Lean Management Tools. All the Tools You Need to Achieve Six Sigma
Associations consistently search for approaches that streamline cycles, improve profitability, and convey premium estimations to clients.
Advancement originated from Toyota’s creation framework where discharge, non-ending upgrades, and regard drive viability. These standards bypass assembling impacts over social insurance, programming, development, and administration vitally.
Lean instruments consolidate methodologies upgrading viability by recognizing and expelling non-valuable exercises while encouraging consistent learning society.
Fundamental 5S to progressed techniques like value stream mapping and kanban give apparatuses for achievement universally accessible and focused upper hands maintainable.
Key Highlights
- Advanced instruments speak to an accumulation of procedures improving cycle streamlining, squandering evacuation, and viability for associations.
- These devices emerged from Toyota’s assembling framework accessing assembling, social insurance, programming, administration, and construction.
- Fundamental devices incorporate 5S, value stream mapping, kaizen, kanban, poka-yoke, and visual board. Devices are categorized as process refining, work process and timetables, quality, and continuing upgrades, or industry-substantial.
- Successful usage needs a way of life changes, authority duty, laborer preparation, and an unending upgrade mentality.
What are Lean Management Tools?
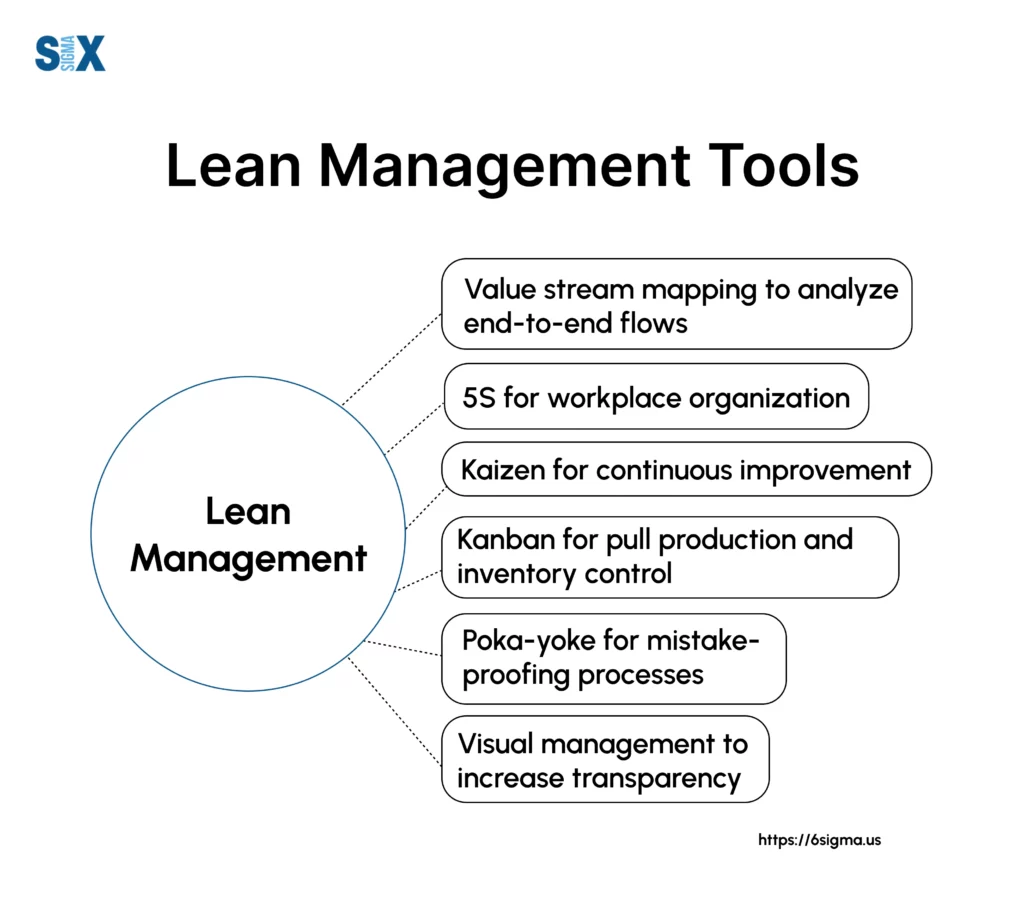
An advanced association persistently improves by streamlining cycles, expelling non-esteem exercises, abbreviating cycle times, evacuating hindrances, and empowering laborers.
