The Toyota 3M Model: Unlocking Lean Manufacturing Mastery
Companies always look for ways to smooth out their work flows, remove wasted effort and maximize productivity. At the core of this objective lies the famous Toyota 3M Model, a time-tested framework that transformed manufacturing for many industries.
The Toyota 3M Model, based on the groundbreaking ideas behind Toyota’s Production System, zeroes in on pinpointing and solving three main obstacles standing between work and efficiency: Waste, Imbalance and Overdoing It.
By methodically handling these three related issues, businesses unlock their full capability while also nurturing an attitude of constant upgrading. This delivers unbeatable value to their customers through streamlined, optimized operations.
Over the long haul, the 3M Model typically improves quality and cost advantages when properly applied. Its proven success stems from focusing resources on what really moves the needle versus nonessential activities.
Key Highlights
- An overview of the Toyota 3M Model: Muda (waste), Mura (unevenness), and Muri (overburden)
- Exploring each “M” and its impact on business processes
- Proven strategies for identifying and eliminating Muda, managing Mura, and preventing Muri
- Integration of lean principles and tools, including Value Stream Mapping, Kaizen, 5S, Kanban, and more
- Case studies showcasing successful implementations of the 3M Model across industries
- Insights into the future of lean manufacturing and the evolving role of the 3M Model
- Practical tips and best practices from a Master Black Belt with extensive industry experience
What is the Toyota 3M Model?
The Toyota 3M Model is a comprehensive framework that lies at the heart of the Toyota Production System (TPS), a pioneering philosophy that has revolutionized the way we approach manufacturing and process improvement.
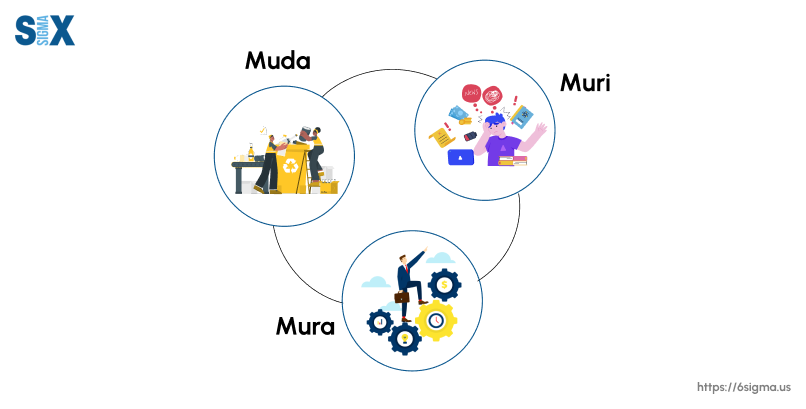
Developed by the Toyota Motor Corporation in the latter half of the 20th century, this model has become a cornerstone of lean manufacturing principles, providing a structured approach to identifying and eliminating waste, variability, and strain within complex operations.
Origins of the Toyota Production System
The roots of the Toyota 3M model can be traced back to the post-World War II era when Japan was in a state of rebuilding.
Faced with limited resources and a pressing need for efficiency, the Toyota Motor Corporation embarked on a journey to streamline its production processes.
Under the visionary leadership of Taiichi Ohno and Shigeo Shingo, Toyota developed a revolutionary system that challenged traditional mass production methods.
The Toyota Production System (TPS) was born out of the relentless pursuit of waste elimination and continuous improvement. It emphasized the principles of just-in-time production, built-in quality, and respect for people ā concepts that were groundbreaking at the time.Ā
The TPS quickly gained recognition for its ability to produce high-quality products with minimal waste, setting the stage for the broader adoption of lean manufacturing principles worldwide.
Understanding The 3Ms: Muda, Mura, and Muri
Muda (Waste)
Muda, the Japanese term for waste, lies at the core of the Toyota 3M model. It represents any activity or process that fails to add value from the customer’s perspective, consuming resources without contributing to the desired outcome.
