Mastering Process Sigma Level: Strategies for Superior Quality Outcomes
Businesses always look for ways to boost their quality while cutting defects and costs. One extremely useful methodology is Six Sigma and Process Sigma Level.
Six Sigma utilizes a full toolbox of methods and tricks to refine processes and satisfy customers better.
A big part of Six Sigma is the “Process Sigma Level” concept. This measure quantifies how able a process is to meet what customers need.
In this article, we’ll cover the process sigma level in depth. We’ll unpack how it’s calculated and its vital role in fueling constant upgrades and world-class results.
Let’s dive in and explore the nuts and bolts of Sigma Leveling and how mastering it transforms business for the better.
Key Highlights
- Understand the origins and principles of Six Sigma, and how Sigma Level serves as a cornerstone metric for process capability evaluation.
- Learn the step-by-step process for calculating Sigma Level.
- Explore the vital benefits of improving Sigma Level, such as meeting customer quality expectations, reducing defects and rework costs, and enabling continuous process improvement.
- Gain insights into the DMAIC (Define, Measure, Analyze, Improve, Control) methodology
- Discover best practices for monitoring and sustaining higher Sigma Levels.
- Benchmark your organization’s performance against industry standards, from 1 Sigma to the coveted 6 Sigma Level.
- Explore case studies of companies operating at world-class Six Sigma Level.
What is Process Sigma Level?
Businesses always look for ways to enhance the quality of their products and services while cutting defects and costs. This never-ending effort led to Six Sigma, a very useful methodology.
Six Sigma uses a full toolbox of methods and tricks to refine processes and really satisfy customers. A big part of it is the concept of “Process Sigma Level”. This measure shows exactly how capable a process is of meeting what customers need.
Understanding Six Sigma and Process Sigma Level
Six Sigma was first introduced at Motorola in the 80s to improve manufacturing and reduce flaws.
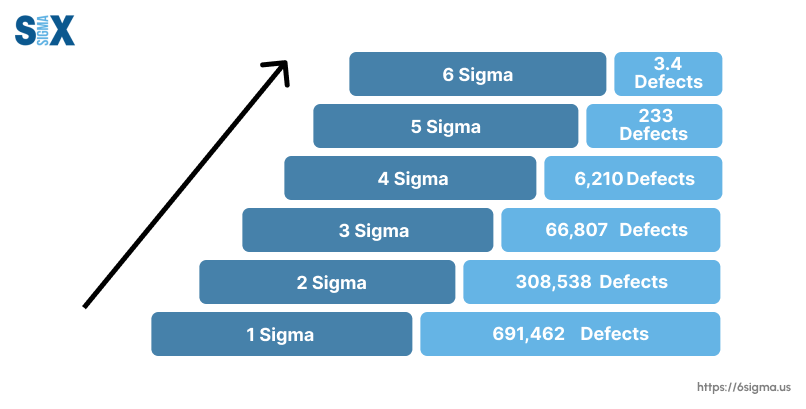
The term “Six Sigma” refers to a super high standard – only 3.4 defects happening per every million chances. Reaching this is considered world-class, like a process working perfectly.
Key ideas in Six Sigma involve using data, focusing on customers, and always improving.
Defects Per Million Opportunities (DPMO)
Defects per Million Opportunities (DPMO) is a major metric in Six Sigma. It shows the number of defects or issues observed out of every million chances for a defect, like each manufacturing step or customer interaction.
Normal Curves and Standard Deviations
In Six Sigma, process sigma level ties closely to the normal distribution curve and standard deviation concepts. The normal curve describes how data spreads out around the average, or mean. Standard deviation measures how spread out or concentrated data is around the mean.
The higher a process’s Sigma Level, the fewer defects or variations it will have. This means data clusters tightly around the mean in the acceptable customer range.
Process Capability and Customer Needs
Process capability is how consistently a process makes outputs meeting customer requirements or standards.
In Six Sigma, the Sigma Level directly measures process capability – how well a process matches what customers expect. Knowing a process’s Sigma Level shows if it can satisfy customers or needs improvement.
Calculating Your Process Sigma Level
To calculate a process’s Sigma Level, first get its Defects per Million Opportunities (DPMO). You gather defect and total opportunity data. The DPMO formula is:
DPMO = (Total Defects / Total Opportunities) x 1,000,000
Once you have DPMO, lookup tables or online tools using statistics convert it to the Sigma Level number. These account for natural data spreads over time.
For example, 3.4 DPMO is Six Sigma level, close to perfect. Long vs short-term calculations factor in natural processes drifting over longer periods.
Why is the Process Sigma Level Important?
Where customer expectations are continuously evolving, the importance of process sigma level cannot be overstated.
