All about Quality Control Management in Lean Six Sigma
Consistently delivering high-quality products or services is a must to succeed.
Customers expect reliability, dependability, and adherence to what’s promised, making quality management so crucial to operations.
It’s an all-encompassing method involving processes, techniques, and tools aimed at ensuring things meet predefined quality standards and customer needs.
Quality control management is systematic yet flexible, centering around preventing defects, identifying and solving issues, and constantly upgrading approaches to enhance quality overall.
It demands careful planning, vigilant monitoring, thorough inspections, and adjustments to keep quality as it should be at all times.
By properly implementing quality control management, organizations can minimize mistakes, cut down on waste, boost efficiency, and ultimately improve the customer experience.
This proactive stance not only safeguards a company’s reputation but also feeds into savings, higher productivity, and competitive advantage in the market. It’s a win all around.
Key Highlights
- Quality control management is crucial for making sure things meet the expected quality levels and specifications. It revolves around putting systematic methods, tools, and techniques into practice to monitor, inspect, and upgrade quality.
- Effective quality management helps companies provide steady quality, cut down on defects, and boost customer satisfaction. Some major parts include quality planning, process control, inspection, audits, and constant upgrading.
- Quality control management is vital across many industries, whether manufacturing or services, to stay competitive and compliant with regulations. From car makers to software firms to healthcare providers, maintaining quality is essential through careful management.
- It allows organizations in all kinds of fields, from automotive to technology to medical, to deliver for customers consistently while also future-proofing the business through overseeing processes and continuously strengthening what’s offered. Quality control is a must-have wherever quality matters.
What is Quality Control Management?
Quality control management refers to making sure things are made right and stay consistent. It involves monitoring every step of the process to spot defects or issues and then taking action to maintain the right quality levels.
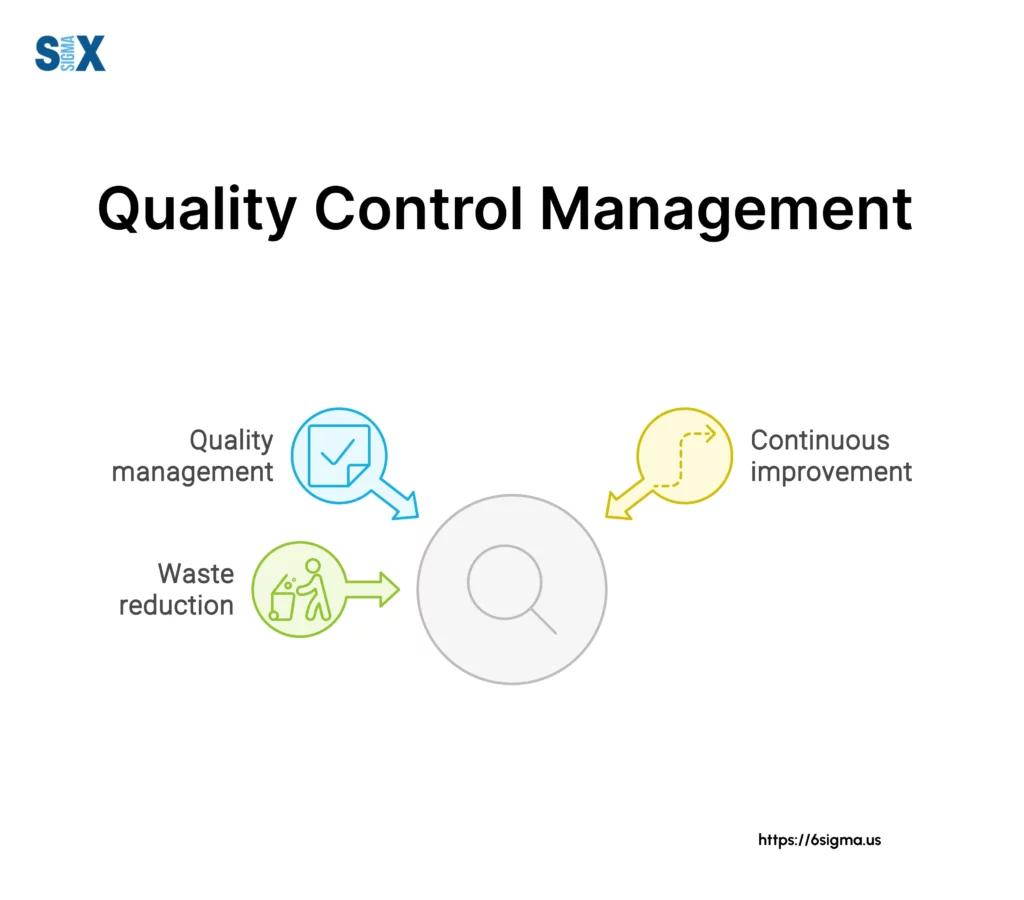
Quality has become hugely important for all sorts of businesses today. Those who don’t properly manage quality risk hurting their brand, losing customers, running into legal trouble, and wasting resources fixing problems.
