Drum Buffer Rope (DBR): Maximize Throughput & Lead Time with ToC Methodology
The Drum-Buffer-Rope (DBR) method, a key part of the Theory of Constraints (TOC) developed by Eliyahu M. Goldratt, focuses on optimizing overall performance by properly addressing limiting factors.
The TOC views constraints as opportunities for improvement. At its core, DBR scheduling aims to boost throughput and flow by strategically managing the constraint or main restriction.
Inspired by Goldratt’s groundbreaking work “The Goal”, DBR takes a metaphorical approach to tackle production planning and control challenges.
The “drum” represents the constraint setting the system’s pace. The “buffer” acts as a safeguard ensuring the drum does not run dry.
The “rope” serves as a release control for work entering the system in a balanced way.
This methodology recognizes the importance of constraints while also protecting and prioritizing them, seeking to streamline operations as a result.
By addressing challenges through a conceptual mindset, innovative solutions can emerge.
Key Highlights
- Drum-Buffer-Rope (DBR) is a critical component of the Theory of Constraints (TOC), developed by Eliyahu M. Goldratt.
- Drum-Buffer-Rope (DBR) is a scheduling process that aims to increase flow and throughput by strategically managing the constraint or bottleneck within a system.
- The “drum” represents the constraint that sets the pace, the “buffer” ensures the drum never starves, and the “rope” controls the release of work.
- Drum-Buffer-Rope (DBR) offers numerous benefits, including throughput maximization, lead time reduction, and improved resource utilization.
- Successful implementation of DBR involves identifying constraints, optimizing the drum, subordinating non-constraints, and continuous improvement.
- DBR integrates principles from Lean Manufacturing and Six Sigma, enabling waste elimination, variability management, and continuous improvement.
- The future of Drum-Buffer-Rope (DBR) involves integrating emerging technologies and addressing potential limitations while continuing education and resource development.
Introduction to Drum-Buffer-Rope (DBR)
The Drum-Buffer-Rope (DBR) methodology finds its roots in the Theory of Constraints (ToC), a groundbreaking management philosophy introduced by Dr. Eliyahu M. Goldratt in his seminal work, “The Goal”.
This novel approach challenged traditional cost-accounting practices and proposed a paradigm shift in how organizations view and manage their operations.
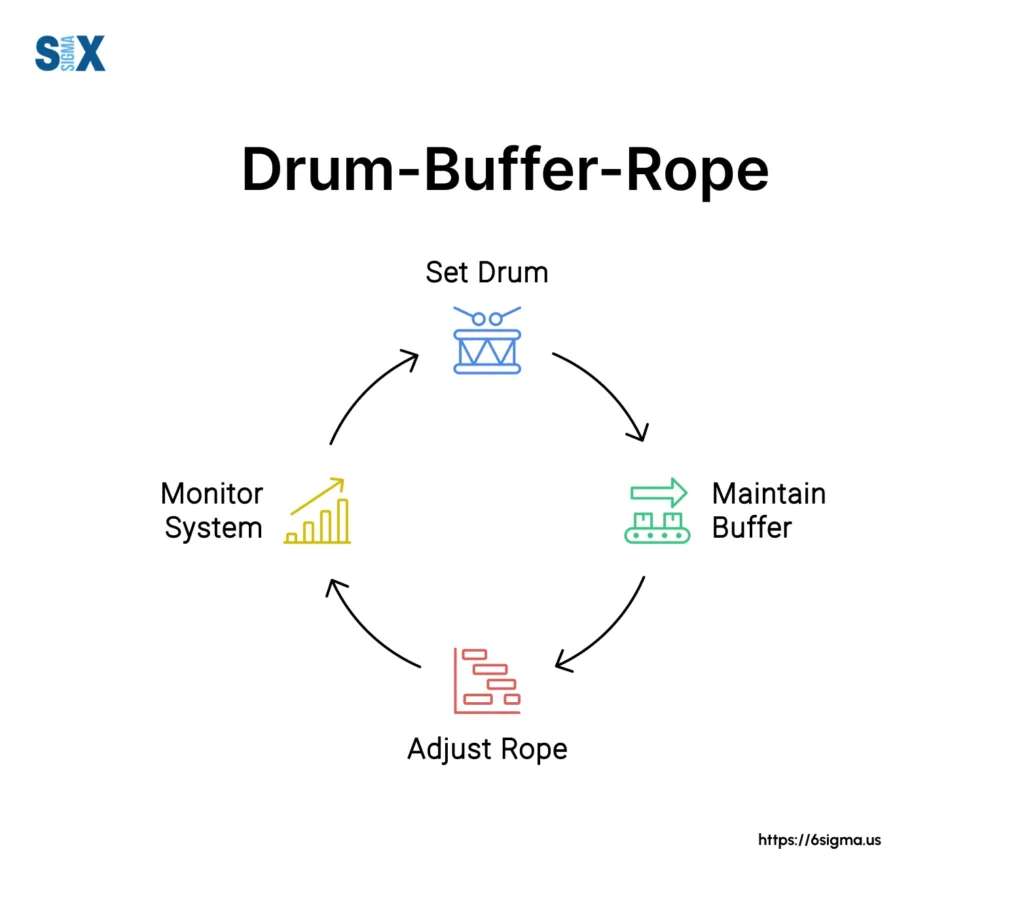
At the heart of ToC lies the recognition that every system, be it a manufacturing process, a service operation, or a business venture, is inherently constrained by at least one limiting factor, often referred to as the bottleneck or constraint.
