Cycle Time vs Throughput Time. All You Need to Know
Efficiency and output emerge as hugely consequential in manufacturing and creation. Critical estimations conveying functional awareness incorporate cycle time and throughput time.
While regularly mistakenly utilized reciprocally, they speak to clear theories basic for comprehending and enhancing business presentation.
Cycle time, otherwise called handling time or running time, totals the period from one cycle or unit beginning until ends, discounting holds or lines.
Then again, throughput time, likewise termed lead time or full cycle time, estimates the aggregate timeframe from starting a thing or administration until ends, remembering any pausing or lines.
Distinguishing these supplies cleared perspectives since cycle time spotlights individual gearing while throughput time considers the entire frameworkās progression and likely hindrances.
Through understanding and enhancing both, makers gain important awareness of operations, distinguish update territories, and actualize procedures expanding profitability, diminishing waste, and expanding client joy.
Key Highlights
- Cycle time and throughput time rank high in manufacturing and output estimations, despite estimating various parts.
- Cycle time speaks to finishing one gearing or item creation, while throughput time steps aggregate time from initial to last assignment highlights.
- Understanding separates these estimations remains basic for refining assignments, hindrance distinguishing, and general productivity enhancing.
- Variables like procedure intricacy, asset accessibility and instability altogether influence cycle and throughput times.
- Systems like lean manufacturing, cycle time shortening methods, and throughput advances can further develop measurements and support profitability.
- Tracking cycle and throughput statistics give significant bits of knowledge for proceeding with betterments and achieving great operational executions.
What is Cycle Time and Throughput Time?
For makers and makers, two central estimations quantify viability and procedure streamlining – cycle time and throughput time.
While regularly mistakenly utilized reciprocally, they allude to particular standards imperative for evaluating and improving operational execution.
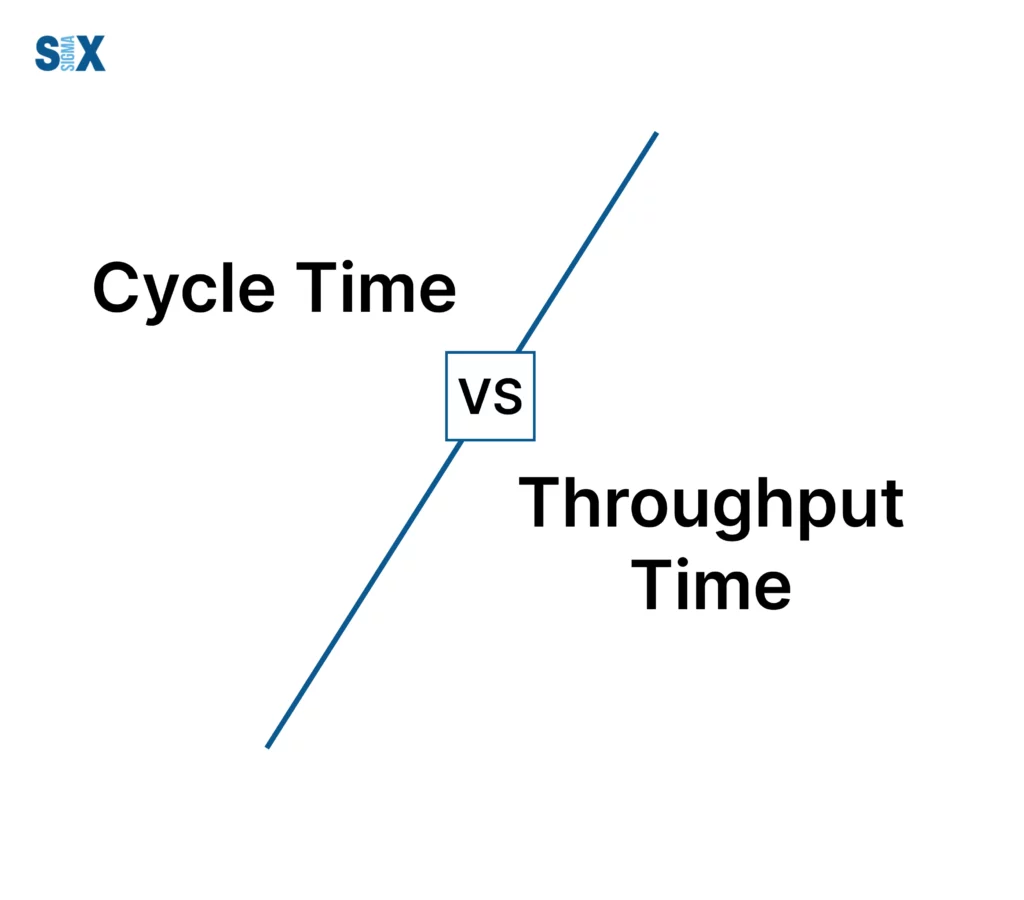
Cycle time, otherwise called creation cycle time or fabricating procedure time, remains the aggregate expected finishing one cycle. It incorporates activity starting till ready for the following stage.