This powerful metric serves as a compass, guiding organizations toward achieving superior quality, driving continuous improvement, and realizing significant cost savings.
By understanding and leveraging the process sigma level, companies can unlock a wealth of benefits that directly impact their bottom line and overall competitiveness.
Benefits of Improving Sigma Level
Every successful business lies in a deep commitment to meeting and exceeding customer expectations.
The Sigma Level directly measures how well a process aligns with customer requirements, enabling organizations to identify gaps and implement targeted improvements.
By continuously striving for higher Sigma Levels, companies can enhance the quality of their products or services, fostering greater customer satisfaction and loyalty.
This, in turn, translates into increased market share, improved brand reputation, and a competitive edge within their respective industries.
Reducing defects and rework costs
Defects and non-conformances can have far-reaching consequences for businesses, including increased rework costs, diminished productivity, and potential legal liabilities.
By focusing on improving Sigma Levels, organizations can significantly reduce the occurrence of defects, minimizing the need for costly rework and product recalls.
This reduction in defects not only enhances operational efficiency but also leads to substantial cost savings, freeing up resources that can be reinvested into research and development, process improvements, or other strategic initiatives.
Enabling continuous process improvement
The Six Sigma methodology is built upon the principle of continuous improvement, and the Sigma Level serves as a powerful tool for driving this ongoing pursuit of excellence.
By regularly measuring and monitoring Sigma Levels, organizations can identify areas for improvement, implement targeted solutions, and track the effectiveness of their interventions over time.
This data-driven approach fosters a culture of continuous learning and adaptation, ensuring that processes remain agile and responsive to changing market conditions and customer demands.
Industry examples: manufacturing, healthcare, aviation
The benefits of improving Sigma Levels transcend industry boundaries. In the manufacturing sector, organizations like 3M, Dell, and Intel have leveraged Six Sigma principles to enhance product quality, reduce waste, and streamline operations.
In the healthcare industry, where patient safety is paramount, hospitals and healthcare providers have embraced Sigma Levels to minimize medical errors and improve clinical outcomes.
Understanding Your Current Sigma Baseline
Before embarking on a journey to improve Sigma Levels, it is crucial to establish a baseline by assessing the current state of your processes. This involves collecting data, calculating the Sigma Level, and identifying areas with the greatest potential for improvement.
By conducting a thorough analysis of your processes, you can pinpoint specific steps or activities that contribute to defects or non-conformances.
This targeted approach ensures that your improvement efforts are focused and impactful, maximizing the return on your investment.
Aligning process performance to business goals
Improving Sigma Levels should not be viewed as an isolated endeavor; rather, it should be closely aligned with your organization’s overarching business goals and strategic objectives.
This alignment ensures that your efforts are strategically focused and aligned with your organization’s priorities, maximizing the impact of your investments and driving tangible business results.
Assessing the cost of poor quality at different Sigma levels
One of the most compelling reasons to strive for higher process sigma level is the potential for significant cost savings.
The cost of poor quality, which includes expenses related to rework, scrap, warranty claims, and lost productivity, can be substantial, particularly at lower Sigma Levels.
By conducting a thorough cost analysis, you can quantify the financial impact of operating at various Sigma Levels and evaluate the potential return on investment (ROI) associated with improving your processes.
This data-driven approach helps to build a strong business case for Sigma Level improvement initiatives, securing buy-in from key stakeholders and ensuring that resources are allocated effectively.
Achieving Higher Process Sigma Level
Achieving higher process sigma level is a journey that requires a structured and disciplined approach.
The Six Sigma methodology provides a proven framework, known as DMAIC (Define, Measure, Analyze, Improve, Control), that guides organizations through the process of identifying opportunities, analyzing root causes, implementing solutions, and sustaining improvements.
The DMAIC Methodology for Process Improvement
The DMAIC methodology is a structured, data-driven approach that provides a roadmap for process improvement. Mastering the DMAIC framework is a core component of our six sigma green belt certification program, equipping professionals with advanced problem-solving skills. It consists of five distinct phases:
- Define: In this phase, the problem or opportunity for improvement is clearly defined, and project goals and customer requirements are established.
- Measure: The current state of the process is measured and quantified, often through the calculation of Sigma Levels and other relevant metrics.
- Analyze: Root causes of defects or process variations are identified through data analysis, hypothesis testing, and other statistical techniques.
- Improve: Solutions are developed and implemented to address the root causes and enhance process performance.
- Control: Mechanisms are put in place to monitor and control the improved process, ensuring that gains are sustained over time.
By following this structured approach, organizations can systematically identify, analyze, and address process inefficiencies, driving continuous improvement and higher Sigma Levels.
Statistical tools: Control charts, hypothesis testing
The DMAIC methodology is supported by a range of powerful statistical tools that aid in data analysis, root cause identification, and process monitoring. Control charts, for instance, are invaluable in visualizing process behavior over time and detecting deviations from expected performance.
