Continuous Process Improvement (CPI): A Guide for Businesses
Continuous process improvement (CPI) describes identifying, outlining, implementing, measuring, and analyzing effectiveness shifts within an organization’s workflows.
Surpassing the notion that “unbroken works best”, this recognizes that even flowing operations can benefit from refinement and optimization.
Key Highlights
- Steady betterment persists – refining products, services, and methods incrementally.
- Principled change coordination sustains learning, innovation, and adaptability spirits.
- Common techniques
- Sound execution
- Tools like process observation, fluidity boosters, and performance trackers aid progress together.
- Creating a better culture.
- Challenges.
- Progress pathway.
What is Continuous Process Improvement?
Continuous process improvement (CPI) is the cornerstone of operational excellence and long-term organizational success.
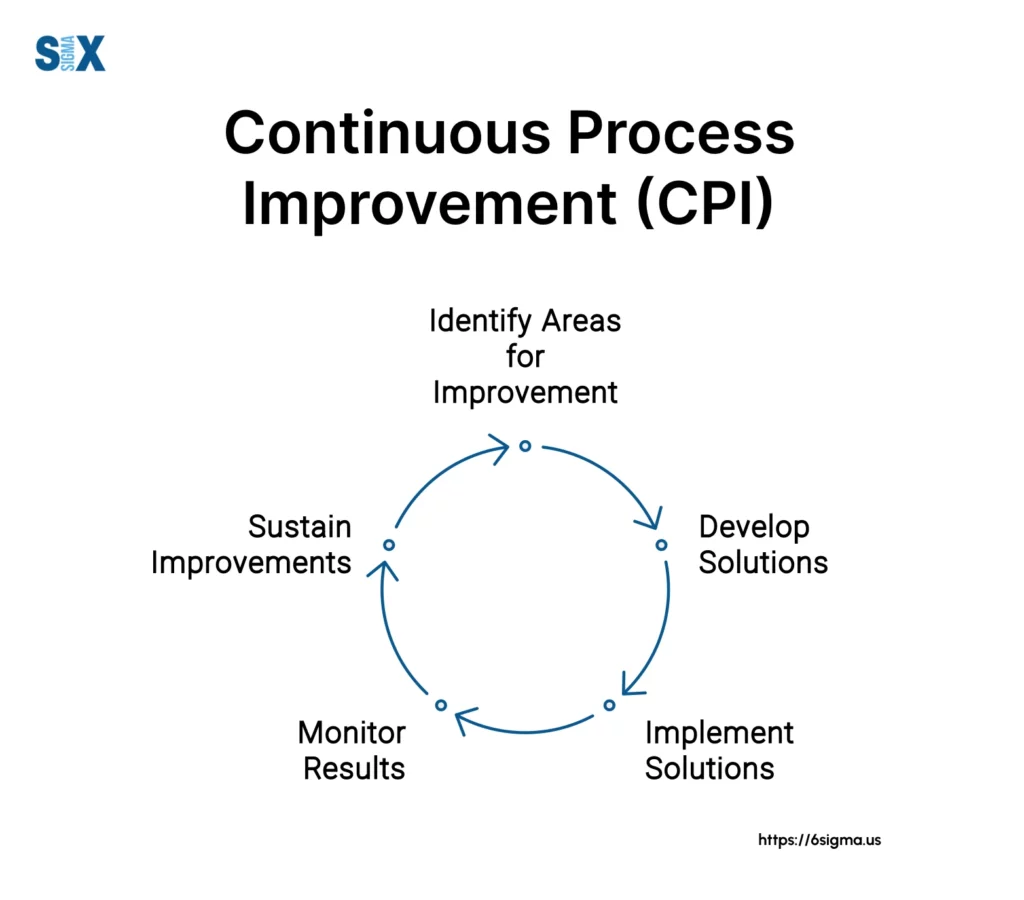
Continuous Process Improvement (CPI) is an ongoing effort to enhance products, services, or processes through incremental and breakthrough improvements.
CPI advocates for a more gradual and iterative approach unlike business process reengineering, which often involves radical, disruptive changes.
It recognizes that even well-established processes can benefit from fine-tuning and optimization, allowing organizations to adapt to changing market conditions, customer needs, and technological advancements.
The philosophy of Continuous Process Improvement is built upon three fundamental principles:
- Incremental changes: Rather than pursuing sweeping overhauls, Continuous Process Improvement (CPI) focuses on making small, manageable improvements that collectively yield significant results over time.
- Employee involvement: Continuous Process Improvement (CPI) thrives on an organization’s workforce’s collective knowledge and experience.