Effective quality control management helps organizations provide steady quality, cut costs from waste and re-work, and improve customer satisfaction.
The core goal is to catch any issues or non-compliance as early on as possible. This prevents defective products from reaching people. It includes setting acceptable standards, inspecting quality at each stage, and analyzing data to spark improvements.
Some fundamental aspects are nailing down quality benchmarks, choosing suitable quality control management methods and tools, assigning clear roles and responsibilities, ensuring everyone gets quality training, keeping documentation, and cultivating a drive for continuous upgrading.
Quality Control Processes and Methods
Quality control involves a set of processes and methods that organizations implement to ensure their products or services meet defined standards and requirements.
These processes and methods aim to identify and address any defects, errors, or issues that could impact the quality of the final output. Common quality control processes and methods include:
Inspection: This involves examining products or services at various stages of production or delivery to check for compliance with specifications. Inspections can be conducted manually or using automated systems, depending on the industry and complexity of the product/service.
Statistical Process Control (SPC): SPC is a methodology that uses statistical techniques to monitor and control a process. It involves collecting and analyzing data from the process to identify variations and take corrective actions when necessary.
Sampling: In cases where inspecting every unit is impractical or too costly, organizations may use sampling techniques. This involves selecting a representative sample of units from a batch or lot and inspecting them for quality.
Audits: Quality audits are systematic evaluations of processes, products, or services to determine their conformance to established standards and requirements. Audits can be internal (conducted by the organization) or external (conducted by third-party auditors).
Testing: Various testing methods, such as functional testing, performance testing, and stress testing, are used to evaluate the quality of products or services under different conditions and scenarios.
Root Cause Analysis (RCA): When quality issues or defects are identified, RCA is a structured approach to identify the underlying causes and implement corrective and preventive actions.
Quality Control Tools: Several tools and techniques are used in quality control, such as control charts, cause-and-effect diagrams (fishbone diagrams), Pareto charts, and process mapping, to analyze data, identify patterns, and solve problems.
By implementing these quality control processes and methods, organizations can ensure that their products or services meet customer expectations, comply with regulatory requirements, and maintain a competitive edge in the market.
What is Quality Control Management & How to Implement It?
Implementing an effective quality control management system requires careful planning and execution across an organization. There are several key steps involved:
Define Quality Standards
The first step is clearly defining what quality standards products or services need to meet. This could involve specifications around materials, components, processes, functionality, durability, and other criteria.
Quality standards should align with customer expectations, regulatory requirements, and industry best practices.
Establish Quality Control Procedures
With standards defined, the next step is to establish procedures for ensuring those standards are met consistently. This includes specific quality control methods like inspection, testing, auditing, and documentation requirements.
Quality control procedures should cover all stages of production from sourcing raw materials to final assembly/delivery.
Deploy Quality Control Tools & Techniques
Many tools and techniques can be leveraged as part of a quality control management program, such as statistical process control, Six Sigma, failure mode and effects analysis, and quality control charts.
The appropriate tools will depend on the products/services and the types of quality issues being monitored.
Implement Quality Management System
A formal quality management system (QMS) should be implemented to oversee all quality policies, processes, procedures, responsibilities, and resources.
This could involve getting certified against standards like ISO 9001. A QMS provides the infrastructure for effective quality planning, assurance, control, and improvement.
Provide Quality Training
All employees involved in quality control activities need to be properly trained on relevant procedures, tools, systems, and requirements.
This will help ensure quality processes are executed consistently and correctly. Quality training should be an ongoing process to reinforce best practices.
Monitor Quality Performance
Once quality processes are implemented, their performance should be continuously monitored through metrics, audits, and reviews. This data can identify areas of strength, opportunities for improvement, and any emerging quality issues that need to be addressed promptly.
Foster a Quality Culture
Ultimately, quality needs to be ingrained into the culture and mindset across the organization – not treated as an isolated program. By getting buy-in and promoting quality as a shared responsibility, it becomes a sustainable competitive advantage.
Quality Control in Different Industries
Quality control management looks different across various industries, as the processes, standards, and requirements can vary significantly.
However, the core principles of quality control management remain the same – ensuring products or services meet established standards and requirements through systematic monitoring, testing, and improvement.
