Understanding Lean Thinking. 5 Principles of Lean Management
To pursue non-stop improvement, specialized approaches like Lean Production techniques, Six Sigma methods, workflow charts, error proofing, etc. play a crucial role.
Common principles embrace Lean practices, manufacturing schematics, mistake-free designs, and control charts tracking changes.
Picking suitable utilities requires factoring goals, procedures, and enhancement prospects recognition.
Key Highlights
- Continuous improvement signifies a consistent enhancement of offerings, techniques, and services via lean philosophy, Six Sigma, kaizen, and other routines refining operations persistently.
- The core revolves around optimizing processes, lessening defects, slashing wasted efforts, and upping proficiency.
- The principles stem from lean production, Six Sigma, kaizen, and besides – each lending singular viewpoints/approaches to betterment.
- Broad principles cover schematics, statistical analysis, and causal investigations – handy methods improving methods strategically.
What are the 5 Principles of Lean?
Continuous improvement requires techniques that consistently enhance processes, output, and services. Breed innovative thinking and advancement through tiny steps.
Cutting waste, and boosting worth while pacifying clients remains pivotal in cutthroat markets. Lean principles chart a refining approach to optimize processes end-to-end, continuously.
Stemming from Toyota’s production system, Lean spread broadly as a management tactic transcending realms.
Although varied instruments, their shared objective streamlines techniques, reduces costs, and boosts client satisfaction.
Practically, continuous improvement demands accommodating shifts, encouraging learning spirits, and training fitted to modificationās requisites.
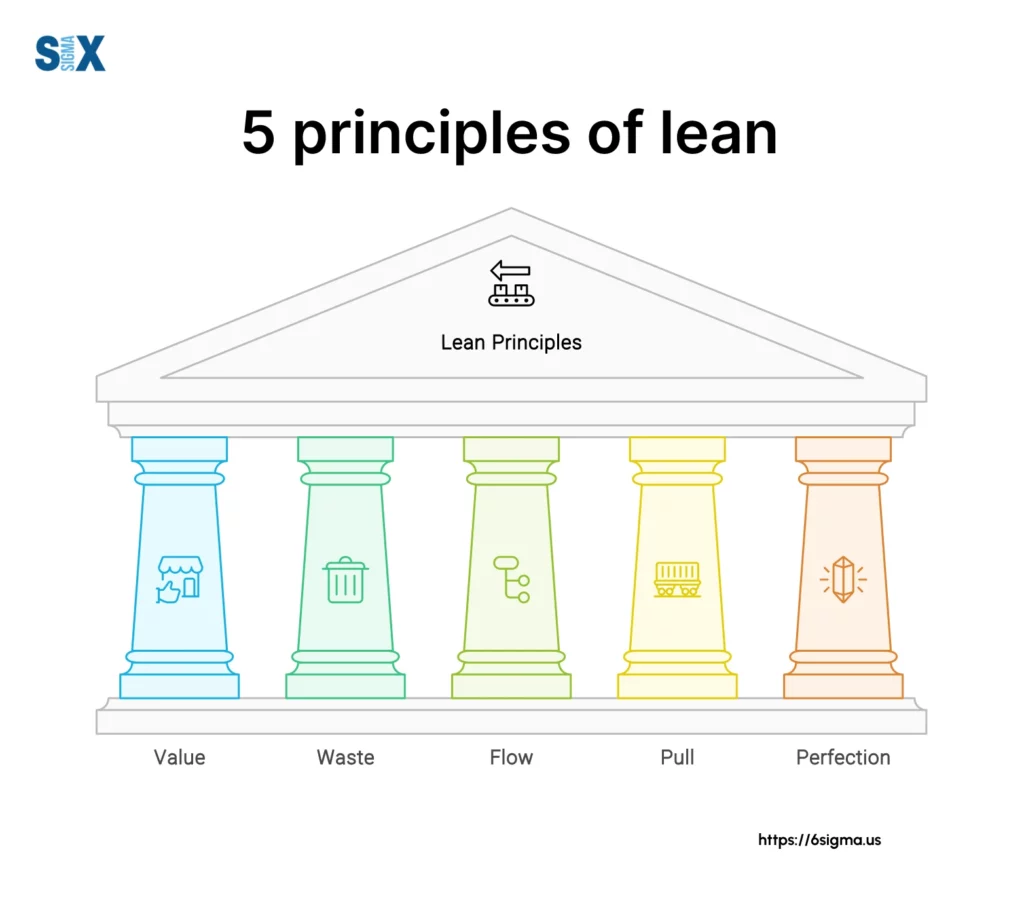
The 5 Principles of Lean Explained
The core philosophy of lean is to maximize value while minimizing waste. This is achieved by following five key principles:
- Value – Understanding value from the customer’s perspective is the critical starting point. Value is defined by the customer’s needs, not the producer’s assumptions. All lean processes must be evaluated through this value lens.
