virtual Classroom Training Programs Self-Paced Online Training Programs