Manufacturing
In the manufacturing sector, quality control is crucial for producing safe, reliable, and high-quality products. Quality control processes involve thorough inspections at every stage, from incoming raw materials to final product testing.
Statistical process control methods are commonly used to monitor production processes and identify any deviations from specifications. Failure testing, such as stress testing or environmental simulation, ensures products can withstand real-world conditions.
Healthcare
Quality control in healthcare is a matter of life and death. Healthcare organizations implement rigorous quality control measures to ensure patient safety, accurate diagnoses, and effective treatments.
This includes strict protocols for sterilization, medication dispensing, laboratory testing, and medical device performance. Regular audits, staff training, and continuous process improvement are essential for maintaining high standards of care.
Food and Beverage
Food safety is the top priority in the food and beverage industry’s quality control management efforts. Hazard Analysis and Critical Control Points (HACCP) is a widely used system to identify and mitigate potential food safety hazards.
Quality control procedures include strict hygiene practices, temperature monitoring, ingredient inspections, and microbiological testing. Labeling accuracy and adherence to dietary regulations are also key quality control areas.
Construction
In the construction industry, quality control management focuses on ensuring buildings and infrastructure projects meet design specifications, safety codes, and durability requirements.
Quality control inspections occur at various milestones, such as foundation pouring, framing, electrical and plumbing installations, and final walkthroughs. Testing of materials, soil conditions, and structural integrity are also part of the quality control process.
Software and IT
For software and IT companies, quality control revolves around software testing, bug fixing, and user experience optimization. Quality assurance teams employ various testing methodologies, such as unit testing, integration testing, system testing, and user acceptance testing.
Performance monitoring, security testing, and compatibility checks across different platforms and devices are also critical quality control measures.
Continuous Improvement and Best Practices to Quality Control Management
Quality control management is an ongoing process that requires continuous monitoring, evaluation, and improvement.
Even the best quality control plans can become outdated or inefficient over time as products, processes, and requirements evolve. Adopting a mindset of continuous improvement is critical for long-term quality management success.
Some best practices for enabling continuous quality improvement include:
Regular Review and Adjustment
Periodically review all quality control processes, procedures, metrics, and documentation. Identify areas that need updating based on changing business needs, new regulations, technological advancements, or opportunities for optimization. Adjust the quality management system accordingly.
Employee Training and Feedback
Ensure all employees involved in quality roles receive ongoing training on the latest quality control processes, tools, and requirements. Encourage them to provide feedback and suggestions for improving the quality system based on their hands-on experience.
Management Support and Resource Allocation
Gain full buy-in and support from upper management for continuous improvement initiatives. Ensure adequate resources like budget, personnel, and tools are allocated for optimizing quality control management efforts.
Lean and Six Sigma Principles
Leverage lean manufacturing and Six Sigma principles and methodologies to systematically identify and eliminate waste, variations, and defects in processes. Implement kaizen events for rapid quality improvement.
Quality Data Analysis
Capture and analyze relevant quality control metrics and data to identify trends, root causes of issues, and opportunities for enhancement. Tools like statistical process control can provide insights.
Benchmarking and Best Practice Adoption
Research quality management best practices in your industry and from leading companies. Benchmark your performance against them and adopt techniques that could improve your operations.
By embracing continuous improvement as a core tenet of their quality approach, organizations can stay agile, relevant, and competitive while delivering consistently high-quality products and services. An unwavering commitment to optimizing quality processes is essential.
Conclusion
Quality control management is an essential process for any organization that wants to deliver high-quality products or services consistently.
By implementing robust quality control procedures, techniques, and systems, businesses can identify and address issues before they reach customers. This helps build brand reputation, customer satisfaction, and loyalty.
While quality control management requires an upfront investment of time, resources, and costs, the long-term benefits massively outweigh the initial efforts.
Organizations that neglect quality control face risks like returns, reworks, recalls, fines, and ultimately, loss of business. Embracing quality control management is the key to continuously improving processes and outputs.
As businesses face increasing competition and customer expectations, quality can be the differentiating factor. Implementing best practices like regular audits, data-driven metrics, employee training, and cutting-edge quality control software can provide that critical competitive edge.
Organizations must view quality control not just as a check-box, but as a crucial strategy for sustainable growth and success.
The road to effective quality management starts with a commitment from leadership and a culture that values getting things right the first time.
With the right quality control plan, processes, and mindset in place, businesses can deliver exceptional products and services consistently to their delighted customers.
SixSigma.us offers both Live Virtual classes as well as Online Self-Paced training. Most option includes access to the same great Master Black Belt instructors that teach our World Class in-person sessions. Sign-up today!
Virtual Classroom Training Programs Self-Paced Online Training Programs