Defects Per Unit (DPU): Driving Quality Excellence in Manufacturing
Defects per unit (DPU) is an important metric for evaluating and optimizing manufacturing processes.
DPU measures the average number of flaws found in a sample of made goods. This provides a real-world look at the quality and consistency of production.
By calculating the ratio of total defects to total units produced, DPU serves as a useful diagnostic tool. It helps companies spot quality problems, find the root causes, and implement targeted fixes.
DPU means more than just numbers. Its real significance lies in unlocking never-ending improvement and customer satisfaction.
Methodically lowering defects per unit enhances product quality, reduces waste and fosters a culture of excellence connecting with both customers and stakeholders.
Measuring DPU gives businesses insights to make manufacturing better one small change at a time. It drives quality that customers truly appreciate.
Key Highlights
- Understanding of defects per unit (DPU) as a crucial quality metric in manufacturing processes
- Detailed exploration of DPU calculation methods and interpretation of results
- Insights into leveraging DPU as a key performance indicator (KPI) for process capability analysis
- Strategies for root cause analysis and process improvement methodologies to reduce DPU
- Real-world applications and case studies showcasing the impact of DPU in various industries
- Advanced concepts such as defects per million opportunities (DPMO) and parts per million defective (PPM)
- Examination of DPU’s role in service industries and non-manufacturing sectors
- Insights into the relationship between DPU, customer specifications, and overall quality perception
This article will provide invaluable insights and actionable strategies to help you harness the power of DPU for continuous improvement and customer delight.
What is Defects Per Unit (DPU)?
Defects per unit, or DPU, is a fundamental metric in the realm of quality control, and it’s one that I’ve relied upon extensively throughout my career as a Master Black Belt.Ā
Here is the formula to calculate Defects Per Unit (DPU).
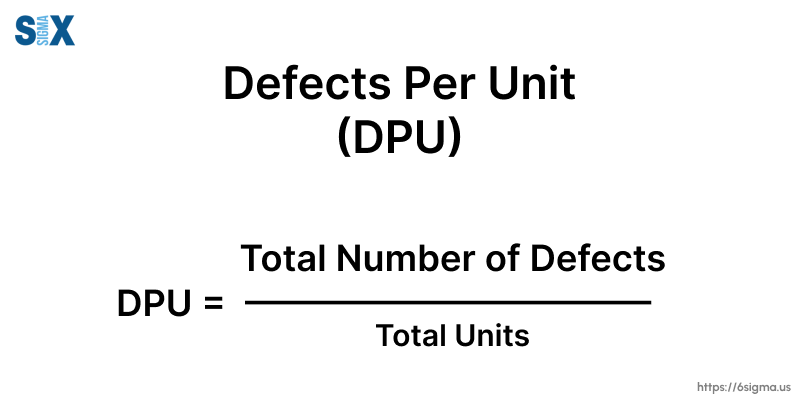
DPU quantifies the average number of defects present in a sample of produced goods, providing a clear and concise representation of the quality and consistency of a manufacturing process.
Defining Defects Per Unit
To truly grasp the significance of DPU, we must first understand what constitutes a defect. In essence, a defect is any deviation from customer specifications or expectations.
It could be a physical flaw in a product, a functionality issue, or even a failure to meet agreed-upon delivery timelines. The key factor is that a defect represents a deviation from what the customer deems acceptable.
DPU Calculation
The calculation for DPU is straightforward: divide the total number of defects identified in a sample by the total number of units produced in that sample.
For example, if a factory produces 1,000 widgets and 20 of those widgets are found to have defects, the DPU would be calculated as 20/1,000 = 0.02 defects per unit.
Example of DPU Calculation
Let’s consider a practical example to solidify our understanding. Imagine a company that manufactures smartphones, producing 10,000 units in a given month.
Upon inspection, it is found that 200 of these smartphones exhibit defects, which could range from faulty cameras to unresponsive touch screens or even cosmetic issues like scratches.
To calculate the DPU, we would divide the total number of defects (200) by the total number of units produced (10,000), giving us a DPU of 0.02. This means that, on average, each smartphone produced has 0.02 defects.
Understanding Defects and Units
While the calculation itself is straightforward, there are nuances to consider when defining what constitutes a defect and what qualifies as a unit.
These definitions can vary across industries and even within organizations, depending on the product or service being offered and the specific customer requirements.
What Counts as a Defect?
The determination of what qualifies as a defect is closely tied to customer specifications and expectations.
In some cases, minor cosmetic issues might be considered defects, while in others, only major functional flaws that impact the product’s intended use would be classified as such. It’s essential for organizations to clearly define their defect criteria and ensure consistent application across all processes.
Customer Specifications and Quality within Defects per Unit
One of the fundamental tenets of the Six Sigma methodology is that the customer defines quality.