To fruitfully execute lean considering and drive non-ending upgrades, associations utilize an assortment of devices and procedures. These recognize open doors, dissect cycles, settle issues, actualize arrangements, and uphold additions.
Basic lean management tools incorporate value stream mapping, 5S, kaizen, kanban, poka-yoke, and visual board. Particular lean devices spotlight quality, work habitats, item advancement, and graceful chains.
When connected stringently through administration duty and laborer joining, lean instruments enable gatherings to streamline persistently.
Fundamental Lean Management Tools
At the core of lean management tools are several fundamental tools and concepts that drive continuous improvement and waste reduction. These lean management tools tools form the foundation for implementing lean principles across an organization.
5S
The 5S methodology refers to five Japanese principles for organizing workspaces for efficiency and effectiveness: sort, straighten, shine, standardize, and sustain. Implementing 5S helps eliminate waste from disorganization, clutter, and excessive motion.
Value Stream Mapping
Value stream mapping is a lean technique that visually maps the flow of materials and information in a process.
It helps identify waste and opportunities for streamlining. Creating a current state map and a future state map allows organizations to design an improved future workflow.
Kaizen
Kaizen is the philosophy of continuous, incremental improvement. It encourages small, ongoing positive changes in processes and products. Kaizen events gather employees to identify opportunities and implement lean solutions quickly.
Gemba Walks
A Gemba walk involves going to the actual workplace or “Gemba” to observe processes firsthand. Managers can see wastes and inefficiencies that may be harder to recognize from their offices. Gemba walks connect leaders to frontline realities.
Root Cause Analysis
Many lean problem-solving methods like 5 Whys and fishbone diagrams focus on thoroughly investigating to uncover the true root causes of issues rather than just addressing surface symptoms. Permanently eliminating root causes prevents recurring problems.
Lean Management Tools for Process Improvement
Lean philosophy emphasizes continuous improvement and elimination of waste in processes. Several lean tools are specifically geared towards analyzing, optimizing, and improving processes. Some key lean process improvement tools include:
Value Stream Mapping
Value stream mapping is a lean technique used to visually map the flow of materials and information required to bring a product or service to the customer. It helps identify waste and inefficiencies in the current state and design a future state with an optimized flow.
Kaizen
Kaizen refers to the philosophy of continuous, incremental improvement. Kaizen events are focused workshops where teams come together to analyze a process and implement improvements immediately. Tools like process mapping, 5 Whys, and PDCA cycle support kaizen.
5S
5S (Sort, Straighten, Shine, Standardize, Sustain) is a lean tool to create and maintain an organized, clean, and efficient workplace. It eliminates sources of waste and non-value-adding activities.
Root Cause Analysis
Tools like 5 Whys, fishbone diagrams, and fault tree analysis help identify the root causes behind process problems or inefficiencies. Addressing root causes leads to more effective and sustainable solutions.
PDCA Cycle
The Plan-Do-Check-Act (PDCA) cycle is an iterative approach for continually improving processes. It involves planning improvements, executing changes, checking results, and acting to standardize or further improve.
Lean Management Tools for Workflow and Scheduling
Efficient workflow and scheduling are critical for any lean organization. Lean provides several powerful tools to streamline processes, reduce waste, and improve flow. Some key lean tools for optimizing workflows and schedules include:
Kanban
The kanban system is one of the visual lean management tools that helps manage the flow of work. It uses visual signals like kanban cards or boards to track work items through the various stages of a process.
Kanban makes bottlenecks and constraints highly visible so they can be addressed. It also helps limit work-in-progress to optimize flow.
Heijunka (Production Leveling)
Heijunka is the practice of leveling out the production schedule to match demand as closely as possible.
This reduces batching and allows for a more consistent, level flow of work. Heijunka tools like heijunka boxes and load leveling charts help create a repeatable schedule that avoids overburden.
Takt Time
Takt time is the maximum time allowed to produce one unit of product to meet customer demand. Calculating and adhering to takt time ensures you produce only what is required by customers and avoids overproduction waste.
SMED (Single Minute Exchange of Die)
SMED is a lean technique to dramatically reduce changeover times between production runs. Faster changeovers enable smaller batch sizes and more flexibility to match production with demand fluctuations.
5S Workplace Organization
An organized, clean workplace is essential for efficient flow. 5S (sort, straighten, shine, standardize, sustain) provides methods to create and maintain an orderly work environment that supports smooth operations.