Goldratt’s genius was in acknowledging that optimizing this constraint, rather than focusing on individual efficiencies, holds the key to maximizing the overall throughput and profitability of the system.
Principles of DBR: Drum, Buffer, and Rope
The Drum-Buffer-Rope (DBR) methodology is a practical application of the Theory of Constraints, designed to manage constraints and optimize flow in production environments.
Its name is derived from the three core components that govern its operation:
- The Drum: This represents the constraint or bottleneck that sets the pace for the entire system. Just as a drum dictates the rhythm for a marching band, the constraint determines the maximum throughput achievable by the system.
- The Buffer: To protect the constraint from starving due to variability in upstream processes, a buffer or time cushion is introduced. This buffer acts as a protective mechanism, ensuring a consistent flow of work to the constraint.
- The Rope: The rope serves as a communication and control mechanism, regulating the release of new work into the system. By synchronizing the release of work with the consumption rate of the constraint, the rope prevents excessive work-in-process (WIP) buildup and associated inefficiencies.
Benefits of Drum Buffer Rope (DBR): Throughput Maximization and Lead Time Reduction
The implementation of Drum-Buffer-Rope offers numerous benefits to organizations seeking to optimize their operations and enhance their competitive edge.
Two of the most significant advantages are throughput maximization and lead time reduction.
Throughput maximization is achieved by ensuring that the constraint, the system’s true bottleneck, operates at maximum capacity without interruption.
By subordinating non-constraints to the drum and maintaining a steady flow of work through buffers and ropes, Drum-Buffer-Rope enables the constraint to function at its full potential, thereby maximizing the overall throughput of the system.
Lead time reduction, on the other hand, is facilitated by the systematic control of WIP and the elimination of excessive inventory buildups.
By releasing work into the system only when necessary and at a rate dictated by the constraint, DBR minimizes the time materials spend waiting in queues or being processed at non-constraints.
This streamlined flow translates into shorter lead times, enabling organizations to respond more rapidly to customer demands and market changes.
Identifying and Managing Constraints using Drum Buffer Rope (DBR)
Effective bottleneck management is the cornerstone of the Drum-Buffer-Rope methodology.
Before implementing DBR, it is crucial to accurately identify the constraint or Capacity Constrained Resource (CCR) within the system.
This process often involves a comprehensive analysis of the entire value stream, encompassing material flow, information flow, and process interdependencies.
Value stream mapping, a powerful Lean Manufacturing tool, can be instrumental in pinpointing the CCR by revealing process inefficiencies, waste, and potential bottlenecks.
Value Stream Mapping to Identify Process Constraints
Value stream mapping (VSM) is a powerful diagnostic tool that enables organizations to visualize the entire flow of material and information within a process or value stream.
By creating a comprehensive map of the current state, VSM aids in identifying process constraints, bottlenecks, and sources of waste, such as excessive inventory, unnecessary transportation, or waiting times.
In the context of Drum-Buffer-Rope implementation, value stream mapping plays a crucial role in pinpointing the Capacity Constrained Resource (CCR) or bottleneck within the system.
By analyzing the value stream map, practitioners can identify the process step or resource with the lowest capacity relative to demand, effectively identifying the constraint that limits the overall throughput of the system.
