Decoding Lean Methodologies – Lean vs Six Sigma. Which One to Pick?
Companies want to refine workflows, boost quality, and keep enhancing, always. Lean vs Six Sigma are two notable techniques recognized for helping with these goals.
They both focus on optimizing techniques and slashing wasted efforts. Yet they differ in their ground rules, instruments, and routines.
Even though both Lean and Six Sigma try cutting waste, always advancing and gratifying buyers, they take separate routes for arriving at shared targets. Their specific methods, utilities, and priorities diverge.
Key Highlights
- Lean and Six Sigma are two popular ways businesses polish up how jobs get done.
- Both eliminate waste, lessen errors, and refine proficiency. But they follow distinct ground rules and instruments.
- Lean centers smooth motions, scrubbing inefficient footling and streamlining methods.
- Six Sigma spotlights data-guided choosings, stats appraisals, and near-perfecting work via constancy increments.
- While hitting shared ends–higher quality and optimized output–they follow unique approaches.
What is Lean and Six Sigma?
Companies aim to ship solutions to buyers smoothly while keeping actions running cost-effectively. Two known methods to achieve this successfully are Lean and Six Sigma.
Though sharing similarities, their approaches are quite opposite.
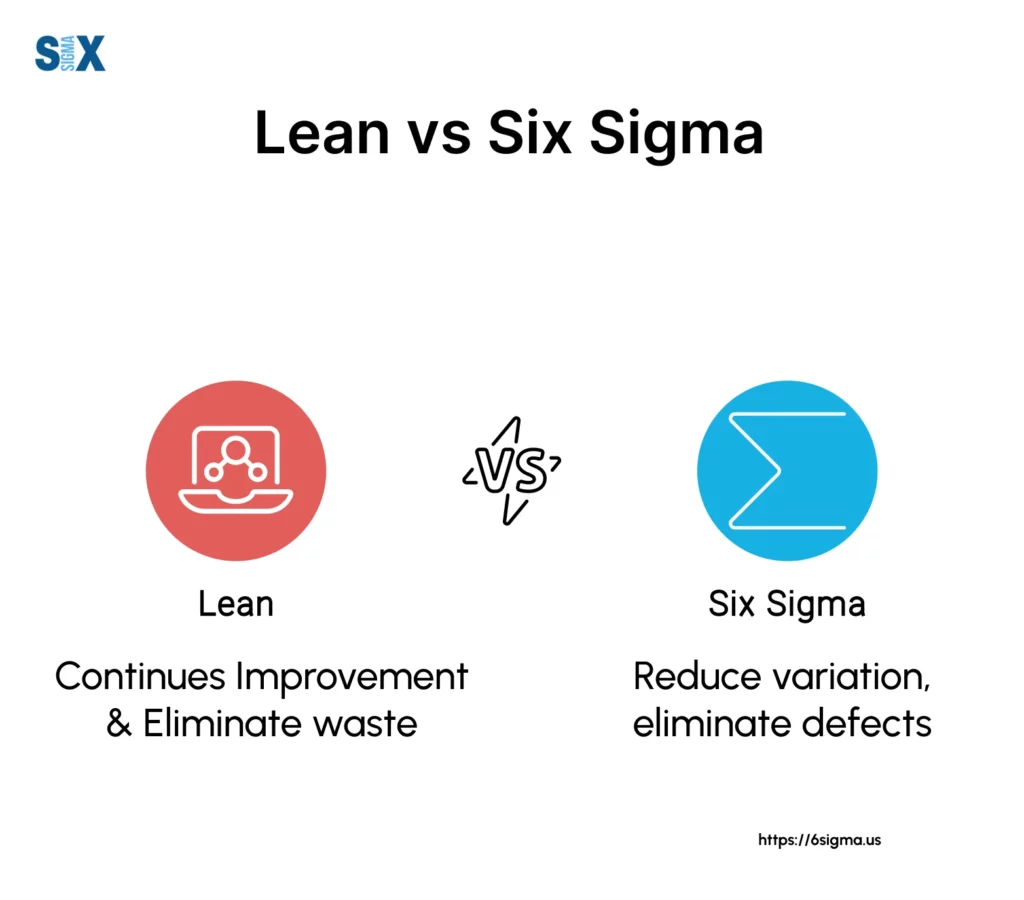
Lean grew from Toyota’s system improving upon wasted grunt and adding worth from customers’ view. This increases proficiency, lowers cost, and delights buyers.
Six Sigma utilizes data-driven analytics and stat methods for measuring, examining, and boosting techniques. Its goal reaches perfection lopping off defects/blunders.
Together Lean/Six Sigma synchronizes yet Lean highlights wastage-eradication and workflow streamlining. Six Sigma zeroes defects limiting inconsistency.
Key Principles and Methodologies
Lean and Six Sigma are process improvement methodologies aimed at enhancing quality, reducing waste, and increasing efficiency within an organization. However, they have distinct principles and methodologies that set them apart.