Hypothesis testing techniques, such as t-tests and ANOVA (Analysis of Variance), help in determining the statistical significance of observed differences, guiding decision-making, and ensuring that improvement efforts are focused on genuine root causes.
These tools, combined with the structured DMAIC approach, provide a robust framework for driving sustainable improvements in Sigma Levels.
Increasing Sigma Level through DMAIC
To illustrate the power of the DMAIC methodology, let’s consider a case study from my experience at 3M. One of our manufacturing facilities was experiencing high levels of defects in the production of a critical component for automotive applications.
The process was operating at a Sigma Level of approximately 3.5, resulting in significant rework costs and customer dissatisfaction.
By following the DMAIC approach, our team first defined the problem and established project goals aligned with customer requirements (Define phase).
We then collected data and measured the current process performance, calculating the DPMO and Sigma Level (Measure phase).
In the Improve phase, we implemented solutions such as tighter raw material specifications, process parameter adjustments, and operator training. These improvements were closely monitored through control charts and statistical process control techniques (Control phase).
Monitoring and Sustaining Higher Sigma Levels
Achieving higher Sigma Levels is only the first step; sustaining these improvements over time is equally crucial. Control plans and statistical process control (SPC) techniques play a vital role in ensuring that processes remain stable and within acceptable limits.
Training and change management
Achieving and sustaining higher Sigma Levels is not merely a technical endeavor; it also requires a strong commitment to training and effective change management. Empowering employees with the knowledge and skills necessary to implement Six Sigma principles is crucial for success. For teams new to Six Sigma, our six sigma yellow belt certification program provides foundational knowledge to support process improvement initiatives.
Comprehensive Six Sigma certification and training programs, spanning Green Belt, Black Belt, and Master Black Belt certifications, equip individuals with the tools and methodologies to drive continuous improvement.
These programs not only impart technical expertise but also foster a culture of problem-solving and data-driven decision-making.
Effective change management strategies, including clear communication, stakeholder engagement, and leadership support, ensure that Sigma Level improvements are embraced and sustained across the organization.
Ongoing Sigma-level tracking and reporting
To maintain momentum and ensure accountability, it is essential to establish robust processes for tracking and reporting Sigma Levels across the organization.
Regular progress updates, dashboards, and performance reviews help to reinforce the importance of Sigma Level improvement and celebrate successes.
By consistently monitoring and communicating Sigma Levels, organizations can identify areas that require additional attention, allocate resources effectively, and foster a sense of ownership and responsibility among employees.
Sigma Level Benchmarks
As we have explored the principles and methodologies behind achieving higher Sigma Levels, it is important to understand the different benchmarks and their implications for process performance and quality.
From the basic 1 Sigma Level to the coveted 6 Sigma threshold, each milestone represents a significant achievement and unlocks new levels of operational excellence.
Interpreting Sigma Levels from 1 to 6
The Sigma Level of a process is directly correlated with the expected defect rate and yield percentage. As the Sigma Level increases, the defect rate decreases, and the yield percentage rises, reflecting higher process capability and quality.
Here is a breakdown of defect rates and yield percentages associated with different Sigma Levels:
- 1 Sigma: Approximately 691,462 defects per million opportunities (DPMO), with a yield of 30.85%.
- 2 Sigma: Approximately 308,537 DPMO, with a yield of 69.15%.
- 3 Sigma: Approximately 66,807 DPMO, with a yield of 93.32%.
- 4 Sigma: Approximately 6,210 DPMO, with a yield of 99.38%.
- 5 Sigma: Approximately 233 DPMO, with a yield of 99.98%.
- 6 Sigma: Approximately 3.4 DPMO, with a yield of 99.9997%.
These figures provide a tangible representation of the impact that Sigma Levels have on process performance and quality.
As we move from lower to higher Sigma Levels, the reduction in defects and the corresponding increase in yield become increasingly significant, underscoring the importance of continuous improvement efforts.
What process sigma level is “good enough”?
While the ultimate goal of Six Sigma is to achieve a world-class 6 Sigma Level, it is important to recognize that the “good enough” process sigma level may vary depending on the industry, product, or service in question.
For example, in the manufacturing of consumer electronics, a Sigma Level of 4 or 5 may be considered acceptable, as the impact of defects on customer satisfaction and safety is relatively low.
Examples of companies operating at different Sigma levels
To illustrate the implications of Sigma Levels, let’s examine some examples of companies operating at different benchmarks:
- Motorola, the birthplace of Six Sigma, achieved a remarkable 6 Sigma Level in its manufacturing processes, enabling it to produce high-quality products with minimal defects.