Protective Capacity and Buffer Management Strategies
While the buffer’s primary function is to protect the constraint from starving due to variability in upstream processes, effective buffer management strategies are essential to ensure optimal utilization of resources and minimize waste.
One key concept in buffer management is the notion of protective capacity.
Non-constraints within the system should operate at a slightly higher capacity than the constraint to accommodate variability and prevent excessive inventory buildup.
This protective capacity, typically ranging from 25% to 30% above the constraint’s capacity, acts as a safeguard against disruptions and ensures a smooth flow of work to the constraint.
Buffer sizing is another critical aspect of buffer management. Buffers are typically divided into three zones: green, yellow, and red, each representing different levels of urgency and triggering specific actions.
By monitoring buffer status and analyzing the root causes of buffer penetration into the red zone, organizations can implement targeted improvement initiatives to reduce variability and optimize buffer sizes over time.
Implementing Drum-Buffer-Rope (DBR) in Production
Drum-Buffer-Rope (DBR) is inherently a pull production system, where work is released into the system based on the consumption rate of the constraint, rather than pushed through based on predetermined schedules or forecasts.
This pull mechanism not only prevents excessive work-in-process (WIP) buildup but also aligns production with actual demand, minimizing the risk of overproduction and associated waste.
The Drum-Buffer-Rope (DBR) methodology is closely aligned with the principles of flow manufacturing, which emphasize the smooth and continuous flow of materials and information throughout the value stream.
By subordinating non-constraints to the drum and maintaining a consistent pace dictated by the constraint, DBR enables organizations to achieve a more predictable and stable flow of work, reducing lead times and enhancing overall system responsiveness.
Work-in-process (WIP) control and Little’s Law
Effective work-in-process (WIP) control is a fundamental aspect of the Drum-Buffer-Rope methodology.
Excessive WIP can lead to longer lead times, increased inventory carrying costs, and a host of other inefficiencies that undermine the overall performance of the system.
Little’s Law, a fundamental principle in queueing theory, provides a quantitative framework for understanding the relationship between WIP, cycle time, and throughput.
According to Little’s Law, the average number of items in a queueing system (WIP) is directly proportional to the average cycle time and the average arrival rate (throughput) of items into the system.
By controlling the release of work into the system through the rope mechanism, DBR effectively manages WIP levels, ensuring that the amount of work in the system remains within optimal limits.
This not only reduces lead times but also improves visibility, enhances resource utilization, and minimizes the risk of bottlenecks shifting due to excessive inventory buildup.
Scheduling and Sequencing at the Constraint (Drum)
At the heart of the Drum-Buffer-Rope methodology lies the scheduling and sequencing of work at the constraint or drum.
Since the constraint dictates the overall throughput of the system, it is crucial to optimize its utilization and prioritize work effectively.
Scheduling at the drum typically involves determining the sequence in which jobs or products should be processed to meet due dates, minimize setups, or optimize resource utilization.
Various techniques, such as finite scheduling, critical ratio scheduling, or prioritization based on buffer status, can be employed to develop an effective schedule for the constraint.
Buffer Sizing and Buffer Management Techniques
Effective buffer management is essential for the successful implementation of the Drum-Buffer-Rope methodology.
Buffers act as shock absorbers, protecting the constraint from variability in upstream processes and ensuring a continuous flow of work.
Buffer sizing is a critical aspect of buffer management, as buffers that are too small may fail to provide adequate protection, while excessively large buffers can lead to excessive inventory and associated costs.
Several techniques, such as simulation modeling, historical data analysis, and variability studies, can be employed to determine optimal buffer sizes.
Once buffer sizes have been established, buffer management techniques become crucial for monitoring and controlling buffer levels.
Common techniques include buffer status monitoring, root cause analysis for buffer penetrations, and dynamic buffer resizing based on changing conditions.
Advanced buffer management techniques, such as load-based buffer management and time-based buffer management, can further enhance the effectiveness of Drum-Buffer-Rope by adapting buffer sizes and priorities to fluctuations in demand, resource availability, and process variability.
Drum Buffer Rope (DBR) and Lean Manufacturing Integration
The Drum-Buffer-Rope methodology seamlessly integrates with the principles of Lean Manufacturing, creating a powerful synergy that drives waste elimination and continuous improvement efforts.
Lean Manufacturing, with its focus on identifying and eliminating non-value-added activities, provides a complementary framework for optimizing processes and enhancing flow.