- Continuous improvement cycles: Continuous Process Improvement (CPI) is not a one-time initiative but rather an ongoing, cyclical process of identifying opportunities, implementing changes, measuring results, and repeating the cycle with the gained insights.
Benefits of Continuous Process Improvement
The benefits of embracing a continuous process improvement mindset are multifaceted and far-reaching.
By consistently optimizing processes, organizations can unlock a myriad of advantages, including:
- Increased efficiency and productivity: Continuous Process Improvement (CPI) initiatives are designed to streamline workflows, eliminate waste, and optimize resource utilization.
- Reduced costs and errors: Through process analysis and improvement, organizations can identify and mitigate potential sources of errors, defects, or inefficiencies.
- Superior customer experience: Continuous Process Improvement (CPI) keeps customer needs at the forefront, driving organizations to refine their offerings and service delivery continually.
- Engaged and empowered workforce: Employees who are actively involved in the improvement process feel a sense of ownership and empowerment.
- Agility and resilience: By embracing a culture of continuous improvement, organizations become more agile and resilient.
- Competitive advantage: Ultimately, the cumulative effects of CPI – improved efficiency, reduced costs, superior customer experiences, and organizational agility – translate into a significant competitive advantage.
Take your first step to implement these benefits for your organization! Check out our short course on Lean Six Sigma Overview to get a solid foundation for implementing CPI.
Common Continuous Improvement Methodologies
While the principles of continuous process improvement are universal, various methodologies have emerged to guide its implementation.
Some of the most widely adopted and effective approaches include:
Plan-Do-Check-Act (PDCA) cycle: Also known as the Deming Cycle or the Shewhart Cycle, the PDCA cycle is a four-step iterative process for continuous improvement.
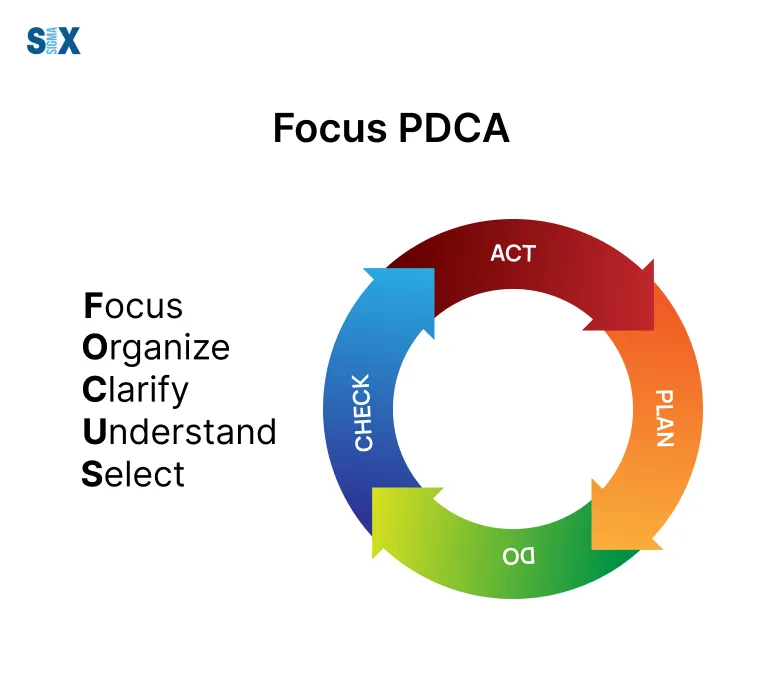
Kaizen (continuous improvement): Originating from Japan, the Kaizen philosophy emphasizes incremental, ongoing improvements across all aspects of an organization.
Theory of Constraints (TOC): This methodology identifies and addresses the most significant constraint or bottleneck in a process, recognizing that improving this constraint will yield the greatest overall improvement.