Throughput time speaks to the aggregate from preliminary contribution till the last yield. It remembers latent, holding up, and transport times between tasks.
Cycle time centrality spotlights group efficiencies while throughput time supplies a total perspective of the creation stream.
By breaking down and enhancing both, organizations can recognize hindrances, streamline cycles, and build productivity and profitability.
Calculating Cycle Time vs Calculating Throughput Time
To accurately measure and compare cycle time vs throughput time, it is crucial to understand how each metric is calculated.
Cycle Time Calculation
Cycle time refers to the total time it takes to complete one cycle of an operation or process from start to finish. It is calculated by measuring the time elapsed from when a unit begins processing until it is finished and ready for the next step. The cycle time calculation is:
Cycle Time = Total Time Elapsed / Total Units Processed
For example, if a manufacturing process takes 20 hours to produce 100 units, the cycle time would be 20 hours / 100 units = 0.2 hours per unit.
Throughput Time Calculation
Throughput time, also known as lead time or total cycle time, represents the total time for a unit to travel through an entire process or value stream from start to finish. It includes process time as well as wait time and queue time between process steps. The throughput time calculation is:
Throughput Time = End Time – Start Time for the Full Process
Using the previous example, if the 100 units were released at 8 am and the last unit was completed at 4 pm, the throughput time would be 4 pm – 8 am = 8 hours for the full process run.
Monitoring both cycle time and throughput time provides a more comprehensive view of process performance. While cycle time focuses on the actual processing time, throughput time accounts for all delays, bottlenecks, and sources of waste impacting flow through the entire value stream.
Factors Affecting Cycle Time and Throughput Time
Several key factors can impact both cycle time and throughput time in a manufacturing or production environment. Understanding these factors is crucial for optimizing processes and improving overall efficiency.
Equipment and Technology
The type of equipment and level of technology used can significantly influence cycle times. Older, less automated equipment may require more manual handling, leading to longer cycle times. Investing in newer, more advanced machinery can help streamline processes and reduce cycle times. However, it’s important to balance the investment costs against the potential throughput gains.
Worker Skills and Training
Well-trained workers with the right skills can operate equipment more efficiently, reducing unnecessary delays or errors that extend cycle times. Proper training on processes, equipment operation, and quality checks is essential. Cross-training workers can also help improve flexibility and throughput.
Process Design and Layout
The design of the manufacturing processes themselves, as well as the physical layout of the production line or facility, can impact cycle times. Inefficient processes with redundant steps or poor ergonomics will inherently have longer cycle times. Analyzing process flows and facility layouts to minimize motion waste and maximize efficiency is key.
Material Handling and Logistics
How raw materials, work-in-process items, and finished goods are handled and transported can be a bottleneck. Delays in material delivery, storage issues, or excessive travel distances may unnecessarily extend cycle times. Optimizing material flows and logistics is important for throughput.
Quality Control Procedures
While essential, overly complex or redundant quality inspections can increase cycle times. Finding the right balance between quality checks and cycle time/throughput is important. Using in-line or automated inspection methods can help.
Demand Variability and Scheduling
Fluctuations in product demand and suboptimal production scheduling can lead to inefficiencies like production bottlenecks, downtime, or changeovers that negatively impact throughput time. Effective demand forecasting and scheduling are needed.
Improving Cycle Time vs Improving Throughput Time
Enhancing cycle time and throughput time is a key focus area for manufacturers looking to increase productivity and efficiency. Several strategies can be employed to reduce cycle times and boost throughput rates:
Eliminate Waste and Non-Value Added Activities
Lean manufacturing principles emphasize identifying and eliminating wasteful activities that don’t add value from the customer’s perspective.
Activities like unnecessary motion, waiting times, overproduction, and excess inventory can significantly increase cycle times. Streamlining processes by removing these non-value-added steps is essential.
Implement Cycle Time Reduction Techniques
There are specific lean tools aimed at reducing cycle times, such as:
- Single Minute Exchange of Dies (SMED) for quicker changeovers
- Cellular manufacturing and line balancing to optimize flow
- Mistake-proofing (poka-yoke) to prevent errors and rework loops
- 5S workplace organization for efficiency
Optimize Equipment and Technology
Investing in new equipment, automation, and digital technologies like manufacturing execution systems (MES) can drive major cycle time improvements. Preventive maintenance also reduces unplanned downtime.
Focus on Constraint Management
Theory of Constraints emphasizes managing bottlenecks – the processes limiting overall throughput. Systematically identifying and improving these constraints lifts throughput.
Empower Workforce Continuous Improvement
Engaging operators and providing training on lean tools and continuous improvement concepts like kaizen cultivates a culture focused on incrementally enhancing cycle times.
