Deming’s 14 Points: Transforming Business Through Quality Management
The 14 principles, which are form the cornerstone of Total Quality Management (TQM), also known as Deming’s 14 Points, are not just theoretical concepts but practical guidelines that have revolutionized businesses across the globe.
Deming’s 14 Points, first introduced in his seminal work “Out of the Crisis“, provide a comprehensive framework for organizational transformation, focusing on long-term viability, continuous improvement, and a system-wide approach to quality.
Drawing from my extensive work with Fortune 500 companies and government institutions, I can attest to the enduring relevance of these principles.
Key Highlights
- Overview of Deming’s 14 Points and TQM
- Detailed explanation of each principle
- Implementation challenges and best practices
- Impact on organizational culture and performance
- Long-term relevance in modern quality management
- Practical insights from industry applications
- Future trends in quality management
Introduction to Deming’s 14 Points
W. Edwards Deming’s contributions to Total Quality Management (TQM) stand out as truly revolutionary. Deming, an American statistician and management consultant, played a pivotal role in Japan’s economic revival post-World War II.
His philosophy, encapsulated in his 14 Points, forms the bedrock of TQM and continues to shape modern quality management practices.
Deming’s approach to quality was holistic, emphasizing the importance of systems thinking and continuous improvement.
This philosophy aligns closely with methodologies like Six Sigma, where professionals often pursue Six Sigma certification to master data-driven problem-solving and process optimization.
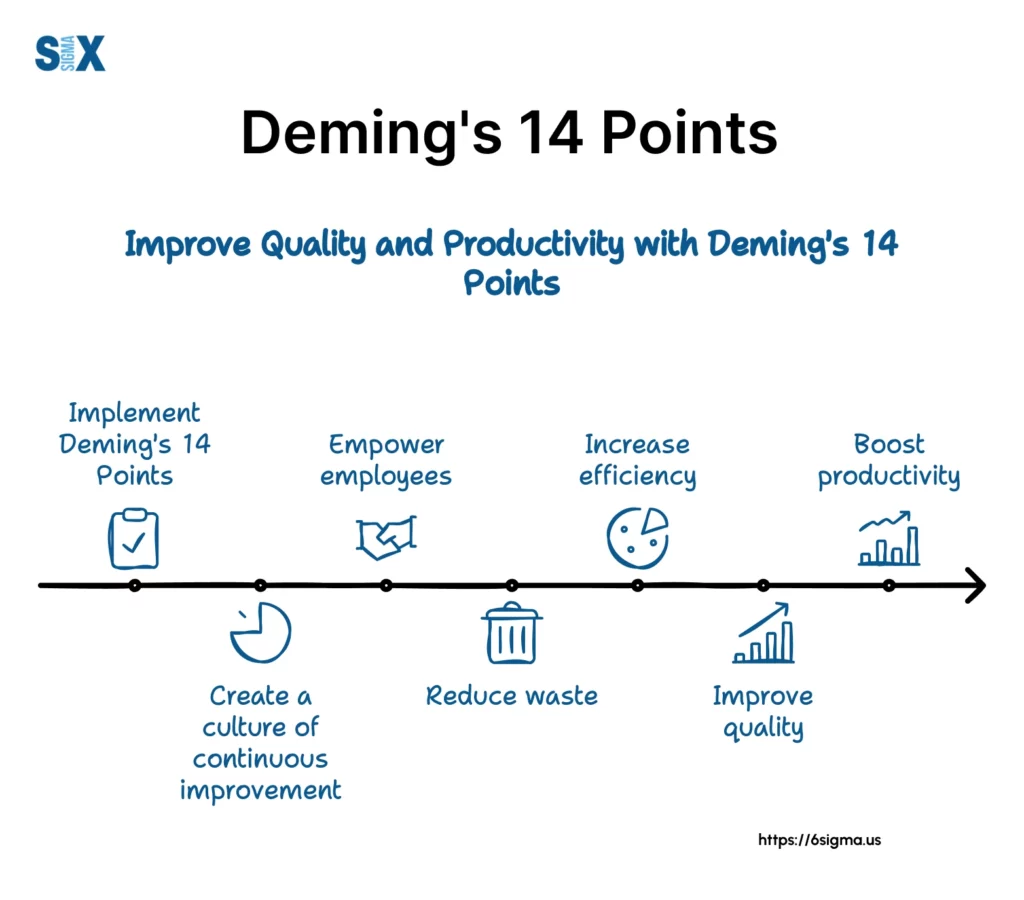
Deming’s 14 Points, The System of Profound Knowledge
Deming’s 14 Points are an outgrowth of what Deming called the “System of Profound Knowledge“.
This system comprises four interrelated components: appreciation for a system, knowledge about variation, theory of knowledge, and psychology.
- Appreciation for a system: This involves understanding how different parts of an organization interact and affect each other.
- Knowledge about variation: Recognizing the difference between common and special causes of variation in processes.
- Theory of knowledge: Understanding how we learn and make decisions based on data.
- Psychology: Recognizing human behavior and motivation in the workplace.
These components form the philosophical foundation for Deming’s 14 Points, providing a framework for transforming management practices and organizational culture.
Deming’s 14 Points Explained
Now, let’s see the Deming’s 14 Points. As we explore these principles.