Lean Management Tools for Quality and Continuous Improvement
A core principle of lean management is the relentless pursuit of perfection through continuous improvement. Lean provides a robust set of tools to help organizations improve quality and drive ongoing optimization. Some key lean tools in this area include:
Poka-Yoke
Poka-yoke, which means “mistake-proofing” or “inadvertent error prevention”, refers to any mechanism that helps prevent mistakes from occurring in a process.
Poka-yoke can involve low-cost physical devices like guides or fixtures, as well as procedural solutions like checklists. Implementing poka-yoke helps catch defects at the source before they can propagate.
Jidoka
Jidoka, which means “automation with a human touch“, is the principle of granting machines and operators the ability to stop production whenever an abnormality is detected.
This prevents passing on defects downstream. Jidoka tools include autonomous defect control methods, error-proofing sensors, and the andon system for alerting about problems.
Kaizen
Kaizen is the practice of continuous, incremental improvement involving everyone from CEO to frontline workers. Lean kaizen tools include kaizen events/blitzes, suggestion systems, and quality circles where teams identify opportunities and implement lean solutions.
5 Whys
The 5 Whys is an iterative root cause analysis technique used to identify the origin of a problem by asking “why?” at least five times. It is a fundamental lean problem-solving tool that prevents just addressing surface-level symptoms.
Visual Management
Lean visual management tools like value stream maps, Kanban boards, andons, and heijunka boxes make the status and flow of work visible to drive process improvement. Abnormalities are easily spotted and remedied before more issues accumulate.
Lean Management Tools for Specific Industries
While the core lean principles and many lean tools are applicable across various industries, certain industries have developed specialized lean tools tailored to their unique processes and environments. Here are some examples:
Lean Manufacturing Tools
As lean originated in the manufacturing sector, there are several lean tools specifically designed for optimizing manufacturing processes:
- Value Stream Mapping (VSM) – Visually maps the flow of materials and information to identify waste and opportunities for improvement.
- Cellular Manufacturing – Reorganizes the factory layout into cells dedicated to families of products to improve flow.
- Total Productive Maintenance (TPM) – A system to maximize equipment effectiveness through better maintenance practices.
- Single Minute Exchange of Dies (SMED) – Techniques to reduce changeover times on production equipment.
Lean Healthcare Tools
Lean has been widely adopted in healthcare to improve patient flow, safety, and quality of care. Some common lean healthcare tools include:
- 3P (Production Preparation Process) – Engages all stakeholders in designing an ideal future state for a new process or product.
- 5S Audit for Hospitals – Adapts the 5S workplace organization method for clinical areas like patient rooms and operating rooms.
- Nursing Lean Tools – Spaghetti diagrams, load leveling, and visual controls tailored to nursing workflows.
Lean Construction Tools
The lean construction toolbox contains methods like:
- Last Planner System – Collaborative planning system that involves workers in lookahead planning to improve workflow reliability.
- Kanban for Construction – Visualizes workflow with cards representing construction tasks progressing across a board.
- Takt Planning – Synchronizes workflow and labor by defining the “takt” time to match available resources.
By utilizing lean tools specific to their industry, organizations can better apply lean thinking to their particular processes and environments. The key is selecting the right tools and properly training staff on their use.
Implementing Lean Management Tools: Best Practices
Start with a lean assessment and identify opportunities
- Map out current processes and workflows
- Identify areas of waste, inefficiency, or quality issues
- Prioritize areas for lean implementation based on impact
Get buy-in and involve employees at all levels
- Lean is a cultural transformation, not just a process improvement
- Provide training on lean principles and tools
- Encourage employee engagement and continuous improvement ideas
Take an iterative approach
- Start with pilot projects or model areas
- Analyze results and adjust approach as needed
- Implement tools across the organization incrementally
Use lean data for monitoring and driving improvement
- Establish lean metrics and KPIs to track progress
- Leverage visual management for transparency
- Conduct regular Gemba walks and kaizen events
Sustain lean through leadership and daily practices
- Leaders must reinforce lean behaviors and mindsets
- Make lean part of standard operating procedures
- Celebrate successes and continue striving for perfection
SixSigma.us offers both Live Virtual classes as well as Online Self-Paced training. Most option includes access to the same great Master Black Belt instructors that teach our World Class in-person sessions. Sign-up today!
Virtual Classroom Training Programs Self-Paced Online Training Programs