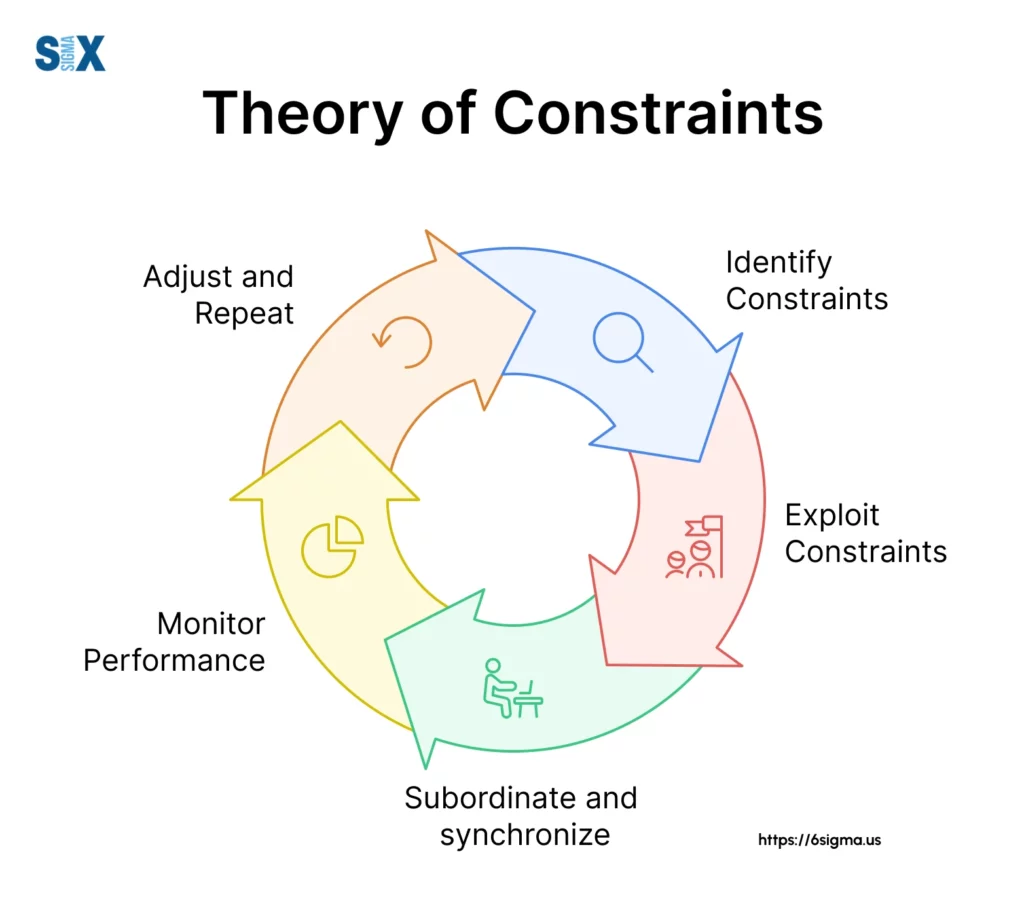
Value stream mapping: A lean technique, value stream mapping involves visualizing the flow of materials and information required to deliver a product or service.
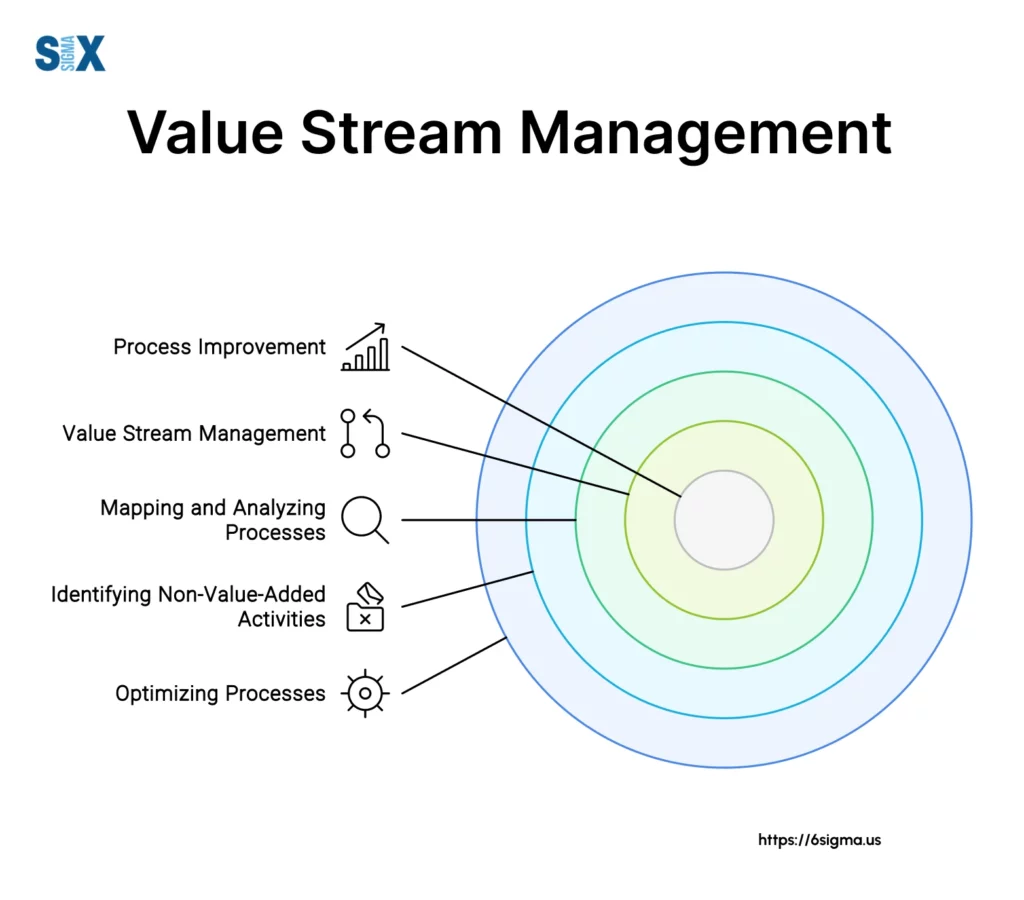
While each methodology, including the Six Sigma methodology, has its unique strengths and applications, they share a common goal: to continuously improve processes, enhance organizational performance, and create value for customers
Want to master these methodologies and apply them effectively? Lean Six Sigma Green Belt course offers in-depth training on CPI techniques.