This means that organizations must carefully analyze and understand their customers’ needs, expectations, and requirements.
Companies can only truly deliver products and services that meet or exceed expectations by aligning their processes and quality standards with these customer specifications.
Unit Definition in Manufacturing
In the manufacturing context, a unit typically refers to a distinct, complete product or component that undergoes the production process. However, the definition of a unit can vary depending on the industry and the specific process being analyzed.
For example, in the automotive industry, a unit might refer to an entire vehicle, while in the electronics sector, it could be a specific component like a circuit board or a microchip.
Importance of Defects Per Unit in Quality Control
DPU plays a pivotal role in quality control, serving as a powerful diagnostic tool and a key performance indicator for organizations striving for excellence.
Defects per Unit (DPU) as a Key Performance Indicator
One of the primary advantages of DPU is its ability to serve as a key performance indicator (KPI) for process quality.
By continuously monitoring and analyzing DPU trends, organizations can quickly identify areas of concern, pinpoint root causes of quality issues, and implement targeted improvements.
This proactive approach enables companies to stay ahead of potential problems, ensuring consistent quality and customer satisfaction.
Measuring Process Capability
DPU is also instrumental in assessing process capability, which refers to a process’s ability to produce outputs that meet specified requirements consistently.
By analyzing DPU data in conjunction with statistical techniques, organizations can determine their process sigma level ā a measure of how well a process is performing relative to customer specifications. This information is crucial for identifying opportunities for improvement and setting realistic targets for process optimization.
Normal Distribution and Six Sigma
The concept of DPU is closely intertwined with the principles of normal distribution and Six Sigma methodology. Six Sigma, a widely adopted quality management approach, aims to minimize defects and variations in processes by leveraging statistical tools and techniques.
By striving for a Six Sigma level of performance, which corresponds to a DPU of 0.00034 or 3.4 defects per million opportunities, organizations can achieve near-perfection in their processes, delivering products and services of exceptional quality.
Benefits of Tracking and Reducing Defects Per Unit
The advantages of actively monitoring and reducing DPU are multifaceted, with far-reaching implications for organizations across various industries.
Improved Product Quality
Perhaps the most obvious benefit of reducing DPU is the tangible improvement in product quality.
By minimizing defects per unit, organizations can ensure that their products consistently meet or exceed customer expectations, fostering customer satisfaction and loyalty.
This, in turn, can lead to increased market share, positive brand perception, and a competitive advantage in the marketplace.
Cost Savings and Efficiency with Defects Per Unit
Defects not only compromise product quality but also introduce significant costs and inefficiencies into the production process.
Rework, repairs, and replacements all consume valuable resources and time, leading to increased operational expenses and reduced productivity.
By actively working to reduce DPU, organizations can streamline their processes, minimize waste, and ultimately save on costs associated with defects.
Customer Satisfaction and Reputation
In today’s highly competitive market, customer satisfaction is paramount. By delivering high-quality products with minimal defects, organizations can cultivate a reputation for excellence and reliability.
This, in turn, can lead to increased customer loyalty, positive word-of-mouth referrals, and a strengthened brand image ā all of which contribute to long-term success and growth.
Defects Per Unit (DPU) in Services and Non-Manufacturing Sectors
While DPU is often associated with manufacturing processes, its applicability extends far beyond the realm of physical goods production.
Defects in Service Delivery
In the service industry, defects can manifest in various forms, such as delays, errors, or failures to meet agreed-upon service levels. For example, in the hospitality sector, a defect could be a delayed check-in process or a room service order that arrives incorrect or incomplete.
By adopting the DPU metric to measure service defects, organizations can gain valuable insights into the quality of their service delivery and identify areas for improvement.
Service Quality Metrics
Just as in manufacturing, the service industry relies on various quality metrics to assess performance and customer satisfaction.
While DPU remains a valuable tool, it may be complemented by other metrics such as customer satisfaction scores, net promoter scores, or customer complaint rates.
By combining these metrics, service organizations can gain a holistic view of their quality performance and make data-driven decisions to enhance their offerings.
Defects per Opportunity
In the service context, the concept of “defects per opportunity” (DPO) may be more relevant than DPU. DPO considers each step or interaction within a service process as an opportunity for a defect to occur.
By tracking and reducing DPO, service organizations can identify and address specific pain points in their processes, ultimately improving the overall customer experience.
Strategies for Reducing Defects Per Unit
Reducing DPU is a continuous journey that requires a systematic approach and a commitment to continuous improvement.
Root Cause Analysis of Defects
The first step in reducing DPU is to identify and understand the root causes of defects within a process.
This involves thoroughly analyzing defect data, conducting investigations, and leveraging tools such as cause-and-effect diagrams, process mapping, and statistical analysis.