Identifying and eliminating muda is crucial for optimizing operations, reducing costs, and enhancing overall efficiency.
Types of Muda
The Toyota Production System recognizes seven commonly encountered types of muda:
- Defects: Products or services that fail to meet quality standards, resulting in rework, scrap, or customer dissatisfaction.
- Overproduction: Producing more than what is required by the customer, leading to excess inventory and associated costs.
- Waiting: Idle time spent by employees or equipment due to bottlenecks, lack of synchronization, or inefficient material flow.
- Non-Utilized Talent: Failing to leverage the full potential and creativity of employees, resulting in lost opportunities for improvement.
- Transportation: Unnecessary movement of materials, products, or information, which adds no value and increases the risk of damage or loss.
- Inventory: Excess raw materials, work-in-process, or finished goods, which tie up capital and can lead to obsolescence or spoilage.
- Motion: Unnecessary movement of people or equipment, which can cause fatigue, safety hazards, and inefficiencies.
Identifying and Eliminating Muda
Identifying muda requires a keen eye for detail and a deep understanding of the processes involved. Value Stream Mapping, a powerful lean tool, can help visualize the flow of information and materials, making it easier to pinpoint areas of waste.
Additionally, techniques like Gemba walks (observing processes firsthand) and employee engagement can provide valuable insights into hidden forms of muda.
Once identified, muda can be addressed through various lean tools and methodologies, such as 5S (Sort, Set in Order, Shine, Standardize, Sustain), Kaizen (continuous improvement), and Poka-Yoke (mistake-proofing).
Mura (Unevenness)
Mura, or unevenness, refers to the variability and inconsistencies that can disrupt the smooth flow of work.
This can manifest in various forms, such as fluctuations in customer demand, variations in product mix, or inconsistencies in process steps.
Mura can lead to imbalances in workloads, accumulation of work-in-process inventory, and potential bottlenecks, all of which contribute to inefficiencies and waste.
Common causes of mura include:
- Fluctuations in Customer Demand: Seasonal variations, market trends, or changes in customer preferences can create uneven demand patterns, making it challenging to maintain a consistent production rate.
- Product Variation: Producing a diverse range of products with varying specifications, materials, or processes can introduce variability into the workflow.
- Inconsistent Processes: Lack of standardization in processes or variations in employee skills and methods can lead to inconsistencies in cycle times, quality, or output.
Managing Mura (Heijunka, Kanban, JIT)
To address mura and achieve a more consistent and stable workflow, organizations can employ several lean techniques:
- Heijunka (Production Leveling): This principle involves smoothing out production by creating a more consistent schedule and workload, reducing the impact of demand fluctuations.
- Kanban: A pull system that controls the flow of materials and information based on actual customer demand, minimizing overproduction and inventory buildup.
- Just-in-Time (JIT): A production philosophy that aims to produce the right parts, at the right time, in the right quantities, reducing waste and enhancing flexibility.
By implementing these strategies, organizations can better manage mura, achieve a more predictable workflow, and minimize the negative impacts of variability on their operations.
Muri (Overburden)
Muri, or overburden, refers to the strain placed on people, equipment, or systems beyond their reasonable capacities. When muri is present, it can manifest in various forms, including:
Breakdowns: Increased frequency of equipment failures or malfunctions due to excessive strain or lack of proper maintenance.
Burnout: Employee exhaustion, stress, and disengagement resulting from consistently working beyond their physical or mental limits.
Absenteeism: Higher rates of employee absences due to illness, injury, or emotional distress caused by overwork or unreasonable working conditions.
Quality Issues: Increased defects, errors, or non-conformities in products or services due to fatigue, inattention, or rushed processes.
Recognizing these signs is crucial for identifying the presence of muri and taking corrective action before more severe consequences occur.
Preventing Muri
To prevent muri and promote a safe, sustainable, and efficient work environment, organizations can implement various strategies:
- Standardized Work: Establishing consistent and documented procedures for tasks, ensuring that employees are not overexerting themselves and that processes are optimized for efficiency and ergonomics.