Implementing Continuous Process Improvement
Successful implementation of continuous process improvement requires a structured and disciplined approach.
While the specific steps may vary depending on the chosen methodology, a general framework can be followed:
- Define scope and identify opportunities: The first step is to clearly define the scope of the improvement initiative and identify specific processes or areas that present opportunities for optimization. This often involves gathering data, analyzing metrics, and soliciting feedback from stakeholders, including customers and employees.
- Build a cross-functional team: Continuous improvement is a collaborative effort that requires diverse perspectives and expertise. Assembling a cross-functional team with representatives from various departments or roles—such as those trained in process optimization through a Six Sigma Green Belt certification—ensures a comprehensive understanding of the process and its inter-dependencies
- Process mapping and analysis: To truly understand the current state of a process, it is essential to map it out visually. Process mapping tools, such as flowcharts or value stream maps, can help identify bottlenecks, redundancies, and potential areas for improvement.
- Develop an improvement plan: Based on the insights gained from process mapping and analysis, the team can develop a detailed plan for implementing improvements. This plan should outline specific objectives, actionable steps, timelines, and metrics for measuring success.
- Test and implement changes: Before implementing changes on a large scale, it is advisable to conduct pilot tests or small-scale experiments. This approach minimizes risks and allows for adjustments based on real-world feedback and data.
- Monitor performance and optimize: Continuous improvement is an iterative process, and it is crucial to monitor the performance of implemented changes closely. Regular reviews, data analysis, and feedback loops enable organizations to fine-tune their processes further and capitalize on lessons learned.
Throughout this cycle, it is essential to maintain open communication, foster collaboration, and encourage employee engagement.
By involving stakeholders at every stage, organizations can cultivate a culture of continuous improvement and ensure the long-term sustainability of the improvement efforts.
Tools
While the core principles of continuous process improvement can be applied manually, specialized tools and technologies can greatly facilitate and streamline the implementation process.
Some of the most valuable tools in a continuous improvement practitioner’s toolkit include:
- Business process management (BPM) software: BPM software provides a centralized platform for designing, automating, and optimizing business processes. These solutions often include process modeling, workflow automation, and performance monitoring capabilities, making it easier to identify improvement opportunities and implement changes seamlessly.
- Process mining and analytics: Process mining tools analyze event log data from various systems to visualize and understand how processes are executed, often complementing techniques learned through root cause analysis training. This visibility into real-world process flows can uncover bottlenecks, deviations, and opportunities for optimization that might otherwise go unnoticed.
- Workflow automation: By automating repetitive tasks and integrating disparate systems, workflow automation tools can streamline processes, reduce manual errors, and improve overall efficiency. As processes are optimized, automation can be easily adjusted to reflect the new, improved workflows.
- Performance dashboards and metrics: Continuous improvement relies heavily on data-driven decision-making. Performance dashboards and metrics provide real-time visibility into process performance, enabling organizations to track the impact of improvement initiatives and make informed adjustments as needed.
These tools, when used in conjunction with established continuous improvement methodologies, can accelerate the pace of improvement, enhance collaboration, and facilitate data-driven decision-making.
Creating a Culture of Continuous Improvement
A culture of continuous improvement requires a fundamental shift in organizational values and behaviors, driven by the following key elements:
- Employee empowerment and ownership: Employees at all levels must be empowered to identify improvement opportunities—supported by skill-building programs like Six Sigma certification—to voice their ideas and actively participate in the change process. This sense of ownership fosters engagement, commitment, and a shared responsibility for organizational success.