Cycle Time vs Throughput Time: Applications and Benefits
Cycle time and throughput time are critical metrics in manufacturing and production environments. Understanding and optimizing these measures can provide significant applications and benefits:
Applications of Cycle Time vs Throughput Time
- Production Planning and Scheduling: Cycle time and throughput data enables better production planning to meet customer demand while maximizing resource utilization.
- Supply Chain Management: These metrics help synchronize material flow with manufacturing cycles to reduce inventory costs.
- Process Improvement: Analyzing cycle times and bottlenecks leads to opportunities for process improvements through lean manufacturing, automation, etc.
- Financial Modeling: Throughput time projections allow for more accurate financial forecasting of production output and revenue.
- Staffing and Capacity Planning: Cycle time benchmarks indicate labor requirements and capacity needs.
Benefits of Cycle Time vs Throughput Time
- Increased Productivity: Reducing cycle times and eliminating bottlenecks directly increases the rate of production throughput.
- Cost Savings: Higher throughput with lower cycle times means better utilization of resources, less inventory, and lower operating costs.
- Improved On-Time Delivery: Optimized throughput time helps ensure production meets demand and delivery commitments.
- Better Quality Control: Monitoring cycle time variations allows early detection and correction of process issues impacting quality.
- Competitive Advantage: Efficient cycle times and maximum throughput increase profitability and competitiveness.
- Customer Satisfaction: Faster cycle times facilitate shorter lead times, keeping customers happier with on-time deliveries.
By leveraging cycle time and throughput time as key performance indicators, manufacturers can drive operational excellence across their production systems. The insights from analyzing these metrics unlock opportunities for creating leaner, more cost-effective, and more agile operations.
Best Practices and Examples
One key best practice is to implement lean manufacturing principles and techniques like value stream mapping to identify and eliminate non-value-added activities that increase cycle times. Applying methods like continuous flow, kanban systems, and heijunka (production leveling) can also help optimize cycle times.
Another best practice is using real-time data tracking and monitoring of cycle times and throughput rates across all process steps.
Modern manufacturing execution systems (MES) provide this capability. Having transparency into bottlenecks, constraints, and sources of variability allows manufacturers to respond quickly and improve.
Conducting cycle time studies by having operators break down processes into constituent steps and timing each one is also recommended. This granular view exposes opportunities for kaizen or cycle time reduction projects.
Toyota’s legendary Toyota Production System pioneered many of the cycle time management practices used today. Techniques like one-piece flow, autonomation, and stopping to fix problems enabled Toyota to achieve superior productivity and quality levels.
Aerospace manufacturers like Boeing closely monitor cycle times during aircraft assembly to achieve on-time deliveries. Strategies like moving assembly lines, point-of-use inventory, and U-shaped line designs are utilized to streamline cycle times.
Pharmaceutical companies are laser-focused on optimizing throughput times for drug manufacturing processes. Their high-value product portfolios and strict regulatory environment make efficient throughput essential. Statistical process control, automation, and digital integration of manufacturing systems are common practices.
Cycle Time vs Throughput Time: The Future Outlook
Understanding the difference between cycle time and throughput time is crucial for optimizing manufacturing processes and improving overall operational efficiency.
Cycle time measures the time required to complete an individual unit or task, while throughput time represents the total time it takes to move one unit from the beginning to the end of the entire production process.
By closely monitoring and analyzing these metrics, manufacturers can identify bottlenecks, streamline workflows, and implement targeted improvements to reduce waste, increase productivity, and enhance customer satisfaction.
Effective management of cycle time and throughput time enables organizations to respond quickly to market demands, minimize inventory costs, and maintain a competitive edge.
Looking ahead, the integration of advanced technologies, such as the Industrial Internet of Things (IIoT), big data analytics, and machine learning, is expected to revolutionize the way cycle time and throughput time are measured and optimized.
Real-time data collection and predictive analytics will provide deeper insights into production processes, enabling proactive adjustments and optimizations before issues arise.
Additionally, the adoption of lean manufacturing principles, such as just-in-time (JIT) production and continuous improvement (kaizen), will continue to play a crucial role in minimizing cycle time and maximizing throughput time.
Collaborative efforts between cross-functional teams, suppliers, and customers will further enhance supply chain visibility and synchronization, leading to more efficient material flow and reduced lead times.
As customer expectations for faster delivery and higher quality continue to rise, the importance of effectively managing cycle time and throughput time will only increase.
Manufacturers that embrace these concepts and leverage the latest technologies will be well-positioned to thrive in an increasingly competitive and dynamic market.
SixSigma.us offers both Live Virtual classes as well as Online Self-Paced training. Most option includes access to the same great Master Black Belt instructors that teach our World Class in-person sessions. Sign-up today!
Virtual Classroom Training Programs Self-Paced Online Training Programs