Organizations can develop targeted solutions and prevent future occurrences by pinpointing the underlying factors contributing to defects.
Process Improvement Methodologies for Defects Per Unit
Once root causes have been identified, organizations can leverage various process improvement methodologies to implement effective solutions.
The DMAIC (Define, Measure, Analyze, Improve, Control) approach, which is central to Six Sigma, provides a structured framework for identifying opportunities, analyzing data, implementing improvements, and sustaining gains.
Lean manufacturing principles, which focus on eliminating waste and optimizing flow, can also be instrumental in reducing DPU.
By streamlining processes, minimizing non-value-added activities, and fostering a culture of continuous improvement, organizations can create an environment conducive to reducing defects and enhancing quality.
Statistical Process Control (SPC)
Statistical process control (SPC) is a powerful tool that organizations can employ to monitor and control process performance over time.
By establishing control limits and monitoring process variables, SPC enables early detection of deviations and facilitates proactive interventions before defects occur.
This approach not only helps reduce DPU but also promotes process stability and predictability, leading to consistent quality outputs.
Defect Prevention vs. Detection
While defect detection and rectification are essential components of quality control, a proactive approach focused on defect prevention can yield even greater benefits.
Defect Prevention Techniques
Defect prevention techniques aim to identify and address potential sources of defects before they manifest in the production process.
These techniques may include design for manufacturability (DFM) principles, which involve optimizing product designs for ease of manufacturing and minimizing potential quality issues.
In-Process Defect Detection Methods
Despite preventive measures, some defects may still occur during the production process.
In-process defect detection methods, such as statistical process control (SPC), inline inspections, and automated monitoring systems, can help identify defects as they occur, enabling timely corrective actions and minimizing the impact of defects on downstream processes or final products.
Final Inspection and Rework
While not as desirable as prevention or in-process detection, final inspection, and rework processes can serve as a last line of defense against defective products reaching customers.
By conducting thorough final inspections and implementing efficient rework procedures, organizations can reduce the risk of shipping defective products and maintain high levels of customer satisfaction.
Applications and Case Studies of Defects Per Unit
The importance of DPU and its impact on quality and customer satisfaction can be observed across various industries and sectors.
Defects Per Unit (DPU) in Automotive Manufacturing
In the automotive industry, where safety and reliability are paramount, DPU plays a critical role in ensuring the quality of vehicles and their components.
Automakers like Ford, GM, and Toyota have implemented robust DPU tracking and reduction strategies, leveraging Six Sigma methodologies and advanced quality control techniques.
By continuously monitoring and reducing DPU, these companies have been able to enhance product quality, minimize recalls, and maintain customer trust and loyalty.
DPU in Electronics and Semiconductor Production
The electronics and semiconductor industries operate with extremely tight tolerances and stringent quality requirements. Companies like Intel, AMD, and
Samsung has made significant investments in reducing DPU through advanced process control, statistical monitoring, and rigorous defect prevention measures.
By maintaining exceptionally low DPU levels, these companies can ensure consistent performance and reliability in their products, which is essential for applications ranging from consumer electronics to mission-critical systems.
Software and IT Service Defect Rates
While DPU originated in the manufacturing context, its principles have been adapted to the software and information technology (IT) service industries as well.
Companies like Microsoft, Google, and IBM have implemented sophisticated defect tracking and resolution processes, leveraging DPU-like metrics to measure and improve the quality of their software products and IT services.
By continuously reducing defect rates, these companies can provide more stable and user-friendly experiences, enhancing customer satisfaction and fostering trust in their digital offerings.
Conclusion
Defects per unit (DPU) have real transformative power as a catalyst for quality success. This simple metric serves as a useful diagnostic tool, allowing businesses to find quality issues, pinpoint root causes, and implement targeted fixes.
By methodically lowering DPU over time, companies across industries have unlocked many perksāfrom cost savings and improved efficiency to stronger customer loyalty and competitive edge.
DPU’s impact goes beyond numbers. It opens the door to endless progress by cultivating an excellence-focused culture throughout the whole organization.
Lowering DPU is a journey without end. It takes commitment to constant improvement, data-guided decisions, and an unrelenting focus on satisfied customers.
Using methods like DMAIC, Lean principles, and stats process control lets businesses develop a holistic flaw-reduction approach ensuring everything aligns with quality excellence.
DPU’s importance will only grow in the future as a cornerstone of quality management and process upgrading.
With openness to ongoing learning and change, organizations can stay ahead of shifting demands and markets to keep products and services top-quality.
SixSigma.us offers both Live Virtual classes as well as Online Self-Paced training. Most option includes access to the same great Master Black Belt instructors that teach our World Class in-person sessions. Sign-up today!
Virtual Classroom Training Programs Self-Paced Online Training Programs