- Value Stream – Once the value is understood, the next step is to map the value stream – the entire process of activities across all functions that are required to bring a product or service to the customer. This allows you to identify and eliminate non-value-adding waste.
- Flow – With waste removed, the remaining value-creating steps are allowed to flow continuously at the rate of customer demand, rather than being delayed by bottlenecks, downtime, or other barriers. Creating flow smooths out production and service delivery.
- Pull – This principle causes upstream activities to be pulled by downstream customer demand rather than pushed based on projected forecasts. Work is pulled through the system only as needed, reducing inventory and overproduction.
- Perfection – Establishing a culture and processes of continuous improvement (called kaizen) ensures that value creation never stops being perfect. Lean thinking constantly identifies the next opportunities for waste reduction and value enhancement.
Lean Tools and Techniques
Lean provides a comprehensive set of tools and techniques to drive continuous improvement and eliminate organizational waste.
While the core principles provide a high-level philosophy, these lean tools allow teams to methodically identify opportunities, implement changes, and sustain an ongoing culture of optimization. Some of the most widely used lean tools and techniques include:
Value Stream Mapping (VSM)
This technique visually maps the flow of materials and information across a value stream, exposing areas of inefficiency, waste, and opportunities for improvement. VSM is foundational for identifying lean transformation priorities.
5S System: This workplace organization methodology focuses on maintaining an orderly, clean, and efficient workspace to reduce waste and non-value-added activities. 5S stands for Sort, Straighten, Shine, Standardize, and Sustain.
Kaizen: Meaning “continuous improvement” in Japanese, kaizen is the practice of continually making small, incremental changes to eliminate waste. It emphasizes the involvement of cross-functional teams in driving innovation.
Kanban: This lean manufacturing scheduling system uses visual signals to trigger the production and movement of materials based on downstream demand. Kanban aims to optimize inventory levels and prevent overproduction.
Just-In-Time (JIT): JIT is a philosophy of having the right materials, at the right time, at the right place, and in the exact amount required. It eliminates the waste of excess inventory.
Jidoka: Also called “autonomation”, Jidoka refers to giving machines or processes the capability to stop automatically when an abnormal condition is detected, preventing defects from being passed downstream.
Poka-Yoke: These “mistake-proofing” techniques create processes and designs that prevent errors and defects from occurring in the first place through warnings, constraints, and fail-safe practices.
SMED: Single-Minute Exchange of Die is a set of techniques to quickly perform manufacturing changeovers, reducing downtime between product runs.
TPM: Total Productive Maintenance optimizes equipment reliability through employee involvement in preventative maintenance.
Implementing the 5 Principles of Lean
While understanding the 5 principles of lean is important, putting them into practice is key to unlocking the full benefits. Implementing lean principles requires a systematic approach and commitment across the entire organization.
Creating a Lean Culture
Lean is not just a set of tools, but a philosophy that needs to be embraced by leadership and embodied in the company culture.
This involves continuous training, encouraging employee engagement, and tying performance metrics to lean goals. A lean culture empowers employees at all levels to identify waste and suggest improvements.
Value Stream Mapping
Value stream mapping is a core lean tool that maps out the flow of materials and information required to deliver a product or service to the customer.
By analyzing the current state value stream, companies can identify bottlenecks, waste, and opportunities for creating a leaner future state. Value stream mapping facilitates lean implementation by providing a blueprint.
Lean Tools and Techniques
There are many lean manufacturing tools and techniques that enable the principles, such as:
- Kaizen (continuous improvement) events
- 5S workplace organization
- Kanban pull systems
- Total productive maintenance
- Mistake-proofing (poka-yoke)
- Quick changeover (SMED)
Using these tools in a systematic way based on value stream mapping allows companies to progressively eliminate waste and optimize flow.