- Total Productive Maintenance (TPM): A systematic approach to maintaining and improving the integrity of equipment through regular maintenance, operator involvement, and continuous improvement.
- Autonomation (Autonomation): Implementing intelligent automation and mistake-proofing mechanisms that prevent equipment from continuing to operate when defects or abnormalities are detected, reducing the risk of overburden and potential damage.
By adopting these practices, organizations can strike a balance between productivity and employee well-being, ensuring that people and equipment operate within their designed capabilities while maintaining a sustainable and efficient workflow.
Implementing Lean Principles with the Toyota 3M Model
The Toyota 3M Model serves as a powerful foundation for implementing lean principles within an organization.
By addressing the three interrelated challenges of muda, mura, and muri, this model provides a comprehensive approach to continuous improvement and waste elimination.
However, simply understanding the concepts is not enough; successful implementation requires a systematic approach and the utilization of proven lean tools and techniques.
Value Stream Mapping
One of the most effective tools for identifying and addressing muda, mura, and muri within a process is Value Stream Mapping (VSM).
This lean technique involves visualizing the entire flow of information, materials, and processes, from the initial raw materials to the final product or service delivery.
By mapping out the current state of operations, organizations can pinpoint areas of waste, unevenness, and overburden, as well as identify opportunities for improvement.
Kaizen and Continuous Improvement
At the heart of lean principles lies the concept of Kaizen or continuous improvement.
This philosophy encourages a relentless pursuit of perfection, empowering employees at all levels to identify and implement incremental improvements daily.
By fostering a culture of Kaizen, organizations can continuously address muda, mura, and muri, ensuring that processes remain streamlined, consistent, and sustainable.
Through Kaizen events and regular improvement cycles, teams can analyze data, brainstorm solutions, and implement countermeasures to address the root causes of waste, variability, and overburden.
This iterative approach not only enhances processes but also cultivates a mindset of problem-solving and ownership among employees, driving lasting cultural transformation within the organization.
Lean Tools and Techniques
The Toyota 3M Model is supported by a robust arsenal of lean tools and techniques, each designed to tackle specific aspects of muda, mura, and muri.
From the foundational 5S methodology (Sort, Set in Order, Shine, Standardize, Sustain) to advanced techniques like Poka-Yoke (mistake-proofing) and Single-Minute Exchange of Die (SMED) for rapid changeovers, these tools provide practical solutions for optimizing processes and eliminating waste.
For instance, the 5S system helps create an organized and visually controlled work environment, reducing motion waste and improving productivity.
Poka-Yoke, on the other hand, focuses on error-proofing processes, minimizing defects, and ensuring consistent quality.
SMED techniques enable faster changeovers, reducing setup times and addressing unevenness in production schedules.
By strategically combining these lean tools and techniques, organizations can effectively address the three Ms of the Toyota 3M model, streamlining operations, enhancing efficiency, and delivering superior value to their customers.
Benefits of the Toyota 3M Model
The implementation of the Toyota 3M Model has proven to be a game-changer for organizations across various industries.
By systematically addressing muda, mura, and muri, this framework not only enhances operational efficiency but also drives substantial improvements in productivity, cost savings, and customer satisfaction.
Improved Efficiency and Productivity
One of the most profound benefits of the Toyota 3M Model is its ability to streamline processes and eliminate non-value-added activities.
By eliminating muda (waste), organizations can optimize their workflows, reducing lead times and increasing throughput.
This, in turn, translates into improved productivity and higher output with the same or fewer resources.
This balanced approach not only enhances productivity but also fosters a more engaged and motivated workforce, further contributing to overall operational excellence.
Reduced Costs and Waste with Toyota 3M Model
The Toyota 3M Model’s focus on waste elimination and continuous improvement directly impacts an organization’s bottom line.
By reducing or eliminating muda, such as overproduction, excess inventory, and defects, organizations can significantly cut costs associated with rework, scrap, and unnecessary consumption of resources.