- Continuous learning and development: Continuous improvement thrives in an environment that values ongoing learning and skill development. Organizations should provide training, mentorship programs, and opportunities for employees to expand their knowledge and capabilities, enabling them to contribute more effectively to improvement initiatives.
- Collaboration and cross-functional teams: Effective continuous improvement requires breaking down silos and fostering collaboration across departments and functions. Cross-functional teams bring diverse perspectives and expertise, enabling a holistic understanding of processes and their interdependencies.
- Leadership support and commitment: Visible and unwavering support from leadership is crucial for cultivating a culture of continuous improvement. Leaders must not only advocate for improvement initiatives but also allocate necessary resources, remove roadblocks, and lead by example.
- Celebrating and recognizing improvements: Acknowledging and celebrating successes, no matter how small, is essential for reinforcing the desired behaviors and sustaining momentum. Recognition programs, success stories, and visible displays of improvement achievements can motivate and inspire others to embrace the continuous improvement mindset.
Ready to lead CPI initiatives in your organization? Lean Six Sigma Black Belt course prepares you to implement and manage complex CPI projects.
By embedding these cultural elements into the fabric of the organization, continuous process improvement becomes an integral part of daily operations, decision-making, and strategic planning.
Challenges and Best Practices
While the benefits of continuous process improvement are undeniable, implementing and sustaining this approach can present various challenges.
Some of the common hurdles organizations may face include:
- Change management: Any process improvement initiative involves change, which can be met with resistance or skepticism from employees accustomed to established routines. Effective change management strategies, clear communication, and addressing concerns early on are crucial for overcoming these obstacles.
- Overcoming resistance to change: Related to change management, resistance to change can stem from various sources, such as fear of the unknown, perceived threats to job security, or a lack of understanding of the benefits. Building trust, involving employees in the process, and demonstrating quick wins can help alleviate concerns and foster acceptance.
- Sustaining improvements long-term: While implementing initial improvements may be relatively straightforward, sustaining them over the long term can be challenging. Organizations must remain vigilant, continuously monitor performance, and make adjustments as needed to prevent backsliding or complacency.
- Continuous feedback and improvement cycles: Continuous improvement is an iterative process that requires ongoing feedback, evaluation, and adjustment. Establishing robust feedback mechanisms, encouraging open communication, and maintaining a willingness to adapt and refine processes are essential for long-term success.
To overcome these challenges and maximize the benefits of continuous process improvement, organizations can adopt several best practices:
- Ensure top-down and bottom-up alignment: Both leadership and frontline employees must be aligned and committed to the continuous improvement mindset.
- Foster a culture of trust and transparency: Open communication, data sharing, and a blame-free environment are critical for identifying and addressing improvement opportunities.
- Provide adequate training and resources: Investing in employee training, tools, and resources empowers individuals to contribute effectively to improvement initiatives.
- Celebrate successes and learn from failures: Recognizing achievements and embracing failures as learning opportunities can reinforce the desired behaviors and foster a growth mindset.
- Continuously assess and adapt: Regularly reviewing progress, adjusting strategies, and adapting to changing circumstances are essential for sustaining continuous improvement over time.
By proactively addressing challenges and adhering to best practices, organizations can overcome roadblocks and fully harness the power of continuous process improvement, driving sustainable growth, innovation, and competitive advantage.
The Future of Continuous Process Improvement
As we look ahead, continuous process improvement is poised to grow and adapt to the latest trends and technologies.
Here are some of the key developments that will shape the future of CPI:
- Emerging technologies: Advancements in areas such as artificial intelligence (AI), machine learning, and robotic process automation (RPA) will profoundly impact how processes are optimized and automated.
- Digital transformation and process innovation: The rapid pace of digital transformation is forcing organizations to rethink their processes from the ground up.
- Agile and iterative methodologies: Agile principles, which emphasize iterative development, cross-functional collaboration, and rapid adaptation, are increasingly being applied beyond software development to process improvement initiatives.
- Customer-centric processes: As customer experience becomes a key differentiator, continuous process improvement will increasingly focus on optimizing processes from the customer’s perspective.
- Sustainable and responsible practices: Organizations are increasingly recognizing the importance of sustainable and socially responsible practices.
As these trends unfold, the role of continuous process improvement professionals will evolve as well.
Skillsets in areas such as data analytics, process automation, design thinking, and change management will become increasingly valuable.
This will enable them to drive sustainable growth, innovation, and competitive advantage in the industry.
SixSigma.us offers both Live Virtual classes as well as Online Self-Paced training. Most option includes access to the same great Master Black Belt instructors that teach our World Class in-person sessions. Sign-up today!
Virtual Classroom Training Programs Self-Paced Online Training Programs