Change Management
Implementing lean principles inevitably involves changing processes and culture, which can face resistance.
Effective change management through training, communication, and getting buy-in is critical for a successful lean transformation. Lean leaders must be able to communicate the urgency and vision for change.
Continuous Improvement Mindset
Lean is a journey of continuous improvement, not a one-time implementation. Companies must continuously re-evaluate value streams, improve processes, and raise the bar.
Ingrained habits of identifying waste, analyzing root causes, and experimenting with improvements are essential for sustainable lean gains.
Benefits of Lean Principles
Implementing the 5 lean principles can provide immense benefits for organizations across industries. Some of the key advantages of adopting lean thinking and practices include:
Increased Efficiency and Productivity
One of the core tenets of lean is the elimination of waste (muda) in all forms – whether it’s wasted time, materials, motion, or other resources.
By identifying and removing non-value-added activities, lean principles help streamline processes and improve overall efficiency. This leads to higher productivity, reduced lead times, and increased output with the same or fewer resources.
Improved Quality with the Principles of Lean
The lean focus on getting things right the first time, combined with principles like built-in quality and stopping to fix problems, leads to higher-quality outputs. Defects are caught earlier and continuous improvement ensures consistent quality over time.
Lower Costs
Increased efficiency, reduced waste, and improved quality all contribute to lowering operational costs for the organization. Just-in-time production minimizes inventory-carrying costs as well.
Better Customer Satisfaction with the Principles of Lean
By centering on delivering value to the customer through a perfect value stream, lean ensures that products/services meet or exceed customer needs. This leads to higher customer satisfaction rates.
Engaged Workforce
Lean encourages employee involvement and empowerment at all levels. Practices like daily kaizen create an atmosphere of continuous learning and buy-in from the workforce.
Competitive Advantage using the Principles of Lean
In today’s marketplace, being lean and agile is key to outperforming competition. Lean provides a structured way to create more value for customers with fewer resources.
Sustainability
Lean’s focus on reducing all forms of waste makes it an environment-friendly practice that minimizes the carbon footprint of an organization.
Principles of Lean Across Industries
The principles of lean are not limited to just manufacturing – they can be applied across various industries to drive efficiency and eliminate waste. Here are some examples of how lean is being adopted in different sectors:
Lean Healthcare
Healthcare organizations are implementing lean principles to improve patient flow, reduce waiting times, and minimize errors and waste of resources/supplies. Lean tools like value stream mapping help identify non-value-added activities in patient journeys.
Just-in-time principles ensure supplies are available when needed. Overall, lean enables healthcare providers to deliver higher-quality care at lower costs.
Lean Construction
The construction industry has started embracing lean to increase productivity and reduce project delays. Lean construction focuses on getting the right materials, equipment, and information to workers precisely when needed.
Lean Services
Service organizations like banks, insurance companies, IT firms, etc. are also adopting lean principles. Concepts like continuous flow, pull production, and stopping-the-line when issues arise help improve responsiveness to customers.
Value stream mapping analyzes end-to-end service delivery processes to identify and eliminate non-value-adding activities. Visual management techniques like kanban boards provide transparency into workloads.
Lean Startups
The lean startup methodology applies lean principles to the process of starting a company and developing products/services. It advocates iterative development, continuous feedback loops, and a disciplined approach to testing assumptions.
This allows startups to eliminate wasteful activities, pivot quickly when needed, and create offerings that truly deliver customer value.
Moving Ahead
Centrally, Lean spotlights maximizing worth, choreographing streamlined worth-delivery, and eliminating wastage amid the total value stream.
The five principles of lean offer structure improve through value-honing, stream-mapping, smooth motion, pull-based making, and unremitting upgrading.
Enterprises achieve competitiveness, lower costs, elevate excellence, and enhance client satisfaction sustainably.
SixSigma.us offers both Live Virtual classes as well as Online Self-Paced training. Most option includes access to the same great Master Black Belt instructors that teach our World Class in-person sessions. Sign-up today!
Virtual Classroom Training Programs Self-Paced Online Training Programs