- In the healthcare industry, organizations like the Mayo Clinic and Johns Hopkins Hospital have implemented Six Sigma methodologies, striving for a 6 Sigma Level to ensure patient safety and quality of care.
- In the automotive sector, Toyota is known for its robust quality management systems, often operating at Sigma Levels between 4 and 5, contributing to its reputation for reliability and customer satisfaction.
- In the financial services industry, companies like American Express and Bank of America have leveraged Six Sigma principles, achieving Sigma Levels around 4 to 5, to streamline processes and reduce operational errors.
These examples demonstrate that while the pursuit of Six Sigma is a noble goal, organizations across various industries have found success and competitive advantage by operating at different Sigma Levels, tailored to their specific needs and customer requirements.
Striving for World-class Six Sigma Performance
While the benefits of achieving a 6 Sigma Level are undeniable, the journey towards this pinnacle of performance is not without its challenges.
Reaching a defect rate of 3.4 DPMO requires an unwavering commitment to excellence, a deep understanding of process behavior, and the ability to continuously identify and eliminate sources of variation.
One of the primary challenges in achieving 6 Sigma is the need for robust data collection and analysis.
Without accurate and comprehensive data, it becomes exceedingly difficult to pinpoint root causes and implement effective solutions. Additionally, achieving and sustaining such a low defect rate often requires significant investments in training, process improvements, and ongoing monitoring.
Another challenge lies in cultivating a culture of continuous improvement and fostering buy-in at all levels of the organization.
Achieving 6 Sigma is not a one-time effort but rather a continual journey that requires unwavering dedication and collaboration across teams and departments.
Companies at 6 Sigma levels
While achieving 6 Sigma is undoubtedly a daunting task, numerous companies have successfully reached this coveted benchmark, serving as inspirational case studies for others to follow.
One notable example is Motorola, the pioneering company that introduced the Six Sigma methodology.
Through relentless focus and a company-wide commitment to quality, Motorola achieved 6 Sigma levels in several of its manufacturing processes, setting a new standard for the industry.
Another inspiring case study is that of General Electric (GE), which embraced Six Sigma under the leadership of Jack Welch in the late 1990s.
By integrating Six Sigma principles into its operations, GE reported savings of over $12 billion in just five years, while significantly enhancing product quality and customer satisfaction.
In the healthcare sector, organizations like the Cleveland Clinic and Mayo Clinic have implemented Six Sigma methodologies, achieving 6 Sigma levels in critical processes such as surgical procedures, medication administration, and patient flow.
These case studies serve as powerful reminders that while the journey to 6 Sigma is challenging, it is indeed achievable through a combination of leadership commitment, robust methodologies, and a relentless pursuit of excellence.
Case studies
Let’s consider an example to illustrate the calculation of Sigma Level.
Suppose a manufacturing process produces widgets, and during a sample period, 25 defective widgets were observed out of a total of 10,000 opportunities for defects. The DPMO would be calculated as follows:
DPMO = (25 / 10,000) x 1,000,000 = 2,500
Using a conversion table or calculator, a DPMO of 2,500 corresponds to a short-term Sigma Level of approximately 4.6. To account for the potential long-term shift, the long-term Sigma Level would be 4.6 – 1.5 = 3.1.
This example demonstrates how organizations can quantify their process performance using Sigma Levels, enabling them to identify improvement opportunities and implement targeted solutions to enhance quality and customer satisfaction.
Final Thoughts
Sigma Level is a core Six Sigma metric and really impacts how well businesses pursue quality and satisfy customers.
Reaching higher Sigma Levels takes both challenge and reward. It involves a deep understanding of how to calculate and interpret Sigma Levels, leveraging the powerful DMAIC framework, and cultivating a culture of constant betterment.
Sigma Level’s importance as a quality measure can’t be overstated. Quantifying process capability and defect rates, provides a clear, data-based way to find areas for improvement, prioritize efforts, and track progress over time.
Constantly aiming higher with Sigma Levels translates to tangible benefits like lower costs from defects and reworks, stronger customer satisfaction, and competitive advantage in their industry.
Focus first on processes most impacting the customer experience, operational efficiency, and profits. Strategically targeting efforts maximizes returns on investments and drive real business results.
The Sigma Levels journey never truly ends. It demands ongoing learning, adaptation, and relentless dedication to process excellence.
It’s not just about hitting a number – it’s cultivating an excellence culture across the whole organization.
With this mindset, businesses unlock new performance levels, fuel innovation and lead their field. The pursuit of Six Sigma is really a quest for quality greatness.
SixSigma.us offers both Live Virtual classes as well as Online Self-Paced training. Most option includes access to the same great Master Black Belt instructors that teach our World Class in-person sessions. Sign-up today!
Virtual Classroom Training Programs Self-Paced Online Training Programs