Lean Principles and Methodology:
Lean manufacturing, also known as lean production or simply “lean”, is a methodology that originated from the Toyota Production System. It focuses on eliminating waste (known as “muda” in Japanese) and creating value for the customer. The core lean principles include:
- Value: Identify and focus on activities that create value from the customer’s perspective.
- Value Stream: Map the entire process flow to identify and eliminate non-value-adding activities.
- Flow: Ensure a smooth and continuous flow of materials and information throughout the value stream.
- Pull: Produce only what is needed when it is needed, based on customer demand.
- Perfection: Continuously improve processes by eliminating waste and pursuing perfection.
Lean techniques, such as value stream mapping, 5S (sort, straighten, shine, standardize, sustain), kanban (pull system), kaizen (continuous improvement), and just-in-time (JIT) production, are employed to achieve these principles.
Six Sigma Methodology
Six Sigma is a data-driven, disciplined approach to process improvement that aims to reduce defects and variations in processes.
It was developed by Motorola in the 1980s and later popularized by companies like General Electric. The Six Sigma methodology follows the DMAIC (Define, Measure, Analyze, Improve, Control) cycle:
- Define: Clearly define the problem, customer requirements, and project goals.
- Measure: Collect data and measure the current process performance.
- Analyze: Analyze the data to identify the root causes of defects or variations.
- Improve: Develop and implement solutions to eliminate root causes.
- Control: Establish controls to sustain the improvements and monitor performance.
Six Sigma utilizes various statistical and analytical tools, such as process mapping, cause-and-effect diagrams, hypothesis testing, and control charts, to identify and eliminate defects and variations in processes.
Both Lean and Six Sigma share the common goal of process improvement, but they approach it from different angles.
Lean focuses on eliminating waste and creating value, while Six Sigma concentrates on reducing defects and variations through data-driven analysis and statistical methods.
Similarities and Differences
While Lean and Six Sigma have some similarities, there are also key differences between lean vs six sigma process improvement methodologies.
Similarities
- Both aim to improve quality, increase efficiency, and reduce waste
- They rely on data analysis and statistical tools to identify problems and opportunities
- Employee involvement and training are crucial for the successful implementation
- A structured approach with defined steps/principles is followed
- They can be applied across various industries and organizational functions
- The focus is on continuous incremental improvement rather than radical changes
- Customer satisfaction is a core goal
Differences
- Origins (Lean from Toyota, Six Sigma from Motorola)
- Primary goals (Lean – reduce waste, Six Sigma – reduce variation/defects)
- Tools used (Lean uses value stream mapping, 5S, etc.; Six Sigma relies on DMAIC, and statistical analysis)
- Improvement approach (Lean is process-focused, Six Sigma is project-based)
- Emphasis (Lean on flow and pull, Six Sigma on measuring and analyzing)
- Certification levels (Lean has no belt system, Six Sigma has belts like Green Belt, and Black Belt)
- Deployment (Lean as an enterprise philosophy, Six Sigma often departmental)
While there is some overlap, Lean targets efficiency through waste elimination using lean principles like just-in-time production. Six Sigma, on the other hand, aims to minimize process variation and defects using data-driven quality management techniques.
Many organizations leverage the strengths of both methodologies through a combined Lean Six Sigma approach.
Implementation and Integration of Lean and Six Sigma
Implementing Lean and Six Sigma methodologies requires a strategic approach and commitment from all levels of an organization. While they can be adopted separately, many companies choose to integrate both philosophies to maximize process improvement and operational excellence.
Lean Implementation
Lean manufacturing principles are typically implemented through a series of techniques like kaizen events, value stream mapping, 5S workplace organization, and just-in-time production.
The journey often starts with training employees on lean thinking and waste identification. Pilot areas are selected to trial lean tools and build experience before spreading lean across the entire operation.
Six Sigma Implementation
Six Sigma follows a structured approach using the DMAIC (Define, Measure, Analyze, Improve, Control) methodology.
It involves training a hierarchy of champions, master black belts, black belts, and green belts. Projects are selected based on their potential impact, and belts lead cross-functional teams through the data-driven DMAIC phases to reduce defects and variation.
Integrating Lean and Six Sigma
While Lean focuses on eliminating non-value-added activities (wastes), Six Sigma aims to minimize process variation and defects.
An integrated Lean Six Sigma approach provides a comprehensive toolkit to streamline processes and enhance quality simultaneously. Some ways to merge the two include:
- Using Lean tools like 5S and visual management to create a conducive environment for Six Sigma projects
- Applying Six Sigma’s data analysis rigor to validate and measure Lean improvements
- Training belts and deploying teams to work on Lean Six Sigma projects holistically
- Adopting Lean Six Sigma certifications that cover principles from both frameworks
Organizations need to carefully plan and execute their Lean Six Sigma roadmap with leadership commitment, training, project selection, and tracking mechanisms in place.
Benefits and Challenges
Both Lean and Six Sigma methodologies offer significant benefits when implemented effectively, but they also come with challenges.