This lean approach enables organizations to operate more efficiently, reducing their overall operational costs and improving their profitability.
Enhanced Quality and Customer Satisfaction
Delivering high-quality products and services is a fundamental pursuit for any organization, and the Toyota 3M Model provides a robust framework for achieving this goal.
By identifying and addressing muda, such as defects and overprocessing, organizations can significantly improve their quality standards and consistency.
This commitment to quality translates into increased customer satisfaction, strengthening brand loyalty and fostering long-term business success.
Case Studies and Examples of the Toyota 3M Model
While the Toyota 3M Model originated within the automotive industry, its principles and methodologies have proven to be universally applicable, driving transformative results across a wide range of sectors.
Through some case studies and examples, we can gain a deeper appreciation for the impact of this powerful framework.
Toyota’s Success with the 3M Model
It would be remiss not to highlight the remarkable success story of the Toyota Motor Corporation itself, the birthplace of the 3M Model.
Through the relentless pursuit of waste elimination and continuous improvement, Toyota has consistently ranked among the world’s most efficient and profitable automakers, setting industry benchmarks for quality, reliability, and innovation.
The implementation of the Toyota Production System (TPS), anchored by the 3M Model, has enabled Toyota to achieve unparalleled levels of operational excellence, delivering high-quality vehicles with minimal waste and exceptional efficiency.
This success has inspired countless organizations worldwide to adopt lean principles and embrace the transformative power of the 3M Model.
Implementing Toyota 3M Model in Other Industries
While the origins of the Toyota 3M Model lie in manufacturing, its principles have transcended industry boundaries, yielding remarkable results across diverse sectors:
Healthcare
Hospitals and healthcare providers have embraced lean methodologies to streamline patient flow, reduce wait times, and minimize medical errors, ultimately improving patient care and satisfaction.
Financial Services
Banks and financial institutions have implemented lean principles to optimize back-office operations, enhance customer service, and reduce processing times, improving overall efficiency and competitiveness.
Retail
Lean initiatives within the retail industry have focused on optimizing supply chain management, reducing inventory levels, and enhancing in-store experiences, resulting in cost savings and improved customer satisfaction.
Government
Public sector organizations have adopted the Toyota 3M Model to streamline administrative processes, reduce bureaucracy, and enhance service delivery, improving operational efficiency and accountability.
These examples demonstrate the versatility and universal applicability of the Toyota 3M Model, underscoring its potential to drive transformative change across industries and sectors.
The Future of Lean Manufacturing and the Toyota 3M Model
The Toyota 3M Model will undoubtedly continue to evolve and adapt to the changing business operations.
Emerging technologies, such as automation, the Internet of Things (IoT), and advanced data analytics, present new opportunities for organizations to further optimize their processes and eliminate waste.
However, the core principles of the 3M Model ā identifying and addressing muda, mura, and muri ā will remain integral to any successful lean transformation.
The ability to continuously improve, adapt, and innovate will be the key to sustaining a competitive edge in an increasingly and rapidly changing business environment.
Conclusion
The Toyota 3M Model, with its focus on waste, imbalance and overwork, has proven itself as a true game-changer for running things efficiently.
By laying out clear steps to find and fix unnecessary effort, inconsistencies and overload, this approach has helped countless companies streamline how work flows, lower expenses and better please customers.
Through smart strategies, tools and techniques, organizations effectively address the linked challenges outlined in the 3M Model. This nurtures a culture of constant upgrading.
Examples show how widely this powerful framework applies. No matter the industry, its priorities of eliminating fat, refining processes and respecting people deliver.
The Toyota 3M Model will keep progressing and adapting, embracing new tech and workforce needs.
But its core principles of removing waste, optimizing methods and valuing individuals remain essential for continuous progress and long term success, guiding smooth operations anywhere.
SixSigma.us offers both Live Virtual classes as well as Online Self-Paced training. Most option includes access to the same great Master Black Belt instructors that teach our World Class in-person sessions. Sign-up today!
Virtual Classroom Training Programs Self-Paced Online Training Programs