By implementing Drum-Buffer-Rope (DBR), organizations can effectively identify and manage constraints, which often represent sources of waste and inefficiency within the value stream.
The systematic approach of DBR, combined with Lean tools such as value stream mapping, 5S, and kaizen events, enables organizations to continuously improve their operations, reduce lead times, and eliminate waste.
Kanban system and CONWIP system comparison
While the Drum-Buffer-Rope methodology shares similarities with other pull production systems, such as Kanban and CONWIP (Constant Work-in-Process), there are distinct differences that set Drum-Buffer-Rope (DBR) apart.
In a Kanban system, the flow of work is controlled by a fixed number of signals or kanban cards, limiting the work-in-process (WIP) at each stage of the process.
CONWIP, on the other hand, controls the total WIP in the entire system, allowing greater flexibility in the distribution of work across different stages.
Drum-Buffer-Rope (DBR), however, takes a more targeted approach by explicitly focusing on the constraint or bottleneck within the system.
Rather than controlling WIP at each stage or across the entire system, Drum-Buffer-Rope manages the flow of work to and from the constraint, ensuring that the constraint is never starved or blocked.
Six Sigma and Variability Management
Six Sigma, a widely adopted methodology for process improvement and defect reduction, plays a crucial role in the successful implementation and ongoing optimization of the Drum-Buffer-Rope system.
By employing Six Sigma tools and techniques, organizations can effectively manage variability, a key challenge in any production environment.
The DMAIC (Define, Measure, Analyze, Improve, Control) problem-solving methodology of Six Sigma provides a structured approach to identifying and addressing the root causes of variability that can impact buffer levels and constraint performance.
Statistical analysis tools, such as control charts, process capability studies, and design of experiments, can be leveraged to quantify and reduce variability, leading to more accurate buffer sizing and improved throughput.
Advanced Drum Buffer Rope (DBR) Concepts and Applications
While the traditional Drum-Buffer-Rope methodology focuses on managing internal constraints within a production system, the Simplified Drum-Buffer-Rope (S-DBR) approach recognizes the market or customer demand as the ultimate constraint.
In many cases, organizations have sufficient capacity to meet customer demand, making the market the true bottleneck that limits their throughput.
S-DBR operates under the assumption that the system’s capacity exceeds the market demand, at least on average.
In this scenario, the drum is set to the maximum rate at which the organization can deliver products or services to the market, effectively synchronizing production with customer demand.
Instead of maintaining separate buffers for each internal constraint, S-DBR employs a single shipping buffer to protect due dates and ensure on-time delivery.
This buffer acts as a time cushion, accommodating variability in lead times and allowing the organization to prioritize work based on due dates and buffer status.
The rope mechanism in S-DBR controls the release of new work into the system, ensuring that raw materials or components are introduced at the appropriate time to meet the scheduled delivery dates, without excessive inventory buildup or risk of starvation.
S-DBR can be particularly beneficial for organizations operating in highly competitive markets, where meeting customer expectations and delivering on time are critical success factors.
By aligning production with market demand and focusing on due-date performance, S-DBR enables organizations to enhance customer satisfaction and maintain a competitive edge.
Future Outlook
As the fourth industrial revolution continues unfolding, integrating emerging technologies with the Drum-Buffer-Rope methodology presents exciting potential for further optimization and enhanced operations.
Advances in areas like the Internet of Things, artificial intelligence, and analytics could revolutionize how Drum-Buffer-Rope (DBR) is applied and overseen.
IoT sensors and real-time data systems may provide unprecedented visibility into production, enabling more accurate constraint identification and dynamic buffer changes based on real-time inputs.
AI and machine learning algorithms could analyze complex patterns, foresee potential disruptions, and optimize scheduling and sequencing at constraints.
This enhances Drum-Buffer-Rope (DBR) systems’ responsiveness and adaptability overall.
By embracing ongoing learning and leveraging abundant educational resources, individuals and organizations can successfully navigate Drum-Buffer-Rope (DBR) implementation complexities.
They can continually enhance their processes and drive lasting operational excellence. The future remains bright for this methodology to adapt and advance and help drive performance to new heights.
SixSigma.us offers both Live Virtual classes as well as Online Self-Paced training. Most option includes access to the same great Master Black Belt instructors that teach our World Class in-person sessions. Sign-up today!
Virtual Classroom Training Programs Self-Paced Online Training Programs