1. Create Constancy of Purpose
This point emphasizes the importance of long-term planning and vision.
Clear, consistent purpose can drive innovation and improvement. It’s about focusing on becoming competitive, staying in business, and providing jobs, rather than short-term profits.
2. Adopt the New Philosophy
This principle calls for a fundamental shift in thinking. It’s about embracing quality as a core value, not just a department or initiative.
3. Cease Dependence on Inspection
Deming argued that quality should be built into the process, not inspected after the fact.
This aligns closely with methodologies emphasized in six sigma certification programs, which focus on building quality into the process through improvement and statistical process control, rather than relying solely on inspection.
By focusing on prevention rather than detection, we can significantly reduce defects and improve overall quality, a skillset developed through root cause analysis training to identify and address process inefficiencies at their source.
4. End the Practice of Awarding Business on Price Alone
This point stresses the importance of building long-term relationships with suppliers based on quality and trust, not just price.
This approach can lead to more consistent quality and lower total costs in the long run.
5. Improve Constantly and Forever
Continuous improvement is at the heart of both Deming’s philosophy and Six Sigma, and earning a six sigma green belt certification equips professionals with the tools to consistently enhance processes and products.
It’s about never being satisfied with the status quo and always looking for ways to enhance processes and products.
6. Institute Training on the Job
Effective training is crucial for quality improvement. This can range from foundational awareness programs, like those covered in Six Sigma White Belt certification or a Lean Introduction, to more involved, job-specific training to ensure everyone understands their role in the quality system.
Well-designed, job-specific training can dramatically improve performance and reduce errors.
7. Institute Leadership
Deming emphasized that managers should be leaders, not just supervisors.
This involves understanding the work being done, providing support, and fostering an environment of continuous learning and improvement.
8. Drive Out Fear
Fear stifles innovation and honest communication.
Creating a culture where employees feel safe to speak up and take calculated risks is essential for true quality improvement.
9. Break Down Barriers Between Departments
Silos can be a major obstacle to quality improvement. In my work on cross-functional projects, breaking down these barriers can lead to better communication, more efficient processes, and higher quality outputs, principles that are central to the fundamentals of lean and support cross-functional collaboration.
10. Eliminate Slogans and Exhortations
Deming argued that slogans without substantive support can be demoralizing.
Instead, focus on providing the tools and resources necessary for employees to do their best work.
11. Eliminate Numerical Quotas
Arbitrary quotas can lead to poor quality and low morale. Instead, focus on improving processes and providing the support necessary to achieve high-quality results.
12. Remove Barriers to Pride of Workmanship
Employees should be able to take pride in their work. This means removing obstacles that prevent them from doing their best, whether it’s outdated equipment, poor training, or ineffective management practices.
13. Institute a Vigorous Program of Education and Self-improvement
Continuous learning is essential in this business environment.
Ongoing education can drive innovation and improve quality.
14. Put Everybody in the Company to Work Accomplishing the Transformation
Quality improvement is everyone’s responsibility.
This point emphasizes the need for a company-wide commitment to transformation and continuous improvement.
Implementing Deming’s 14 Points in Modern Organizations
Implementing Deming’s principles can be challenging, particularly in organizations with entrenched cultures.
Common obstacles include resistance to change, short-term thinking, and a lack of leadership buy-in.
Best Practices for Successful Implementation of Deming’s 14 Points
Successful implementation of Deming’s 14 points requires a systematic approach.
Based on my experience, some best practices include:
- Start with leadership education and buy-in
- Develop a clear implementation plan
- Provide comprehensive training at all levels
- Use data-driven decision making
- Celebrate small wins to build momentum
- Continuously assess and adjust the implementation strategy
Impact of Deming’s 14 Points on Business Management
Deming’s 14 Points have had a profound impact on the development of Total Quality Management and continuous improvement methodologies like Six Sigma.
They’ve shifted focus from inspection to prevention, emphasized the importance of systems thinking, and highlighted the critical role of leadership in quality management.
Long-term Effects of Deming’s 14 Points on Organizational Culture and Performance
Organizations that successfully implement Deming’s 14 points often see significant improvements in quality, productivity, and employee satisfaction.
These principles can transform organizational culture, fostering innovation, collaboration, and a genuine commitment to quality.
The Enduring Relevance of Deming’s 14 Points
Deming’s 14 Points continue to be relevant today.
They provide a comprehensive framework for quality management that goes beyond mere tools and techniques, addressing fundamental issues of leadership, culture, and systems thinking.
Future of quality management in light of Deming’s 14 Points
As we look to the future, Deming’s principles will continue to shape quality management practices.
The emphasis on continuous improvement, data-driven decision making, and systems thinking aligns well with emerging trends in technology and management.
While the specific tools and techniques may evolve, the fundamental principles outlined in Deming’s 14 Points will continue to guide organizations in their pursuit of excellence.
As quality professionals, it’s our responsibility to understand, apply, and evolve these principles to meet the challenges of the future.
SixSigma.us offers both Live Virtual classes as well as Online Self-Paced training. Most option includes access to the same great Master Black Belt instructors that teach our World Class in-person sessions. Sign-up today!
Virtual Classroom Training Programs Self-Paced Online Training Programs