Benefits of Lean
- Reduces waste and non-value-added activities, leading to increased efficiency and productivity
- Improves workflow and process flow, resulting in faster cycle times
- Enhances customer satisfaction by delivering higher quality products/services
- Promotes a culture of continuous improvement and employee engagement
- Requires less capital investment compared to other improvement initiatives
Challenges of Lean Implementation
- Overcoming resistance to change from employees and management
- Requiring a shift in mindset and company culture towards continuous improvement
- Sustaining Lean practices and avoiding a relapse into old habits
- Lack of leadership commitment and insufficient training can hinder success
Benefits of Six Sigma
- Provides a structured, data-driven approach to reducing defects and variations
- Improves quality and consistency, leading to increased customer satisfaction
- Delivers significant cost savings by eliminating defects and rework
- Enhances problem-solving and decision-making capabilities within the organization
- Offers a clear career path and recognition through Belt certification levels
Challenges of Six Sigma Implementation
- Requires extensive training and investment in resources (time, money, people)
- Can be perceived as complex, rigid, and bureaucratic by some organizations
- May face difficulties in sustaining long-term commitment and momentum
- Overemphasis on data and statistics can overshadow other important factors
Integrating Lean and Six Sigma (Lean Six Sigma) can help organizations leverage the strengths of both methodologies while mitigating their challenges.
However, successful integration requires careful planning, training, and a strong commitment from leadership and employees alike.
Case Studies and Examples
To better understand the practical applications of Lean and Six Sigma methodologies, let’s examine some real-world case studies and examples.
Lean Manufacturing at Toyota
Toyota is widely regarded as the pioneer of the Lean manufacturing philosophy. The Toyota Production System (TPS) is a prime example of how Lean principles like continuous improvement, respect for people, and elimination of waste can revolutionize operations.
By implementing techniques such as just-in-time production, kanban systems, and kaizen events, Toyota has achieved unparalleled levels of quality, efficiency, and productivity in its manufacturing processes.
Six Sigma at General Electric
General Electric (GE) is often cited as one of the most successful companies to adopt Six Sigma on a large scale.
Under the leadership of former CEO Jack Welch, GE launched its Six Sigma initiative in 1995, aiming to improve processes and reduce defects across all business units.
By training thousands of employees as Six Sigma experts (Green Belts and Black Belts), GE reportedly saved billions of dollars in costs and improved customer satisfaction significantly.
Lean in Healthcare
Hospitals and healthcare organizations have increasingly embraced Lean principles to streamline operations, reduce waste, and improve patient care.
For example, Virginia Mason Medical Center in Seattle implemented Lean techniques such as value stream mapping, 5S (sort, straighten, shine, standardize, sustain), and rapid process improvement workshops (RPIWs).
As a result, they achieved significant reductions in patient wait times, improved safety, and increased staff satisfaction.
Six Sigma in Financial Services
Many banks and financial institutions have adopted Six Sigma methodologies to enhance their processes, reduce errors, and improve customer experience.
For instance, Bank of America implemented Six Sigma across various divisions, including consumer banking, credit card operations, and mortgage lending.
By identifying and eliminating defects in processes like loan approvals and account openings, the bank reportedly saved millions of dollars and improved customer satisfaction scores.
Lean and Six Sigma Integration at Lockheed Martin
Aerospace and defense company Lockheed Martin has successfully integrated Lean and Six Sigma principles into its operations.
The company uses Lean techniques like value stream mapping and 5S to eliminate waste and improve flow, while Six Sigma tools like DMAIC (Define, Measure, Analyze, Improve, Control) are employed to reduce defects and enhance quality.
This combined approach has helped Lockheed Martin streamline production processes, reduce costs, and improve product quality across its various divisions.
Future Trends and Conclusions
As businesses continue to strive for greater efficiency, quality, and customer satisfaction, the integration of Lean and Six Sigma methodologies is expected to gain further momentum.
The synergies between these two approaches have proven to be highly effective in driving continuous improvement and optimizing processes across various industries.
One emerging trend is the adoption of Lean Six Sigma in the service sector, such as healthcare, finance, and customer service operations.
By combining the waste reduction principles of Lean with the data-driven, analytical tools of Six Sigma, service organizations can streamline their processes, reduce errors, and enhance customer experience.
Additionally, the integration of digital technologies, such as automation, data analytics, and artificial intelligence (AI), with Lean Six Sigma practices is becoming increasingly prevalent.
These technologies can assist in identifying process inefficiencies, predicting potential defects, and optimizing resource allocation, further amplifying the benefits of Lean Six Sigma implementations.
As the business landscape continues to evolve, organizations will likely seek more agile and adaptable approaches to process improvement. This may lead to integrating Lean Six Sigma with other methodologies, such as Agile project management or Design Thinking, to create hybrid frameworks tailored to specific business needs.
SixSigma.us offers both Live Virtual classes as well as Online Self-Paced training. Most option includes access to the same great Master Black Belt instructors that teach our World Class in-person sessions. Sign-up today!
Virtual Classroom Training Programs Self-Paced Online Training Programs